Introduction: Towers AstroGarden
Proposal: The Towers
This is a submission for the "Growing Beyond Earth" challenge in the professional category.
Design by Draper engineers: Carly Buchanan, Martin Sinclair, Isaac Whipple, Max Turnquist, Kevin Myers, Lexi Neese, Rob de Saint Phalle, and Jeff Burrell.
The Towers design uses up-lighting to coax the lettuce plants to grow at an angle to the walls, keeping the canopy far enough away from the light pole in the center to prevent tip burn. Staggering the location and planting times of the lettuce allows for a denser nesting of plants. The eight towers holding plants are attached to the four sides of the shell; the back face is reserved for electronics, water reservoirs, and the central light column; the front face is open to the ISS environment for water reclamation. The towers are plumbed in pairs which can be pulled out from the interior of the shell for easier access to lettuce for monitoring and harvest.
Root Volume & Growth Medium
The plant pillows in VEGGIE are 250 cubic centimeters in volume[1]; our tower modules have a volume of 245 cubic centimeters. We used sphagnum moss for the growth medium due to its natural capillary abilities, which helps draw water away from the source. We also experimented with a foam growth medium which may be less prone to mold or fungus, but isn't sold off-the-shelf in blocks that nest neatly into our triangular volumes and makes it harder to run the water plumbing. The modules could be filled with any growth medium, although granular growth mediums may need some sort of netting to keep them contained within the module.
Lighting
The type of lighting used and the distance from the light source to the lettuce have a major impact on the health of the plant and the shape that it grows in. To fit as many plants into the volume as possible, it was important to minimize that distance. We found commercial off-the-shelf hydroponic lighting units that claim they can be mounted as close as 4” from the canopy[2], so we chose to base our design around that number. However, professional hydroponic LED setups are carefully designed to create a consistent field of photosynthetic light across the growing area. We did not have the expertise or time to design a custom LED module, and COTS modules are designed for much larger growing areas than our small volume, so we used spools of flexible LED tape in our prototype. This means our prototype will not perform as well as it would with bespoke LEDs for our specifications. However, we do believe that the fundamental distances within the design are plausible. Since in space there is no gravity to tell plants which way is “up”, they grow straight toward the light. To try to encourage the lettuce plants to grow outward as well, we added up-lighting at the base of the plants. These LEDs will be dimmer than the traditional above-canopy lights since they are much closer to the leaves. We did find studies that had successfully used up-lighting for terrestrial growth operations to help plants receive more light and grow faster.[3],[4] To maximize lighting efficiency, we made the majority of flat surfaces inside the shells white to reflect light around the inside of the shell.
Growth Modeling
Staggering the growth stages of the plants allows for a more continuous harvest of lettuce and a more efficient use of space. The growth cycle of lettuce generally follows a Gompertz function[5], characterized by slow early growth, a mid-stage growth spurt and a final stage of slow growth until the lettuce is harvestable. The growth period is estimated to be 35 days (5 weeks) from a seed, with the fastest growth between days 10 and 20. For our modeling purposes, the lettuce plants were idealized as paraboloids opening upward, as we conjectured that lettuce growing in microgravity would be more voluminous at the top of the plant, closer to the lights. The maximum size assumed for mature lettuce plants is 10 cm in height and 15 cm in diameter at the widest point. Dry leaf masses were converted to paraboloid volumes to model the lettuce plants at different stages of growth. Based on this model, our design assumes two plantings staggered two weeks apart. When the first planting is harvested, this allows more space for the second planting to reach full volume at maturity, and then the second planting is harvested and the relationship is reversed.
Watering Method & Water Reclamation
We don’t have any experience in microgravity fluidics, so we did not design a new watering system. In our prototype, we use a garden soaker hose that weeps water to simulate the porous tube in the Advanced Plant Habitat (APH). We couldn’t find details of how PONDS works, since it contains Tupperware intellectual property, so we don’t know if the root modules could be reconfigured slightly to support a passive watering system. As there is no nutritional value in the growth material itself, fertilizer must be added to the water or the growth medium. We chose a liquid fertilizer in the water, but the design could support either method. As the International Space Station has a water reclamation system, our design takes advantage of it with one side of the shell open to the ISS environment to allow moisture transfer from the plants to the ISS's water reclamation system, similar to the method that VEGGIE uses. Fans are mounted throughout the shell for proper air circulation.
[1] Massa, G. D., Newsham, G., Hummerick, M. E., Morrow, R. C., & Wheeler, R. M. (2017). Plant Pillow Preparation for the Veggie Plant Growth System on the International Space Station. Gravitational and Space Research, 5(1), 24–34. Retrieved from https://pdfs.semanticscholar.org/c5a4/a623c0fe8de...
[2] Valoya BX and C Series. https://pdfs.semanticscholar.org/c5a4/a623c0fe8de... https://www.valoya.com/wp-content/uploads/2019/06...
[3] Zhang, Geng, et al. “Supplemental Upward Lighting from Underneath to Obtain Higher Marketable Lettuce (Lactuca Sativa) Leaf Fresh Weight by Retarding Senescence of Outer Leaves.” Frontiers in Plant Science, vol. 6, 2015, doi:10.3389/fpls.2015.01110.
[4] Takagaki, Michiko. “Chapter 27 - Challenges for the Next-Generation PFAL.” Plant Factory: an Indoor Vertical Farming System for Efficient Quality Food Production, by Toyoki Kozai and Genhua Niu, Academic Press, 2016, pp. 387–393.
[5] Barker, David J. et al. 2010. Analysis of Herbage Mass and Herbage Accumulation Rate Using Gompertz Equations. Agronomy Journal 102:849-857.
Supplies
- 1 box shell
- Threaded inserts and bolts
- 16 Slides
- 20 corner root modules
- 10 center left root modules
- 10 center right root modules
- LED strips
- 1.25” diameter pipe
- 1 pipe flange
- 4 fans with spacers
- 1 microcontroller
- 1 electronics breakout
- 1 power supply
- Wire & connectors
- 1 pump
- 1 reservoir
- ¼” ID soaker (porous hose)
- ¼” ID non-porous hose
- ¼” ID coiled hose
- 90-degree connectors for ¼” ID hose
- Cable holders
The CAD for this project can be found here.
Construction Notes
Since the purpose of this write-up is to specify the “form, fit, and function” of the major components, we do not include detailed construction methodology in this write-up. In our prototype, we sometimes used screws for ease, but we assume that all fasteners can be replaced with bolts paired with threaded inserts as captive nuts.
Step 1: Prepare the Shell
Steps
- Construct the shell walls. We routed the walls out of a plastic composite and 3D-printed the corner joints.
- Install threaded inserts into the walls.
- Assemble the shell.
- Install the slides.
- Cut the LED strips to length, install connectors, and attach LEDs to walls. We bought waterproof, flexible LED strips that had an adhesive backing.
- Mount the pipe in the flange, wrap the pipe with LEDs, and add connectors to the LEDs.
Notes
The shell is designed to fold and flat-pack. See the render for how constructing the shell with hinges would allow the shell to collapse. However, due to our limited machining capabilities and time, our prototype uses a rigid shell with plastic walls joined together by 3D-printed corners. To make assembly in orbit as easy as possible, we designed the shell so that some features are installed on the ground. This includes mounting the slides and the LEDs onto the walls.
Drawer slides are bulky for the tight space constraints. We used a custom-manufactured dovetail-shaped extrusion that slides within corresponding recesses in the back of the root modules. A T-shaped extrusion could also be used. It is important that the modules and the extrusion are low-friction so that they slide smoothly and easily.
Step 2: Install Life Support
Steps
- Attach the reservoir and pump to the back wall.
- Attach the ends of the coiled tubing to the wall
- Connect the ends of the coiled tube to the plumbing harness that connects to the pump.
- Mount electronics to back wall.
- Connect control board to power supply.
- Mount light pole with flange to back wall.
- Connect the LED strips to their corresponding connectors from the control board. Cable holders are useful for routing the wires neatly.
- Mount the fans to the wall, with spacers between them and the wall for air flow.
- Connect the fans to control board connectors.
- Connect the pump to control board connectors.
- Connect the input and output of the plumbing harness to the pump.
Notes
We designed the towers so that pairs of Towers could be pulled out of the shell for easier access to the lettuce plants for inspection, tending, and harvest. Coiled tubing at the base of each tower allows for each tower to extend out of the shell. The end of the hose that does not attach to the root modules should be held in place by a clip that attaches to the wall. Our design could be improved by adding a sled that the modules clip into to hold the tower together. Alternatively, the root modules could be designed to have snap latches or jigsaw joints to securely connect the modules together.
The power supply, microcontroller, electronics breakout, reservoir, and pump are attached to the shell by hook-and-loop tape so we could easily remove them for modification during prototyping. This ability could be a benefit on the ISS for maintenance, but a longer lifespan material should replace the hook-and-loop tape. The diagram above gives a general idea of how things are electrically connected. Essentially: using drivers such as Darlington arrays and/or MOSFETs to to allow the microcontroller to power the fans, pump, and lights on and off as determined by parameters that can be set by a user interface. The up-lighting and down-lighting should be wired separately so that the up-lighting can be run dimmer than the down-lighting since it is supplementary and closer to the leaves.
Our prototype does include a power supply. However, on the ISS power would be supplied by the Express Rack. The control electronics could also be packaged much more compactly onto a custom PCB. This would open more space for a larger reservoir. Our reservoir is currently large enough to hold ~4L of water, providing more than 1 day of water for 25 fully mature plants, which would require the reservoir to be refilled regularly. We constructed our reservoir using a boxed-beverage bladder contained within a rigid box. For a space-ready design, we propose a rigid-wall tank and a quick connect junction between the reservoir and the pump. This quick connect could be used to temporarily connect a water supply to refill the reservoir.
Step 3: Add Root Modules & Plumbing
Steps
- The center modules are stacked in towers of 5, alternating pointing left and right. These towers are placed in the shell so they are mirrored across the corner. See the diagrams above. The corner modules and center modules will be planted so their harvests are staggered by 2 weeks, ensuring that the lettuce plants have enough space and light to grow fully.
- The corner modules are also stacked in towers of 5. Two or three of the module slots will not be used for plants so that the plants can be staggered throughout the towers in a checkerboard fashion.
- Run porous tube through the root module towers, connect the ends of the tubes to 90-degree connectors.
- Stuff the root modules with growth medium.
- Slide the towers into place along their slides and connect the back-facing 90-degree connector to the free end of the coiled tubing.
- Add nonporous tubes connecting pairs of towers through the front-facing 90-degree connectors. This creates a single plumbing loop that runs up one tower and down its neighbor. See the plumbing diagram.
Notes
Currently our root modules mate flatly, face to face, to each other which does create a leak zone. In our prototype, we ran a bead of hot glue around the hole where the hose traveled between modules and pressed the modules together to create a water-tight seal. For a real version that would be launched into space, we recommend adding a flange around the hole or creating a rubber gasket that can be used to overlap the root modules and prevent leaks. Similarly, the lids of the root module would benefit from an O-ring or some other type of rubber gasket to help them mate securely to the root module body.
We used sphagnum moss as a growth medium because it was affordable, lightweight, acted as a capillary system to wick the water away from the porous tube source, and didn’t fall out of the hole where the lettuce sprouted. We also experimented with a foam growth medium, but it was difficult to carve into the shape of the interior of the root modules. The modules could be filled with any growth medium, although granular growth mediums may need some sort of netting to keep them contained within the module.
Step 4: Program, Prime, Plant
Steps
- Attach the user interface to the front edge of the shell, and connect its wires to the control electronics (again, cable holders are useful).
- Program the microcontroller to control the photoperiod of the lights and the frequency of watering.
- Prime the pump if it needs to be primed.
- Plant lettuce seeds into the growth medium.
- Monitor for seedlings!
Notes
A user interface module is intended to allow a user to interact with the control electronics to change the photoperiod, tune the LED wavelength, adjust the watering schedule and otherwise program the parameters that control the environment within. It is intended to mount onto the front face of the shell, but is currently mounted onto our control electronics on the back wall as we ran out of time to build a cable connection for it. Since the purpose of this contest was the geometry and layout of the design, we have not programmed the adjustable functionality into our prototype.
Step 5: Thanks & Acknowledgements
We’d like to thank Lauren Kessler, John West, Kim Slater, Seamus Tuohy, Chris Yu, John West, Kim Slater, and Bryan Dolan for their support of this project; Abigail Bonnice, Erik Weir, Steven Popkes, and Manwei Chan, and Allison Looney for their contributions; Bill Wells and Dave Reed for their advice; the rest of Draper Strategic Communication including Sarah Von Oldenburg and Allison Looney for their assistance; and Jay Schwartz for his carpentry skills.
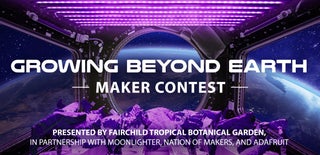
Runner Up in the
Growing Beyond Earth Maker Contest