Introduction: The Revolve Electric Lawn Mower - Made From Recycled Components!
I wanted to share our electric lawn mower with you all. It was designed and built by my engineering students at Wachusett Regional High School. We were state finalists for the Samsung Solve for Tomorrow competition this past year and although we didn't move forward to be national finalists I thought that the Instructables community would appreciate the work my students and I did on this.
Our main goal was to make something more powerful than the typical mowers on the market yet made from mostly recycled materials that are easy to come by. Throughout the process my students learned a number of skills ranging from:
- Engineering design and 3D rendering
- MIG welding
- Grinding and sanding metals
- Cutting metals
- Motor and battery design
- Electrical wiring and solid state switches
- Prototyping and the engineering design process
Once we get some real grass here in MA we are going to put this to the test and see how long the battery will ultimately last. I hope you enjoy our little story about the Re-Volve Mower!
Supplies
- motor arbor to threaded shaft
- Bayite Power Meter
- 48v 10ah battery and charger
- 48v DC motor example (for the life of me I can't find the exact motor we purchased to make this work, but this could work with some modification)
Step 1: Our Idea
It seems like by the time the end of summer and fall roll around folks are sick of their cruddy lawn mowers no longer starting, leaking oil, or just plain not working anymore. That's when you start to see mowers along the curbs, posted for free on Craigslist and Facebook Marketplace and, sadly, dumped along the side of the roads in our local forests. We all seemed to notice this during the past fall and decided there had to be something we could do with the old lawn mowers. Internal combustion engines, while powerful, are noisy, stinky, inefficient, and a hassle for most folks to maintain. We figured we could use the old mowers and convert them to clean and efficient electric machines.
Step 2: The Mowers Arrive!
We wanted to get the community as involved as possible in this project so we sent an all call out to the staff at our school for their no longer wanted / no longer running mowers. Amazingly we received 17 mowers... way more than we anticipated. The first step for us was to determine which mowers were worth fixing up as is, which ones were completely useless (rotten decks and what not), which were good for parts, and which were perfect for an electric conversion. The students removed the motors from those that were not worth fixing up, and stripped down the mowers to just a deck with wheels and a handle.
Step 3: Preparing the Mower Bodies
The next step was to clean up the bodies of the mowers. Using angle grinders and sanders the mowers were prepped to be welded and painted.
Step 4: Using Fusion360 to Design the Mower Prototype
The students used Fusion360 to do the bulk of the design work on the mower prototype. We needed to have something that would clearly represent what we planned on building. This was because we wanted to share our idea with the greater community to help drum up support. We did not have all of the necessary tools to disassemble the mowers and we still needed a battery to run the machine. We used the model developed in Fusion360 to show prospective supporters and to help guide our final build. We had additional help with design ideas by working with Zac and Jesse Cataldo from the Now You Know Channel (you will see a cameo they did for us in our video). Jesse had built an electric lawn mower and did a whole series on his adventures with the lawn mower design he worked around. These guys were extremely helpful with this entire process!
Step 5: Welding the Motor Mounting Plate
We really wanted to make the majority of the mower out of fully recycled components, and we did a fantastic job reaching for that goal. Of course when using recycled components you are working with stuff that was already discarded, so there are some ugly warts that you have to deal with. One instance of this was when the students tried to use an old trailer rim as a mounting plate for the mower. It seemed to good to be true, the rim was a perfect size for the motor we decided on (more on that in a moment) and it fit perfectly in a spot within the mower. The students ground the rim in half, ground it down and prepped it for the motor and for welding to the mower. The problem was that the rim was delaminating and would not allow the motor to sit flush without a lot of work. The students decided it would be best to scrap the rim and instead use a piece of recycled sheet metal we had. They cut it to shape using an angle grinder, drilled a center hole for the motor shaft, found the mounting holes for the motor housing, drilled those and then welded the plate to the motor using our MIG welder.
Step 6: Motor Choices
This was one of the main purchases for this project, although they were both used motors... so we are still on that recycling vibe. I decided to purchase a 40V motor that was originally dedicated to an electric mower. This was a three phase motor and could be used with a motor controller. The other motor was a random find. It was a 48v high RPM motor with a keyed shaft. Ultimately we decided to go for the motor with the keyed shaft since we felt it would be the easiest to attach a motor arbor and blade to and it was a more powerful motor too. The only problem was that getting the blade and motor to be friends was harder than we expected, more on that in a minute.
Step 7: Battery Choices
We now had a 48v motor but needed a 48v power source. Zac and Jesse helped us make a connection with the Big Battery company who donated an amazing 48v battery to our class. Sadly the battery came in much later than we originally anticipated (not their fault) and we had to use some old e bike batteries I had kicking around. The batteries are 48v 10ah. We used XT60 connections on the motor and the battery and we used an old Craftsman toolbox to safely inclose them in at the front of the mower. This is more of a temporary fix until we make a permanent enclosure attached to the mower directly. I'll go into more detail on the monitoring system they created for the mower in a bit, but let's first get that blade connected to the mower!
Step 8: Motor Meets Blade
Getting the blade SAFELY attached to the motor was definitely something that threw us for a loop. We had plenty of blade to motor couplers from the mower motors we disassembled but they were all for 7/8" motor shafts and our motor had a 1/2" shaft. That's a BIG difference! What we ultimately decided on was to use a motor arbor to threaded shaft. We could then take the 7/8" motor arbor and weld it right to the arbor shaft, leaving enough threads available to attach the blade securely.
Step 9: Electronics Testing and Experimenting
A big part of this project was investigating ideas that could be used with the mower to make it both more efficient and user friendly. We were already working on a project involving Arduino microcontrollers and it seemed like the mower would be a great transition to move towards after learning basic coding and components with Arduino. The students investigated the use of current sensors, gps modules, dc-dc converters / regulators, and even lithium ion battery design. This gave us a chance to see how we could utilize currently available shields and components to make the mower that much better.
Step 10: Painting the Mower Body
One of our students builds and designs surfboards. He uses his own spray setup to finish the boards and he generously brought it in to put a finish on our mower bodies. He was able to purchase a low VOC water-based paint at the local paint store and use it to put a finish on some of the mower bodies.
Step 11: Energy Monitoring System
We used the same power meter I have used on my other electric machines, the Bayite Power Meter. You can check out more details on how to wire this with my previous Instructables, but overall you need to connect the negative side of your battery to one side of the provided shunt and then need to connect the other side of the shunt to your negative side of your motor. You then need to connect the display to both your positive side of your battery and the negative side of your battery to power the unit. The amount of current will be measured as it passes along the negative wire across the shunt. We only quickly prototyped a box for the mower and installed a 30 amp DC switch to turn the unit on and off. Nothing fancy and with more time (likely next school year) we will 3D print a proper box and install an ignition switch and on/off/on switch to have two power settings at least. The wires were run through some split channel plastic tubing from the battery box up to the display.
Step 12: Final Design and Future Thoughts
Please keep in mind that this was a project designed and built by high school students. It is not perfect, but I can honestly say that they were in control of the whole process. There are things we need to add / change. For one we need a tip switch that prevents the machine from running when it is tipped over at all. We would also like to incorporate the original throttle bar into the design and make that the secondary on/off switch which would make the blades spin once the previous switch is thrown. The thing is crazy quiet, but we need to push it through some thick grass and see if it is as powerful as it needs to be. With the current setup it will be able to pull upwards of 1500 watts of power... which is a lot for an electric mower! Ultimately we want to build a dedicated battery or install the one provided by Big Battery unless that one goes to next year's electric vehicle we are planning on building!
This was a fantastic project to introduce my students to welding, engineering design, electronics design, battery and motor compatibility, and even video editing and design since we created our explanatory video for the entire project. So far we only have one semi-complete mower built, but we have another 12 mower bodies ready to go for next year's classes. We're hoping to make a simple conversion kit next year that quickly converts an old gas powered mower into an electric mower.
Thanks for checking out our project and a big shout out to all of my awesome Wachusett Mountaineer Engineers!
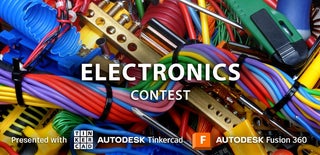
Runner Up in the
Electronics Contest