Introduction: The Ultimate Micro Forge/Foundry
This is my version of the micro coffee/paint can forge. I only needed something small and fairly portable but also tried to design this with acting as a small furnace for melting aluminium, brass gold etc. I also made a Youtube video to hopefully give you a better idea of what it did.
I first got the inspiration from Pask makes on youtube for his Fergus the forge pig, but also changed a few things around.
Don't forget if your going to follow this instrucable to read the step 7 about what i would do differently. It stops a lot of screw ups.
Step 1: Supplies
My aim was to try and make this as simple as possible for other people to follow, you don't need a lot of tools or consumables to make this forge. Most everything should be able to come from your recycling pile or your local hardware store.
- 2 tin cans, makes sure that one of the cans will fit neatly inside of the other.
- Fire clay (some instrucatables and other plans suggest the use of plaster of paris but this is not likely to last long)
- sand, any sand will mine came from a bag of playground sand from the hardware store
- Disposable paper/plastic cups for mixing
- Assorted spoons and mixing stick
- Standard MAPP gas burner
- A drill and bit to suit mapp gas diameter
Step 2: Prepare Your Tins
Now that you've emptied all that glorious Milo out of those tins we can begin. If your in a hurry you can simply eat the Milo but its best to mix it with milk over a 3 day weekend.
Remove the labels and make sure that the tins do indeed fit within one another, check the height difference as this will become our base layer in the bottom of the large tin. I also found it really helpful to fill the inner tin with sand and water to weigh it down, fit it in its general location within the larger tin and pour water around the gap to determine how much mix i needed in my case it was 8 cup fulls.
Step 3: Start Mixing.
I used a ratio of 50/50 sand to dry fire clay mesured by volume so approx 4 cups of sand to 4 cups of clay. I mixed them dry in a larger container and then took smaller amounts to my cup to mix with water. It helped contain the mess a bit.
It also let me work in stages rather then needing to go all at once, this design means the mixture needs to be a runny, about the consistency of pancake batter rather than stiff and stick that needs to be rammed.
Step 4: First Layer
Pour or pack the mix into the bottom of the large tin to a point where the inner tin will sit level on the top. I just sat the inner tin inside and said good enough. If your mix is too runny and the inner tin starts to sink as mine did throw it in the over for an hour or two. We're not looking to bake the clay here just dry off some excess water until the inner can sits nicely.
While waiting for it to dry might i suggest you play with a doggo, If you are not in possession of a doggo i suggest you borrow someone elses to play with (its great stress relief)
Step 5: Around the Sides
Once your base has set its time to start adding more mix. Make sure your inner can is close to the center, we can still move it a bit but once the mix starts to dry it wont budge. I also kept the sand and water mix inside to stop it from floating in the runny mix.
I added about a half cup of mix at a time to get the constancy right and try to pour evenly. By using a slightly runnier mix it helped it self level or simply tap the tides of the tin or drop it onto the bench. You want to get it until the mix is right at the top or maybe a little under, i over filled it here but as the water was driven off it settles quite a bit.
I put it back in the oven to try and speed up the drying time but its not strictly necessary. I also found pressing a paper towel to the surface with a plate helped wick the water away from the lower levels. If you choose to put it in the oven it also helps to slowly remove the water and sand mix from the inner tin to help with better heat transfer. Do this very as the mixture dries of the tin can start to float again.
Its also a great idea to do this in the sink, any mud can just be washed away and your house mates don't get mad at you for ruining their grandmothers dining table.
Step 6: Light It Up
Nows the time we've all been waiting for.
Insert the propane torch and light it up. Its best to do this for about a minute and then off to cool it down. If there's any water still in the mix you could boil it and that will be very messy.
After doing this a few times over a few days i felt comfortable enough to put it to the test of a full light up and try and get some metal cherry red.
Step 7: The Final Notes
So what would i do differently if i was to do this again?
I would use a drier mix and sort of pack it in rather than casting. It would take a lot less time to dry and id be burning withing a weekend.
I would probably add something like perlite to increase the thermal insulation of the mix. This would save probably a decent amount of fuel over a time period.
I may end up putting a better refractory material in the center tin. Either i would use pure fire clay, sodium silicate and sand or a commercial refractory that may be available in small quantity.
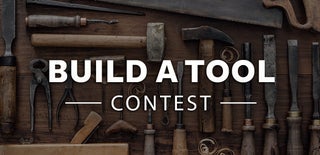
Participated in the
Build a Tool Contest