Introduction: Tools -- 3 for the Price of 1
It's raining, can't do anything outside so thought I would have a go at making some woodwork tools.
All of my stuff is mainly made from scrap, quite often from inorganic waste (roadside dumps), I like to recycle and people seem to dump a lot of old solid wood furniture.
Supplies
Tools :-
Pillar Drill
Bandsaw
Holesaws
Tablesaw/Chopsaw
Drillbits
Epoxy Glue
Bench Sander
Grinder
Materials for the Marking Gauge :-
Small Hardwood Block (mine was 70x45x45mm)
Dowel (I used 10mm)
40mm Hex Head Roofing Screw
8mm Bolt 50mm long
Butterfly nut
Materials for the Sanding Block :-
6 inch piece of 4x2
6 inch piece of 4x 1/2inch
8mm Carriage Bolt 50mm long
8mm Tee Nut
Small piece of 4x2 for handle
Materials for Drill Sanding Attachment :-
8mm carriage Bolt 150mm long
8mm Butterfly nut
8mm plain nut
Metal strip (I used a piece of Meccano)
Small Screws
Step 1: Tool 1 - the Marking Gauge
I cut a piece of wood from a scrap table leg, not sure what the wood is, either Kwila or Redwood.
The dimensions are 70mm x 45mm x 45mm.
Step 2: Drill a Hole
I drilled a 10mm hole in the centre of the piece to allow the dowel to pass through.
Step 3: Clamping Bolt Hole
I then drilled another hole towards one end of the piece, this was 8mm to suit the clamping bolt. I also drilled a 15mm recess for the bolt head.
Step 4: Clamp Slot
Using the Bandsaw, I cut a slot from one end to the dowel hole. I then inserted the dowel and the bolt and tightened with a butterfly nut to ensure that the dowel was clamped firmly when the nut was tightened.
Once I was satisfied with it I epoxy glued the nut head in position and allowed it to dry.
Step 5: The Marking Point
I screwed in a roofing screw into a small piece of dowel and mounted in my pillar drill. I then used a file to sharpen the "washer" of the screw.
Step 6: Screw Mounted in the Dowel
I then drilled the dowel and mounted the sharpened screw into it. I also marked the dowel at 10mm intervals as a guide.
Step 7: Using It
Then I checked it all worked
Step 8: Tool 2 - Sanding Block
I cut a piece of 4x2 and 4x1/2 to the same size.
The 4x2 is a piece of framing timber (softwood) and the 4x1/2 is hardwood (Rimu from a broken drawer)
I then sanded both and drilled an 8mm hole through the centre of both.
Step 9: Counterdrill for Bolt
I counter drilled the base of the 4x2 for the carriage drill bolt head.
Step 10: Handle
Using 2 different size hole saws I drilled halfway through a piece of scrap 4x2 with the larger, then from the other side with the smaller to give a stepped handle
Step 11: Tee Nut
I pressed a Tee Nut into the handle hole.
Step 12: Sanding
I put a bolt through the centre and mounted the handle in the drill for sanding.
Step 13: Assembly and Use
I assembled and epoxy glued the 50mm carriage bolt in the bottom recess. Once dry I cut a sheet of sandpaper and put it in. Tightening the handle secures the paper in place.
Step 14: Tool 3 - Sanding Disc/Column
I haven't got space for a spindle sander, so have made an adaption for my pillar drill.
First I cut some circled from scrap 4x2
Step 15: Sanding
I then mounted 2 of the circles on a 150mm carriage bolt using an 8mm nut at each end, cut the head off of the bolt using a grinder and mounted them in the drill to sand the outside
Step 16: Slot
Using the table saw I cut a slot along the length of the circles
Step 17: Securing
I used a small piece of Meccano to secure the sandpaper in position and screws to hold it in place.
Step 18: In Use
Tested - It Works.
Step 19: All Together
And there they all are, about an hours messing around all together, and it's still raining!
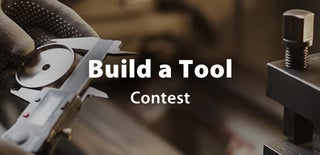
This is an entry in the
Build-A-Tool Contest