Introduction: The Valence Life System 1
Team
Collegiate entry created by Nathan Woodward and Arthur Work aided by Yadid Levis and rendered by Abhiroop Kollipara.
Objective and Constraints
We began our design process with a zealous round of due diligence; after studying the APH and Veggie extensively, we identified three areas of core functionality to address. Our team determined to focus on maximizing 3D space efficiency, accurately controlling the grow environment and automating watering the plants, and design the enclosure to collapse, minimizing its footprint during transportation and expanding to ideal growth height over the plants life cycle.
We were able to create a system that scales up incredibly well by breaking down our design into multiple modules. We were able to save space by combining several of the functional and structural elements of the machine.
Although the most obvious constraint for this competition is the 50cm cubic space, the most challenging aspect has been managing the dynamics of fluid delivery and oxygenation in microgravity. It is because of this difficulty that our first models using traditional hydroponic methods would have failed. Frustrated by the clunky profile of the plant pillows and the difficulty in adequately providing nutrients and dissolved oxygen to the plants, we were forced to come up with something new. We have developed our system of hydroponics specifically for microgravity; we are calling it Zeroponics.
Design Overview
The heart of our design is centered around a middle frame that houses the water reservoir, plants, electronics, and the rackmounts for the express cabinet. Plants’ phototropic tendency to grow towards the light in zero-gravity allowed us the freedom to explore many different and unique grow configurations for space. The benefit of our designs being modular allows for many different placements of components. We eventually concluded that arranging the plants above and below the middle frame, two biomes would utilize the 50cm cubic space most efficiently as the red romaine grows to 15-20cm in diameter and 15cm tall.
Design A - Plant Pillow:
Our configuration is similar to a mirror of the veggie’s groth area on top and bottom of our growth systems, allowing us to double the number of plants grown to 12! Red romaine grows up to 15cm, allowing two grow chambers to be stacked in a 50cm cube easily. Our stacked plant-pillow design, where one is growing “up,” and the other is growing “down,” allows us to create a unified middle section to house the electronics and a 15L reservoir. This configuration makes greater use of space by having one reservoir that needs to be refilled and reduces excess piping with it central positioning. The LEDs are on a retractable roof that raises and lowers, providing 18cm of height when fully extended for the plants to grow while controlling lighting distance.
Design B - Zeroponics:
A secondary design we created explores a plant pillow replacement that mimics deepwater and drip hydroponics. The plants are grown in a root reservoir, a mylar bag with specially designed vents to let air pass through but not water. The root reservoir has a screw-on cap for the seed pods that connects it to a root guide, which is a 3D printed lattice to guide root growth and provide air or water and nutrients. The root reservoir can function as a deep water hydroponic system where the root reservoir is filled 95% with water and the root guides are supplying oxygenated air.. The root reservoir can also function as a drip hydroponic system where the root reservoir is filled 95% with air, and the root guides are delivering water and nutrients at precise dosages directly to the roots. The nutrient dosing system is a set of syringe pumps that mix nutrient solutions into the water. This design is extremely lightweight, and with root guides and a single large root reservoir, we can take up the entire 50x50cm plane to grow 9 plants. Following the double biome configuration, we will be able to grow a total of 18 red romaine lettuce plants, triple the output compared to the Veggie!!
Supplies
BOM 1: Structures and Frame
5 Silver T-Slot 1m 1.5x1.5cm https://www.makeralot.com/t-slot-1515-aluminum-ex...
4 Body Panel White UV acrylic ⅛ in 24x24 in https://www.mcmaster.com/8505K744
2 Roof Aluminum sheet ¼ in 24x24 in 2 Roof Motor Bi-directional, 3mm metric screws (M3) mounting holes, 5mm diameter drive shaft, 24mm long, with a machined flat 4.2x4.2x4.5cm Requires 12V https://www.mcmaster.com/8505K744
1 Motor Driver Chip controls 2 bi-directional at 4.5-13.5V Requires 3.3V signal https://www.adafruit.com/product/324
1 Inner Shield PEVA clear sheet 72x72in https://www.amazon.com/Epica-Market-100-Anti-Bact...
2 Sting O Rings Silicone Rings .25 cm Dia. https://www.firemountaingems.com/itemdetails/H20B...
8 String Retractable kevlar string 48in https://www.uline.com/Product/Detail/S-11882/Key-...
1 Mylar 2 mil grade mylar sheets 4x24ft https://www.amazon.com/VIVOSUN-Horticulture-Highl...
1 Magnet Tiny Neodymium 1/8 x 1/16in https://totalelement.com/products/1-8-x-1-16-inch...
BOM 2: Air Circulation
4 Blower Fan 1.5CFM 3x3x1cm 12v, 0.060A https://www.digikey.com/product-detail/en/delta-e...
1 3-way Solenoid 3way 2position Solenoid: Power off : Port 2-3 pass , 1 is blocked ; Power on : Port 1-2 pass, 3 is blocked. ID: 2mm, OD: 4mm 48 x 20 x 21mm 12V, .19A https://www.amazon.com/uxcell-Miniature-Solenoid-...
2 2-way Solenoid 1/2" opening 3.3x1.69x2.24in 12V, .36A https://www.adafruit.com/product/997
BOM 3: Watering
1 Peristaltic pump 100mL/min flow rate 7.2x2.7x2.7cm 12 V https://www.adafruit.com/product/1150
1 Valve Connectors 40 Pack of different style connectors https://www.amazon.com/Pawfly-Aquarium-Airline-Co...
1 Tubing Silicone tubing, ID: 3/16”(4.8mm) OD: 1/4"(6.35mm) 20ft https://www.amazon.com/WOW-Design-Professional-Ac...
1 3way 2position Solenoid Power off : Port 2-3 pass , 1 is blocked ; Power on : Port 1-2 pass, 3 is blocked. ID: 2mm, OD: 4mm 48 x 20 x 21mm 12V, .19A https://www.amazon.com/uxcell-Miniature-Solenoid-...
BOM 4: Lighting
2 Grow LED strip of 4R:1B LEDs, SMD 5050, IP65 16.5ft 12V 2A https://www.amazon.com/AveyLum-Waterproof-Flexibl...
2 White LED strip of white LEDS 16.4 ft 12V 2A https://www.amazon.com/dp/B076RQR47S/ref=sspa_dk_...
BOM 5: Electrical
1 Raspberry Pi 4 3.33V 8.5x5.65x1.1 cm 5.1V / 3.0A DC https://www.raspberrypi.org/products/
1 Raspberry microSD 64GB microSD card https://www.amazon.com/Samsung-Endurance-64GB-Mic...
2 ENV Sensor temperature, humidity, barometric pressure, and VOC gas 1.8x1.65x.28cm 3.3 or 5V https://www.adafruit.com/product/3660
2 Camera 5megapixels, autofocus 15 Pin Ribbon Cable https://www.amazon.com/Arducam-Autofocus-Raspberr...
2 Relay 8 Channels 14x5.7x1.7cm 5Vpower, 3.3V trigger https://www.amazon.com/MCIGICM-Channel-DC-Relay-M...
2 28V to 12V, 5A Step-Down Converter 9.5-36V to 12V, 5A 6.78x11.2x3.8cm https://www.automationdirect.com/adc/shopping/cat...
1 28V to 5.1V, 8A Step-Down Converter 9.5-36V to 5.1V, 8A 6.38x11.2x2.56cm https://www.automationdirect.com/adc/shopping/cat...
1 Wiring 10 colored 22AWG wire kit https://www.adafruit.com/product/3175?gclid=EAIaI...
BOM 6: Zeroponics
1 Vents, Microporous PTFE, 100cc/in2/sec, 24x2in roll https://www.films.saint-gobain.com/products/chemf...
1 Vacuum Pump Outlet Diameter: 3.95mm, .75L/min, requires 5V, 1A power https://www.amazon.com/5V-12V-Aluminum-Diaphragm-...
Step 1: Structures and Frame
The structure is a perfect 50x50cm square that is broken up into top-bottom: 1cm top plate, 18cm top biome, 12cm middle body, 18cm bottom biome, 1cm bottom plate. Our retractable roof design optimizes the efficient use of space without compromising the environment for the plants. Four 20cm telescopic poles connect the top and bottom plates, two with springs to expand the structure into a 50cm cube and two hollow for running wiring. The roof is adjustable by spooling a wire running through the spring arm and connected to the middle frame by use of a bidirectional servo, unwinding the wire to raise the roof away from the plants and winding the wire to pull the roof closer to the body. This allows us to entirely collapse the habitat to less than ⅓ of its full size for storage and transportation and expanding to max plant height over the growth of the plants.
Surrounding the biome is a 360-degree retractable shield. The inner part of the shield is made from a clear PEVA plastic and is layered with an outer shield of mylar to reflect light. The shield maintains a closed internal environment while reflecting light back into the biomes. The biome shield is fully retractable to the roof to allow for easy plant care and harvesting. Circular grommets used to thread a retractable cord to keep the shield straight and assist with folding. Strong magnets are placed in the base of the shield to create a good seal with the middle frame.
The middle body houses all the central components, such as the electronics and water delivery system. The middle frame is made out of T-slot aluminum bars and ⅛” acrylic body panels. The middle structure houses the power, air, data, and water ports, rack mounting points, electronics, and the water reservoir in the middle with plant pillows on both sides. There are two acrylic plates in the middle body where the plant pillows are secured to and between the acrylic sheets is the water reservoir.
Roof Build Instructions:
- Load 24 x 24in 1/4in aluminum plate into CNC mill.
- Upload and run the file to cut the aluminum plate into the desired 50 x 50cm square and to predrill holes for the arms, fan, and motor mounts.
- Cut two sheets of PEVA and two sheets of Mylar 18 x 200cm.
- Lay PEVA on top of Mylar and sew in O ring string holders starting at the bottom and one every cm until the top, repeat every 10cm. Sew magnets into the bottom every 10cm. Sew two ends of the curtain together to create a 360-degree shield that is 18cm tall. Repeat for bottom biome shield.
- Take four of the eight spring telescoping arms, unscrew the bottom and remove springs. These will be used to run wiring.
- Take the other four spring telescoping arms and thread nylon wire down through the spring. Secure the nylon wire to the base end by tying it around the base and then gluing it to secure it’s position. These will be for raising and lowering the roof.
- Attach the four arms to the roof 3cm from the corners by bolts. Repeat for the bottom.
- Attach wire from the two sprung arms to the spool. Repeat for the bottom.
- Attach spool to the servo motor and bolt servo to the roof. Repeat for the bottom.
- Run motor power and control wires down the unsprung telescoping arm.
- Attach retractable kevlar wire to roof matching the spacing of the O ring string holder, every 10cm.
- Attach sensors with adhesive as depicted in the roof schematic and run wires down other unsprung telescoping arm.
- Place the shield around the four arms. Retract shield into the folded pattern by winding the spool and string kevlar string through the O ring holders. Tie off and glue the string to the bottom O ring holder.
- When it comes time to connect the roofs to the middle frame, bolt the four arms to the cross-layered acrylic sheets that are supporting the plant pillows.
Middle Frame Build Instructions:
- Cut four 1.5x1.5cm T-slot rods to 50cm, four to 47cm, and four to 9cm.
- Laser-cut four 9.5 by 47.5cm rectangles of acrylic.
- Laser-cut one acrylic rectangle with ISS rack ports and a second acrylic sheet with front-facing ports.
- Connect two 50 (outer square) and two 47cm (inner square) to create a 50x50cm square. Repeat for bottom.
- Connect the bottom square to the four 9cm rods at every corner.
- Slide the two acrylic sheets with ports opposite one another and the two solid acrylic sheets on opposite sides of the cube.
- Connect the top square to the four 9cm rods at every corner, sandwiching the acrylic sheets in place.
- Laser-cut two acrylic sheets each into a 40x40cm square with four arms that connect into the middle frame.
Step 2: Air Circulation
It is essential for plants to have carbon-rich air to feed off of, and it is crucial to have continuous air movement in space, so oxygen bubbles do not inhibit the plants ability to perform photosynthesis. The top and bottom biomes share the same air but can be made to have separate biomes if needed by using 47x47cm acrylic sheets in the middle frame instead of 40x40cm sheets. For input and output air, we have one solenoid in the middle connected to the AAA Air inlet and a second solenoid on the other end of the backplate connected to the AAA Air outlet. At the top of each biome, two blower fans pull air in and blow them to the sides for circulation.
Air System Build Instructions:
- Bolt blower fans to the roof by use of the pre-drilled holes and run wires down unsprung telescoping arm that already has a motor wire. Repeat for the bottom.
- Place the solenoid inlet and exhaust ports that were pre-cut out from the acrylic backport sheet.
- *For separated biomes, use a 3-way solenoid instead of 2-way for dual zone-control.
Step 3: Watering
The water reservoir’s size is very important. We wanted to go with the largest reservoir size possible to limit the number of times the astronauts would have to water the garden. The reservoir is made of lightweight mylar to create a 15L, 44x44x8cm reservoir. The watering system is made up of a centralized reservoir, a peristaltic pump, and solenoid valves to allow two different watering schedules. It is also possible to enable individual plant watering schedules by using a solenoid connected to every plant.
Watering System Build Instructions
- Cut two sheets of mylar 60 x 60cm.
- Cut two 3/16” silicone tubing 6cm long.
- Lay the first mylar sheet down, then place two 3/16” tubing on the mylar with 2cm hanging off.
- Place the second mylar sheet directly on top of the first.
- Go over the outer 4cm with an iron set to high to create a seal. Trim off 2cm of excess mylar around the bag.
- Attach an external water port connector to one of the two tubes sticking out the mylar bag. Connect the second tube to the peristaltic pump.
- Connect the peristaltic pump to port 2 of the 3-way 2-position solenoid using 1/4in tubing.
- Create two sets of 6 port connectors using 5 Y-Connectors.
- Attach a 6 port connector to solenoid ports 1 and 3.
- Cut twelve 20cm 1/4in tubing.
- Connect one tube to each port of the 6 port connector. On the other end of the tube, attach the plant pillow’s reciprocal connector.
- Mount one acrylic sheet 2cm from the bottom of the middle frame, insert water reservoir, and mound second acrylic sheet 2cm from the top of the middle frame to sandwich the reservoir bag and provide a flat surface to mound the plant pillows onto.
Step 4: Lighting
The right lighting conditions are vital for optimal plant growth. With plants responding better to particular wavelengths, we are using a 1 blue to 4 red (1B:4R) 5050 SMD LED rope light for the majority of our lighting. We are also using warm white 5050 SMD LED rope lights. The white light illuminates the plants, so we see the plants in the color we are used to seeing for better observation. The LED rope lights are IP65 rated.
Lighting System Build Instructions:
- Cut eight 40cm long 4R:1B LED rope strips, cutting along the dotted mark.
- Cut two 40cm long White LED rope strips, cutting along the dotted mark.
- Cut two 15cm long White LED rope strips, cutting along the dotted mark.
- Attach the LED rope lights with adhesive, as depicted in the Roof Schematic.
- Repeat for the bottom growth chamber roof.
Lighting System Wiring Instructions:
- Alternating every other strip of 4R:1B LED rope strips, wire in parallel. This will result in two groups of 4R:1B LED strips.
- Wire all White LED rope strips in parallel. Using Yellow wire for 12V positive and Black wire for ground. Run wire down unsprung telescoping arm that already has sensors wire.
- Connect each of the three sets of lights positive wire to the Normally Open port of a relay switch, following electrical schematic shown in the Electrical Schematic.
- Repeat for the bottom growth chamber roof.
Step 5: Electrical
To ensure optimal yields and minimize the gardening time for the astronauts, the system needs to be able to adapt and manage itself. Co2, humidity, temperature, and pressure sensors are used to control the air input pump rate, the biome fan speeds, the number of lights on, and the air exhaust valve. The sensors, peristaltic pump, solenoid valves, and piezoelectric motor are all controlled by a raspberry pi. By using a peristaltic pump to water the plants, the computer tracks how much water has been used by knowing the pump flow speed and how long it is on and sends an alert when refills are needed. There is a wide-angle camera on the roof to record plant growth, allow ground scientists to take a look whenever they want, and for the potential use by AI to monitor the plants' growth and tweak the grow environment as necessary. The LEDs, fans, pumps, and solenoids all run off of 12V, which is supplied through a step-down converter, and the sensors, stepper motors, and Raspberry Pi run off of 5.1V, which is stepped down from 28V.
Electrical Wiring Instructions
- Select 20A fuse for ISS express rack SSPCM connect.
- In parallel wire two 28-12V 5A step-down converters and one 28-5.1V 8A step-down convert to the SSPCM port, using purple wire. And wire to ground with black wire.
- From 5.1V, connect in parallel the Raspberry PI, two 8 channel relays boards, and five stepper motors, using red wire. And wire to ground with black wire.
- From 12V, connect in parallel all 8 relay channel com ports: one white LED rope, two 1B:4R LED rope, two blower fan, and three solenoids to normally open, using yellow wire. And wire to ground with black wire.
- From the second 12V, connect in parallel 7 relay channel com ports: one white LED rope, two 1B:4R LED rope, two blower fan, and two solenoids to normally open using yellow wire. Also wire peristaltic and motor driver in parallel, using yellow wire. And wire to ground with black wire.
- Connect the 8th relay channel com port to 5.1V and then to the vacuum pump, using red wire. And wire to ground with black wire.
- Wire two motors from the two slot motor driver chip in: 12V power with yellow wire, signal with white wire, and ground with black wire.
- Use Raspberry Pi 3.3V to power the sensors using orange wire. And wire to ground with black wire.
- Connect the Raspberry Pi to the camera with a 15 pin ribbon cable. Repeat for the second camera.
- From the Raspberry Pi, connect 8 signal wires to each of the two relay boards, 5 signal wires to each of the five servo motors, 4 signal wires to each of the two sensor chips, 1 signal wire to the peristaltic pump, and 1 signal wire to the motor driver, using white wire.
- Boot up Raspberry Pi with the correct code.
Step 6: Growing Beyond the Plant Pillow - Zeroponics
With our second design, we were able to forgo the plant pillows for our zeroponics root reservoir, an ultra-lightweight hybrid mylar bag with insertable 3D printed root guides that screw on seed caps. Air is passivated through the zeroponics root reservoir through a while letting air pass through, effectively aerating the roots. Using semipermeable membrane “vents,” that act like gills to diffuse air out of the zeroponics root reservoir into the biomes, overcoming the challenges to traditional methods of hydroponics in space. The vent is a flexible PTFE membrane that is waterproof and repellent while allowing air to pass. The root guides have two pathways to deliver air and water & nutrients directly to the plant's roots.The air pathway has many micro holes for air and the other pathway has many tiny holes for water and nutrient mixture. The root guide is made of semi-absorbent structural material, creating a lattice between the air and water/nutrient stems to assist with watering or oxygen delivery. The system can fill the root bag with water and nutrients with the root guides delivering a constant flow of oxygen to the roots that will be expelled through the vents into the biome; like a deep water hydroponics system. Or the bag can be pumped full of air and the root guides deliver water and nutrients directly to the roots; like drip hydroponics.
Our overall design was created with modularity in mind. The only difference between the plant pillow system and ours using zeroponics is that the zeroponic roo reservoir replaces of the plant pillows, along with a nutrient dosing system and a vacuum pump for emptying the root reservoir at the end of a grow. The nutrient dosing system uses five syringe pumps, and the nutrients solutions can quickly be swapped based on what plant is being grown. Like the plant pillow design, we use a 3-way solenoid to provide individual watering schedules to the top and bottom biome plants
Zeroponics Root Reservoir Build Instructions (40x40x2cm)
- Cut two sheets of mylar 42x42cm and one sheet 46x46cm.
- With the two 42x42cm sheets, cut nine 4cm diameter circles in three rows of three. Also, cut 3cm wide strips 35cm long 2cm along the border.
- With one 42x42cm sheet, place the root screw ports with a 4cm diameter flat base on top of each 3cm diameter holes and place 4cm by 36cm porous PTFE film on top of 3cm by 35 cm vent holes.
- Cut eighteen 20cm tubing.
- Create two 9 port connectors using 8 Y-connects. Connect the single stem to the water solenoid and the other single stem to the air solenoid.
- Connect two tubes to each root screw ports to connect the root guide to air and water and nutrient mixture.
- Place the second sheet with cutouts directly on top of the first shit, sandwiching the root guide and cap screw ports, tubing, and porous film between mylar.
- Go around all edges with a heated iron to seal the two mylar sheets together.
- Align 42x42cm and 46x46cm edges together and use the heated iron to go 1cm around the mylar sheets.
- Trim off excess mylar.
- Repeat for the bottom root reservoir
Nutrient Dosing System
- Syringe Pump: https://www.instructables.com/id/3D-Printed-Syrin...
- Using four Y connects, combine syringes to a single tube.
- Using one Y, combine the nutrient tubing to the water tubing. Then connect to the water solenoid.
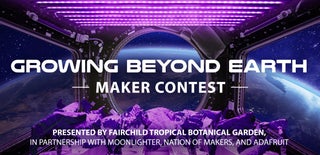
Participated in the
Growing Beyond Earth Maker Contest