Introduction: Timber Guitar Stand
We moved house a year and a half ago and, due to a lack of closets or storage, our solution for the guitars was to leave them piled up in their cases beside the couch. Aside from being an epic eyesore in the lounge room, it also meant it was a big hassle every time we wanted to pluck some tunes.
Buying a modular couch that took out the "guitar corner" spurred me into planning action and I began researching guitar stands. At our last place we had made a guitar hanger that was screwed into the wall. Sadly our rental agents are not massive fans of putting lots of screws in walls and so we had to look at getting a free-standing one.
Multi stands are pretty cheap to buy and we could have just bought one, but the cheaper guitar stands for sale are pretty boring and ugly...and who wants to do things the easy way anyway?
Hoping to utilise some of the beautiful timbers we had lying around I went hunting on pinterest and instructables for a design I liked and loosely based mine on a few really excellent instructables I found here -
https://www.instructables.com/id/Multiple-Guitar-St... and here -
https://www.instructables.com/id/My-Multiple-Guitar...
Check them out!
Step 1: Plan the Design
I always find it easier to make something if I have a pretty clear plan in my head and it helps to have all the measurements marked out so I have a guide for how to cut the timbers.
I drew this one in sketch up and it gave me the spring board I needed. Sorry, I'm an Aussie, so all my measurements are metric. There's always google converter for the imperial makers out there :)
The dimensions are based on my research into other guitar stands - how deep and high it needed to be and working out roughly how to get the right width for how many guitars I have - not nearly as many as everyone else apparently because most multi stands are made to fit about 8 guitars. Clearly I have some shopping to do!
Step 2: What You Will Need.
You will need the following timber lengths.
2x4 @ 2m For the feet and bridge
70mm/25mm @ 2m For uprights
Screws and finish
50mm stainless decking screws x 10
2x stainless batton screws @ 120mm long
Decking oil or finish of your choice
Tools
Table saw or powersaw
Scrollsaw , jig saw or coping saw
Sander or sandpaper- 240grit
Drill and drill bits - Decking drill and countersink in one and 5mm long series bit.
Step 3: Rough Cut 2x4
I chose some 2x4 hardwood I had for the base feet and cut them both to 500mm. The drop saw is the love of my life when making things, so you'll see it a lot, however any cutting tool will do - it doesn't have to be perfect.
Step 4: Dressing Timber Feet
The 2x4 I was using was very ripply and needed a good sanding. Because I am lazy and hate sanding, I chose to use a planer to flatten and neaten all the edges. If you are less lazy than me and feel like investing lots of time into sanding, that works well too.
Step 5: Cutting Feet to Length
I cut my feet to 500mm long. Check the ends are square and neaten them before cutting you timber to length.
Step 6: Cutting Uprights
The piece of timber I used for the uprights was too thick, so I halved it using my table saw - a small block of wood cut at the right width can be a very useful guide to set your distance between the blade and saw guide.
Wanting to have angled upright pieces meant that I needed to work out the height I needed and then cut them slightly longer to allow for the angle. I cut my pieces flat at 800mm and later docked them to the same angle as the base.
Step 7: Dressing Uprights
Dressing is a breeze when you have a planer! Dress the side that has been cut with your table saw till its smooth.
Step 8: Working Out Upright Positions
To work out the positioning of the upright pieces and the angle I wanted to cut, I laid out my two feet pieces to use as a square and used one upright piece to indicate where the timber would hit the wall, adjusting the other upright piece until I had the angle and height I wanted.
Step 9: Marking and Cutting Uprights
I marked out my cut and the upright placement on the timber and then worked out the angle using the drop saw guide - it was 22.5º. I cut the top and bottom at this angle on both upright pieces.
Step 10: Cutting Bridge Piece
I used another piece of 2x4 to be my bridging neck piece and cut it to 680mm I had worked out that allowing approx 150mm per guitar was a good guide and then adding on the 40mm either side to allow for the feet width gave me the length I needed.
Step 11: Marking the Bridge
I wanted to make the top part of my guitar stand a little ornate because the rest of it was quite square and boxy. I divided the full bridge length into four and made a mark at each point. Do this by eye roughly first before doing it by measurement as the eye makes much nicer curves than precision can.
Step 12: Hula Hooping While Marking
Because it's important to have fun while making stuff!!
Also, the hula hoop gave me just the right amount of curve to stencil my cutting lines on.
Step 13: Scroll Sawing
The 2x4 I chose was hardwood which meant that cutting any detail would be tricky, I used my trusty scroll saw to follow the lines as accurately as possible. For softer timbers, a coping saw or jigsaw would work fine. Be prepared to spend a very, very long time doing this if you use a scroll saw on hardwood.
Step 14: Sanding Scroll Saw Marks Out
I used a belt sander to sand out all the little teeth marks that the scroll saw put into the curves. You can always sand by hand with sandpaper rolled around a broomstick.
Step 15: Using a Router to Bullnose Edges
Getting nice clean edges on the timber gives it a more polished look so I used a router to neaten everything up. Place the lead of the router over your shoulder so that it is not in your way.
Step 16: Screwing in Uprights
To ensure the stand was really stable, I used three stainless steel screws on either side, running down on an angle to avoid the timber splitting.
Step 17: Transfering Upright Marks to Other Foot
Mark out where the screws need to go in the other upright piece and the base and then check them against the first base and upright you screwed together to make sure they're the same.
Step 18: Holes to Connect Bridge
Work out where the centre of the bridge piece will sit against the upright pieces and, using a clamp, drill a hole through both upright pieces at the same time, ensuring they are at exactly the same height.
Step 19: Staining
It's always important to treat your timber with something that will help give it longer wear. You can paint it, colour stain it, or oil stain it like I did with a good quality decking oil. I chose to use decking oil because the timbers I used were beautiful and I only wanted to bring out their natural colours, not change them.
Step 20: Admire
Now that you can see how the final product will look, take a moment to pat yourself on the back for getting this far and plan your next moves.
Step 21: Positioning Your Guitars
My awesome husband made me a lap-steel guitar for my 21st birthday. It's absolutely gorgeous and I wanted to have it on display with our standard acoustics. Because it's a lot narrower at the base than the other guitars, I positioned the horizontal rods closer together so that it would not fall through.
To ensure the rods are spaced in the positions you need them for your guitars, I recommend placing them on top of your base feet and rolling them forward and back until you find the distance that works best for what you have and then marking the timber at the centre of each rod.
Step 22: Accuratley Marking Base Bars
I used a ruled marking tool to get the exact points I needed to drill my holes and then held the two base pieces against each other to ensure the points matched on both sides.
Step 23: Drilling Holes for Base Bars
So that the point of the hole cutting drill bit went just through the base (making a mark on the other side to make it easier to put a screw in the right spot) I held it against the base and marked directly onto the bit.
Step 24: Drilling
These holes needed to be really, really accurate, so make sure your drill is super straight when doing these.
Step 25: Cutting Your Rods and Jflex Protectors
The rods are kwila dowel - kwila is a very strong hardwood and it meant that the base wouldn't bow down the track. The holes I had drilled in the base feet measured 25mm in depth and so I just added that on to the width of the stand and cut them to length.
For the foam bedding over the rods, I bought some jflex from my local Bunnings (it's used to cover pipes that need to be insulated usually). I cut it 10mm too long to ensure a snug fit and not leave any exposed timber either side.
Step 26: Fitting and Fixing Base Bars
Put the rods in one side of the base first, slide on the foam and then stick the rods in the other side. Because the drill bit left a mark on the outside of the base pieces, I knew exactly where to drill and put stainless steel screws in to hold the rods.
Step 27: Marking Bridge for Guitar Neck Holders
This bit was tricky and there are a few ways to do it. I measured out the bridge and marked at even intervals (66.6mm) and left an extra 40mm on each end to allow for the base feet. Honestly I'm not that happy with how this worked because some of my guitar necks are too fat for that amount of space. You could also do it by eye measuring around each guitar or not leaving the extra space at either end. It's best to use the guitars you are using to get the best measurements here.
Step 28: Drilling Peg Holes and Sanding Pegs
Make sure your drill is really straight and the holes are as exact as possible so you don't end up with pegs facing different directs and looking higgledy-piggeldy. If you have a drill press use it here.
Step 29: Achiving a Smooth Finish on End of Jflex
Cutting the jflex neatly is harder than it looks, even with a super sharp knife, so once the foam pieces were cut, I used a blow torch to heat up the end of a can and gently pressed the foam ends onto them, getting a flatter, cleaner look.
Step 30: All Done!
Now you throw your guitars in and see how it all looks together. I found the lap-steel fitted better without the foam so had to take those pieces off, but otherwise it works really well.
Enjoy your new stand!!
Special thanks to my husband for taking pics of me when my hands were busy and letting me raid your timber stash. You are awesome!!!
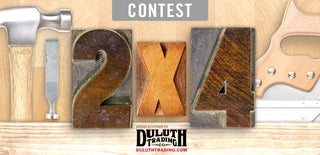
Participated in the
2x4 Contest
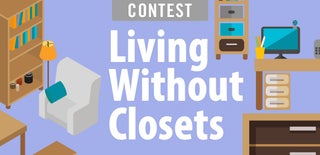
Participated in the
Living Without Closets Contest
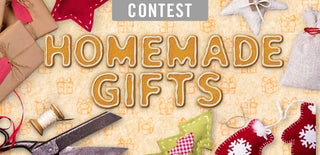
Participated in the
Homemade Gifts Contest 2015