Introduction: Timber Jewelry - Necklace Pendants, Cufflinks, Ear Rings
As a 23 year old guy, why do I make jewelry. It started making some cufflinks for some mates of mine as birthday presents. I realised that they were a great use of exotic off cuts. Then I started doing markets, cufflinks sold well but I wanted more diversity on my table. I started making the pendants and then the earrings. All use my best bits of scrap as I hate wasting it.
This will cover the 3 main designs that I do.
Step 1: Necklace Pendant Part 1
Cut the blank to size, approx 50mm x 50mm x 8mm and then cut the corners off it. These also are made from quality off cuts The block that I use in the chuck has a tenon that is 30mm in end grain. This is important for a step later. Using hot glue I attach the blank to the block. Using the gouge, I rough shape the outside of the dome. So there is no break out, I come back from the other direction for the last 2mm (pic 8). Then I can refine the shape. When done, sand, including rounding over the back edge.
Finish using Aussie Oil. This is a friction polish that is applied using a rag. The heat of burnishing with the lathe on is what sets it off. Pry it off with a chisel. It should be easily leveraged. Before the polishing process, I plug in the hot glue gun for the next step
Step 2: Necklace Pendant Part
The next step is remounting it off center with hot glue. I line the edge up with the edge of the 30mm tenon on the block. I find this is a good balance for these pendants, with the hole 15mm from the edge. Start by making the hole in the middle. Make it bigger with a flowing curve. You dont want it to be a straight line. It will be cutting air at some points as the timber will not always be in contact. Sand it carefully as it is still uneven. Then if you want, you can put some grooves in the free space. I did them at varying depths. These are best to sand when the lathe is not on. Re polish the surface using the Aussie Oil. Pry off with the chisel and sand the back. Round over the edge from the back side of the hole.
Step 3: Necklace Pendant Different Design
This is another design where I put a bead around the edge of the pendant. I made the center hole go just up to the edge of the bead. There are so many different options for designs. You can use eyelets to for chains rather than leather bands.
Step 4: Necklace Pendant, the Band
This is a simple sliding knot that I was taught at the jewelry shop where I get get some supplies. Its done with 2 overhand knots. Loop the leather and tie an overhand knot around the other end. Slide that further down and then do the same at the other end. Make sure the knot is not too tight and it should be able to slide well. This loop can then be threaded though the hole in the pendant and then through the rest of the loop on the other side.
Step 5: Cufflinks
I buy the kits in bulk so I have made quite a few of these. Over 120 pairs. I start with small bits of timber roughly 20mm x 20mm x 5mm. I sand the bottom flat and then knock the corners off. Like the pendants I have a block that I use to hot glue onto. The diameter is fractionally smaller than the inserts of timber. I use my beading tool to size the diameter. Pic 6 shows it close but still too tight. It needs to be done with in 1/4 of a mm. If it is more, it has a gap and looks loose.
Then the top has to be faced off. With figure like this blackwood, it does make it harder. It had to be done with a sharp gouge. Same with other soft woods. Hard woods I sometimes scrape the surface. These also have to be an exact height (4 - 4.5mm). If they vary, it is easily noticed. Sand and take the sharp edge off with out over doing it. If its too rounded it goes into the sleeve of the cufflink.
For these, I use triple E wax and glow. I choose these for the ease and speed of application. I dont use it on bigger pieces as it can get streaky. Use a small amount of wax on a rag, rub it in and then turn the lathe on and force it in. It has an abrasive in it and will also sand it. Then repeat the same process with the glow. For efficiency, I put the hot glue gun in before polishing so its ready for the next one.
Use a chisel to pry it off and then glue in using superglue. Make sure its not too much as the timber fills most of the space and the glue could push out.
These are great gifts and more people wear them than you would think.
Step 6: Acorn Ear Rings
These are my better sellers. I choose to always make these from oak as that is they tree they come from. With timber selection, dont use wood that are too hard. They might snap of the eyelets
Start with the blank in the pin jaws. They are the most secure way to hold timber like this. Rough it down with a gouge. The tool I use is a spindle gouge blank that hasnt been ground to shape. I use it for roughing for small pieces. These are 15mm diameter and 18mm long. I mark my measurements and then do the rest by eye. I could use calipers for more accuracy. Using the point of the skew I make a clean cut for the shoulder and then size the other diameter at approximately 13mm. I use a gouge to shape the end, rolling the tool over and then rolling back out to an open position to get the nib at the end.
I use a parting tool to mark the end, turning down to about 5mm for support. Like rolling a bead, I shape the top with a skew. Can also be done with a gouge but the skew should give a cleaner cut. Then I sand and finish it all using the Aussie Oil. Then you can turn the tenon down to 1-2mm and shape the top. Part that off and clean it up on the sander.
With any turning, making one is easy, multiples are more challenging. These are good to make 3 and use the 2 most similar ones as the ear rings and the other as a necklace pendant.
With a 1mm bit, drill a hole in the top and screw the eyelet with pliers. Use jewelers ones or cheap ones that are flat on the inside, not ridged. I have the cheap ones. Bend out the eyelet and but the ear hook on, then bend it back to shape.
These shapes are only limited by your imagination.
Step 7: Enjoy
These are perfect gifts or great for the table at markets. All quick projects and easy to make with minimal timber needed. I love the variety that I can get from such little projects. Enjoy making them
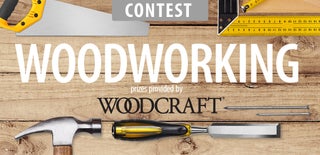
Participated in the
Woodworking Contest 2017
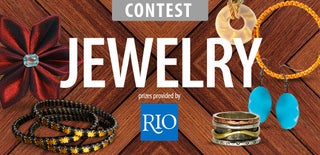
Participated in the
Jewelry Contest 2017