Introduction: The Tesla Meets Edison Nixie Clock
The idea of this clock came from thinking about what Nikola Tesla and Thomas Alva Edison could have produced were it not for their divergence in the field of electrical invention.
Tesla was a former employee of Edison's and was considered a genius as he had the ability to formulate designs from a few sketches as he had an eidetic mind whereas Edison had a large team of assistants who were responsible for making his ideas work. Tesla despite all of his inventions ended up destitute while Edison made a fortune from his.
Had it not been for these two gentlemen our world would be a very different place from what it is today.
The clock itself runs on AC converted to DC so it would satisfy Edison who hated AC having had a bitter feud with another inventor, Westinghouse, the proponent of AC.
The design reflects some of the important inventions of the time, Tesla for his coils and Edison for his lights.
As my designs are off the wall and this is no different but I hope that it ties the two inventors together in my interpretation of a Tesla Meets Edison Nixie Tube Clock.
PS - I entered this for the Light competition so if you think it is worth a vote then please do so.
Step 1: A Few Things About Me.
I am by no means a skilled electronics engineer, woodworker or metal worker. I just picked things up as I went along and made all the usual mistakes before being able to get things looking half reasonable at the end of it.
I like Nixie Clocks but not those generic ones that most people see, buy a kit, buy a case, put them together and stand back, I like the ones that have imagination in their creation and reflect the ingenuity of their creators. There are some fantastically designed clocks out there made from the most ordinary of things and materials. It just takes imagination to put them all together and have something to show at the end of it. Take a look at the likes of Bad Dog Designs, Christian Monjibox, Hellboy Lantern Clock to see what I mean.
The clocks in the photo sequence are ones I have made previously. I have yet to make a clock kit in the way as it comes out the box, not even the first one I built for the Steampunk Lamp
Designs I create are the result of scribbles on bits of paper, waking up at 4 am with a great idea and then falling asleep again and forgetting it! I have a rough idea at the start of what I want to create and often I will scrap something that just does not quite lend itself to what I was thinking. Trial and error have been the way I get to the final result and I am happy to see it when it is finished.
I think that the term that really describes me is 'Tinkerer'.
This clock is no different as changes were made after parts were made and hopefully the changes were for the better, I will leave that up to you to decide as you work your way through this Instructable.
Rgds,
Roddy
Step 2: Getting Started
The Materials of the Clock
1 x Teak Plank (a former floating shelf)
50mm Oak dowel
30mm Beech Dowel
6 x Home Made Wooden Lamp Holders
6 x Home Made Tesla Coil Holders
6 x E27 Clear Glass Bulbs
6 x GNP-7AH Nixie Tubes
1 x QTC PV Electronics Clock Kit
4 PCB Stand Offs
2M x 28AWG Insulated Wire - 4 Colours Required
1M 26 way Ribbon Cable
2M x 1mm Sleeving
1 x 240v to 12vdc 1A Wall Wart PSU
3mm x 12mm Brass Cheese Head Machine Screws
300mm x 3mm x 30mm Brass Flat Bar
200mm x 14mm Brass Round Bar
1M x 8mm Clear Acrylic Tube
500mm 16mm PVC Tube
12M x 1.5mm Copper Wire
1M x 2.5mm Copper Wire
0.5mm Brass Sheet Material
Clear Varnish
Black Gloss Spray Paint
THE TOOLS USED
Hobby Milling Machine
Hobby Lathe
Forstner Bits
Milling Cutters
Lathe Tools
$10 Engraving Tool
Home Made Lichtenberg Etching Machine*
Electrolyte Solution
Dremel
Dremel Bits
Soldering Iron
Solder
Wire Strippers
Electronic Snips
Sheet Metal Snips
Vice
Orbital Sander
Sandpaper - Various Grades
Cellulose Lacquer - Spray Type
Brass Polish
Liver of Sulphur**
Epoxy Glue
Super Glue
HELPFUL LINK
* See Text In Making The Base Section
** See text in Brass Section.
Step 3: Preparing the Light Bulbs
Due to changing legislation in Europe, common light bulbs are getting hard to obtain and I had to use Halogen Energy saver E27 bulbs instead which are a tad more expensive.
A Dremel tool makes short work of preparing the bulbs as the enclosure for the Nixie tubes. You MUST wear eye protection and a dust mask when doing this as fine particles of glass are created
The first step is to remove the base contact from the E27 screw part and this was done with the thin cutting disk as the material was aluminium, some will be made from brass but it cuts that just as easily.
When it is cut it the contact will still be attached by the internal wire, just cut this off with the snips and you will have access to the stem area. There is a slender stalk of glass that need to be broken off with pliers to break the seal of the bulb.
Once the stalk is out of the way the next thing to do is remove the interior parts of the bulb. This is done with a dirt cheap electric engraving tool that I found in LIDL, similar will be available in the likes of Wallmart etc. It has a carbide tip that is ideal for this task.
You will see from the photograph that there is a curve in the glass before the sealing compound, this is where you want to start. It takes very light pressure and just a couple of seconds before it breaks away from the globe part and will hang inside it by its connection wire. Using the engraving tool gradually chip away at the edge of the hole to enlarge it enough to remove the interior part with long nose pliers.
At this time using the Dremel with a grinding stone you can enlarge the hole so that your nixie tube can fit inside easily. Do not use too hard a pressure in doing this and take your time otherwise you might break the glass envelope and have to start again with another bulb.
Most bulbs have a maker and rating print on the glass, you can remove this with cellulose thinners and some kitchen paper very easily. To clean the dust from inside the globe just wash them out with a dilute solution of washing up liquid and rinse well. When you have them all done, put them aside to dry and avoid getting broken.
The wooden lamp bases were made from Oak dowel on the lathe and on shaping them burning took place which I left as it gives a good effect on them but I ended up spay painting them black. The holes were drilled on my milling machine using a rotary table at 120 degrees apart and then the curve was milled flat for the fixing screw but this can be done by hand or you can buy some lamp bases to save you the trouble of making them.
Step 4: Making the Wooden Base
The base for this clock is made from a teak plank that used to be a floating shelf at one time so it had slots from the back for the support arms as you can see in the first photograph.
The cavity for the circuit board is much longer that any previous one on my clocks as access is needed for the QTC bases that the Nixie Tubes are fitted to as they are not directly fitted to the board.
I am not going into details of the cavity creation as you can take a look at some of the previous Instructables I have made for Nixie Clocks as the details are there. With this clock there are a lot of through holes from the top surface for the Nixie tubes and the associated parts that are used in the clock along with the connection plate on the rear. As I have said in previous clock builds, the through holes are made first to prevent tear out of the wood which can happen if you make them after the cavity. The extra slot you see on the rear was where a support slot was and it will get a brass name plate fitted to hide it.
TORTURING WOOD!
The decoration on the base section was done by the Lichtenberg process which is similar in effect to that produced by lightning. This is NOT TO BE DONE if you have no understanding of the risks involved and I accept no responsibility of injury or death resulting from anyone attempting this process. It involves voltages in excess of 2 kV being applied to an electrolyte solution on the wood and creates electrical arcing that will kill you on contact.
YOU HAVE BEEN WARNED!
In the photographs is the unit I used to torture the wood into confessing. Some practitioners advocate nails, clips and clamps but I used a probe system. The connecting wires are insulated to 16 kV, the probes are 3mm brass rod with rounded polished ends, the insulation on the probes is triple encased. No risk involved says he! This is a dangerous process and as I said before, you do at your own risk and you leave me out of it unless I am in your last will and testament as a beneficiary.
The effect on the wood is varied as I moved the probes around to get an overall coverage of the Lichtenberg Effect on the top, front and ends of the base. The discolouration is from the electrolyte solution and when it had dried the 'lightening strikes' are cleaned up with a small fine wire brush to remove the carbon created and a very light sanding so as not to remove the lighter fractal patterns that developed from the process. Make sure that all the 'channels are cleaned out, even the shallow ones as the carbon needs to be removed to get the best effect. Spraying with cellulose lacquer really brings up this feature as well as the exposed grain of the wood created by the process. Compare the final case with the blank at the start of this photograph sequence and you will see the vast difference that this process has achieved on a rather plain looking plank of wood. When a real Tesla Coil is operating there are 'lightning bolts' everywhere so why not have them on the case?
With the lamp holders painted additional coats of cellulose are applied and now the wood stands out more with the etching showing up really well.
If you want to know about the Lichtenberg process there are numerous sites on the internet with this site being the best at describing it but again I accept no responsibility if you end up dead should you attempt it.
Step 5: The Electronics of the Clock
PV Electronics provide excellent kits for Nixie Clocks to suit all pockets, the QTC kit used here is relatively cheap and easy to build if you have some soldering skills and can read!
The QTC kits advantage is that the Nixie tubes are fitted to small circuit boards and plug into the main board. However this would have put the tubes too close together and I would not have been able to make the clock the way I had in mind so I ordered another set of the tube plugs and sockets at the same time as ordering the QTC kit from Pete Virica, the owner, and made them remote tubes by using ribbon cable to take them off the circuit board. Another issue was the height of the tubes had to be enough to display correctly inside the lamp globe so I left the leads at maximum length and insulated them before fitting a spacer between the Nixie tube and the small board before soldering them into position. There are commercial tube stand offs available but I could not find the length I needed so I just used some 16mm PVC pipe to make my own ones.
The Nixie Tubes that I have used for this clock are quite rare and hard to find but on a medium sized tube they have some of the best digits shapes of them all and a good reddish orange glow when operating. The QTC kit can use several different types of Nixie Tubes from the relatively cheap IN-14s to the more expensive GNP-7AHs that I have used and a lot more in between such as ZM1210, ZM1080, Z570M, IN8-2 and the likes. There is one tube that is nearly of the Unobtainium variety, the very beautiful ZM1177 which has a really fine mesh in front of the digits, just try finding 6 NOS (new old stock) of these! The GNP-7AH ranks second to this tube. There would be nothing to stop anyone scaling this design up so that it uses really large tubes such as Z566M, ZM1040, Z568M or IN-18s apart from finding light bulbs big enough!
The downloadable instruction for these kits are excellent as is the customer support from Pete
The QTC kit features RGB LEDs which are programmable via a separate menu from the clock function and can give a wide range of effects. To vary the colour effect that my clock uses I switched the positions of the RGB cathode leads to give 3 pairs of different colour change effects on the Nixies but on testing it was not visually acceptable and I went back to the straight RGB wiring pattern which makes the tubes and coils change in the same pattern. The circuit can support an additional set of LEDs if the current is limited by resistors to below that of the max of the 2N7000 FETs on it but you need to add more current limiting resistors for the cathodes of the extra RGB LEDs. I opted to make an off board LED assembly and drive it from the board supply with 220 Ohm dropper resistors limiting the current and using the on board PIC signals for the three colour signals. This was paralleled up to the outputs of the 2N7000s that feed the existing RGB LEDs and a nearby connection provided the +5v for the anodes. The supply wiring was hot glued to the underside of the board to secure it and the ribbon cable goes to the LEDs and the connections covered with heat shrink.
The original idea was to have the Tesla coils as shown in the photograph made on wooden formers with a silver globe but they did not look the part when against the bulb enclosures so I made a different type that is far more suited to the design - See Brass Work for details.
The internal part of the Tesla component is a clear acrylic tube with an RGB LED inserted into the bottom and the top section opaqued to give the glow effect. I had to machine the hole to 5mm in order to fit the LED and used sandpaper to make the visible part opaque. The coil is fitted by drilling a small hole in the tube and bending the end of the copper wire to 90 degrees to secure it before wrapping the coil. The other end is held in place by applying super glue to the end of the tube before making the final 5 or 6 wraps of the copper wire and holding it until the glue sets before cutting off the excess wire.
The last photograph shows the wiring that goes into the clock with it just needing the board mounted inside the cavity. The clock board had to be mounted upside down to simplify the tube connections and is fitted to aluminium hex standoffs that I made. The stand offs are fitted to the board first and then they are epoxied onto the underside of the top of the case. This determines the position of the holes in the brass control plate that is on the rear of the clock. I had a set back with the electronics when one of the anode driver transistor pairs got shorted out and blew them and the PIC. A replacement of these and the electronics were back up working again giving the desired effects with the RGB lighting effects.
As I mentioned in the Brass Work section, I had completely forgotten about the AM/PM neon indicators so these were added. It simplified things that the wiring can be soldered to the underside of the circuit board so I did not have to remove it to add them. Neon lamps do not really have polarity but if you connect one, one way and another the opposite way it will cause the other segment to illuminate, I was lucky in that I have the same segment on both operating.
There is a GPS unit that works with this clock that allows it to constantly update the time from the GPS satellite system, available from PV Electronics as a pre-built unit ready to plug in. A Wi-Fi module is also available if you cannot get GPS reception but have a Wi-Fi router in your house.
The video clip shows the effects of the RGB LEDs.
Step 6: The Brass Parts
Nothing goes better than Brass and Wood, they compliment each other no matter what species of wood you use that is why my clocks always feature brass some where in their design and the Tesla Meets Edison is no different.
To try and get something that would not have looked out of place in Nikolai Tesla's workshop I came up with the idea for these coils.
The copper coil is formed on acrylic tube as I described in the Electronics step and the brass parts were made to enhance it.
I used 0.5mm brass sheet and cut strips of varying width which were then cut into squares. These were drilled in the center for mounting in my lathe to machine them round. They are held on a 6mm Allen screw with two brass end plates and tightened up as much as possible to prevent them spinning when being machined. At first I used a standard lathe tool but this was giving burrs on the first and last washer and I changed this for a round nose cutter which gave a better finish.
You have to take this process slowly because if you try and cut too much at the start it will jam the plates and cause them to spin. Very shallow cuts are needed until you have them all rounded then you can machine as normal to get your finished diameter. I made 4 different sizes and them I enlarged the holes to 8.25mm so they would slide onto the acrylic tube. I made spacers from 14mm round brass bar with 2mm and 3mm thickness and again an 8.25mm hole to allow fitting on the acrylic tube.
All of these parts have to be polished for the next step which is mounting and glueing.
The top piece is made from 14mm brass round bar again and is machined on the lathe first and then on the milling machine to give the 'windows' for the LED glow to emanate from for effect. I tend to make things up as I go along having a general idea of what I am looking for and these parts were free designed as I worked on them turning out just as I saw in my mind's eye!
First of all the round bar is drilled out to 8.25mm to a depth of 14mm and then the 'window' section is reduced to 10mm with a sweep back to 14mm. Leaving a ridge of 1mm the top part is turned down to 6mm with a bigger sweep and then all of it is subjected to emery paper to reduce machining marks. The top part of this is turned down to a small nipple for a brass clamp where the connection to the top of the lamp is made. On the milling machine the part is still attached to the bar and a few passes to the depth required opens the window on one side. To get the other side horizontal I reverted to an old trick of holding a 6" ruler against the already cut face and then rotating it until it was on the underside and horizontal again measured against the side of the vice. Not precision work but does the trick. A rotary table would be the correct way but that involves me removing the chuck from my lathe and spending about 1/2 an hour each time setting it up for true then removing the chuck and putting it back on the lathe to repeat the process as I had only one bar of 14mm brass and only one 3 jaw chuck!
Small nipples with base plates are made for glueing to the top of the lamp globes. The underside of these are dished to make a good fit against the glass of the lamp for attaching.
The connection part is made from scrap brass cut into strips and 2.5mm copper wire. I folded the strips over the shank of a drill that matched the nipples of the coils and globes and when it was in a 'U' shape I put it in a vice and closed the jaws while holding it down to get a tight loop. The tags were cut to length and the ends of the wire were flattened before soldering them all together and shaping the loops. These along with the copper wire of the coils has been antiqued using Liver of Sulphate solution. You need to wear eye protection and rubber gloves while doing this and also have good ventilation as it pongs quite a bit. Once aged it is then washed and given a light polish with very fine wire wool to produce a burnished effect on the high areas. Spraying this with lacquer would prevent it tarnishing but I left it as it was to get more aged looking as the clock gets older.
The base section cover plate was a bit of an issue as the remains of the brass sheet were smaller than the opening so I 'stitched' two parts together with pop rivets. To get the hole alignment correct I sandwiched the three brass sheets together and drilled one set of holes. This enabled me to get the join plate accurately positioned and the other half of the base cover was just pushed up against the edge of the first one which was riveted first. When riveting thin materials like this there is a tendency to cause deformation so you need to work from both ends of the join decreasing the gap as you rivet. The pop rivets were too long so I took the rivet off the stalk and pushed it through a hole in an aluminium plate of the thickness needed to get the length and cut of the excess with the Dremel disk before refitting it to the stalk and using it.
The feet are made in two parts with the circular part made from 4mm brass flat bar in the same way as the washers of the Tesla coils. A small spacer is made from 14mm round brass bar and with a countersink made in the circular part they then are screwed together into the base with a wood screw. If there is any unevenness in the feet they are easily levelled out by using the reinforcing rings that you use for securing paper in a binder by putting them between the spacer and the wooden base section.
The rear plate is made from a strip of 3mm x 30mm brass and the holes are machined to suit the LEDS and sockets of the electronics board. The shrouds are made from 14mm round brass bar as I do not like the look of having the plugs just stick out of a normal hole in the plate. Mounting holes are drilled for attaching to the base section and the whole thing is polished up to a mirror finish. The clock control buttons are recessed into this plate along with the function indicator LEDs to stop prying fingers inadvertently changing the parameter settings of the clock.The small plate that covers the shelf hole is made from the same and I engraved this with the date of the build and my name for posterity.
It wasn't until I had written this up and was looking at the photographs that I realised that I had forgotten to add the AM/PM indicators! These were made from compression olives drilled to accept a 4mm brass tube with a base turned down from 12mm round brass bar in keeping with the wire connection parts. The neon bulb leads were extended and covered with heat shrink before connecting to the circuit for the clock.
Step 7: Putting It Together.
One of the difficult parts is getting everything lined up and to help with this I had to make a jig to center the brass nipple on the lamp globe. The jig was a 50mm diameter hole in a piece of wood and a close fitting plug that I turned on the lathe with a recess for the nipple. The nipple was placed in the hole and glue applied then the lamp globe was place in position on the 50mm hole and the plug pushed up to fit the brass nipple. on with drawing the plug it left the nipple attached to the globe and this was put the right way up until the glue set. After working my way through 3 different glues I finally ended up with a bonding type as super glue, hot glue were not doing the job.
The lamp globes are fitted to their bases then the Nixie tubes are positioned and hot glued to the inside of the base section. Next the Coils were epoxy glued into position and once everything was set the link coils were shaped and fitted between the coils and the lamp globe nipples.
Next would have been the fitting of the electronics but for some reason the PIC chip fried itself after test running for 4 days with everything connected so I had to wait on a replacement PIC arriving from Pete. Once the PIC arrived it was fitted but there was an additional fault with an anode driver transistor pair which required their replacement and then the board is put into position before attaching the rear brass plate. Back on test again before closing up the base with a cover and finally completing the clock.
Step 8: The Conclusion
After all the little setbacks it looks as though it has turned out not too bad from the original idea that I had. I like the enhancement that the Lichtenberg etching has given to the base which sets it apart from the norm.
I also like the look it has of being put together in some backroom from the Tesla and Edison days instead of looking like a machine produced item bought out of a shop.
Maybe it will be a clock I will repeat but I will wait and see how it is received, you never know, I just might.
People who contribute their ideas to the Instructable site are to be commended as it opens up a whole new viewpoint for those who see them so if you have something that you think is different why not give it an Instructable and let us all see what you can do.
Thank you to all who took the time to go through this Instructable and I hope you enjoyed it.
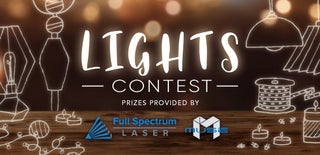
Second Prize in the
Lights Contest 2017