Introduction: Tropical Epoxy Island Table
I had this really cool piece of wood sitting in my boiler room for years. I think it was bought 15 years ago as a stand or a base for something but was never used. It had dried up from sitting in the moisture-wicking environment of the basement, so I decided to breathe new life into it. Now it is a beautiful epoxy island table.
Let’s dive into it!
Supplies
- Materials
- Total Boat epoxy resin and hardener
- Spar Varnish
- 2x4 plank (enough to surround the wood island piece)
- Hairpin legs
- Alcohol ink
- Wood glue
- 2 inch Wood screws
- Wood hardener
- Cool shaped wood for the island center
Tools
- Clamps
- Paint brushes
- Drum sander
- Orbital sander
- Saw
- Spirit level
- Drill
- Drill bit the same diameter as shaft of wood screws
Step 1: Prepping the Island Wood
Since the wood had dried so much, I had to harden the wood. Otherwise, when the resin is applied, it would rip it apart; not to mention that sanding, cutting and other operation on the wood would destroy it because it was so brittle. Hardener is pretty easy to use; you just pour it on the wood and let it dry. Repeat this cycle until the wood becomes a little shiny on top and when you knock on it, it does not sound hollow.
The next step in the process was drum sanding and making sure the wood was as level as possible. I sent it through the drum sander enough times to make sure it was flat on top, which I measured with a spirit level. I used an orbital sander to make sure any small imperfections were ironed out.
Step 2: Building the Epoxy Enclosure
Since the epoxy is going to be poured all around the piece of wood, we need to make a box for the wood to fit in so that the epoxy hardens as a square around it. I found that melamine planks lined with Tyvek tape works the best for the enclosure because the Tyvek tape is easy to remove from the epoxy. In a pinch, packing tape would also work well. It adheres to the epoxy a bit more but is very easily sanded/peeled off. I used 4 melamine planks taped together with a base of chipboard into a rectangle that fit the island wood. I used Tyvek tape to try and seal all the edges so that epoxy did not leak through and ran a bead of hot glue on the outside of the box for good measure.
Step 3: Pouring the Resin
There are
two steps in the epoxy pouring process: mixing and pouring.
Mixing
- In the mixing stage, you mix 2 parts of resin and one part of hardener. You want these ratios to be close to exact, so I used a measuring cup. I also added about 5 drops of cerulean-colored alcohol ink to get that tropical blue color.
- You stir for three minutes. Make sure you hit that 3-minute minimum; you need the hardener and the resin to be homogenous.
- Note: I found that leaving the alcohol-ink colored resin outside in the sun did not retain its color very well. It is now a stormy gray color. Still cool, but not the tropical island table it once was.
Pouring
- The pouring part is a bit easier (you just pour an even surface). However, there are some nuances. With totalboat epoxy, you don’t want to pour more than 0.25 inches at a time.
- Your first pour should be about 1/8 of an inch, and let it cure fully (2 days). This helps seal any cracks and leak points in the bottom without leaking too much resin.
- You can pour the next layer in 2 circumstances:
- when the previous layer is in the gel state. This occurs after 40-ish minutes and the resin is a very viscous liquid. If you touched the pour with a toothpick, it would curl up, but eventually fall back down.
- when the resin has fully cured (2 days). Scuff up the previous surface first with light sandpaper and continue the pour
- Remove bubbles with a barbeque lighter and hovering the flame above the bubbles to pop them. Do not touch the flame to the resin.
- Pour until you reach just above the island
- Break off the melamine walls when the final layer has fully cured.
Step 4: Sanding and Sealing
If there are any burrs from the resin or Tyvek tape left stuck to the epoxy brick, you can sand it off with an orbital sander.
Sand the top of the table until the bare wood is just exposed. Make sure the tabletop is level to the ground after this process. Work up to 600+ grit sandpaper so that the surface of your epoxy table is smooth.
Apply a thin coat of spar varnish to the surface of the table as a protective coating.
Step 5: Building the Frame to Rest the Block On
This is where you can get a bit creative, but I made a simple table frame out of 2x4s and hairpin legs. I used a lap joint to connect the corners of the 2x4s with wood glue to hold it in place. I used wood screws to attach the hairpin legs to the frame. I also used wood screws to hold the pieces of lumber together diagonally. I have recently learned there is a tool called a kreg jig that can help you align these diagonal holes, but since I was ignorant of this at the time, I just used lots of clamps and scrap pieces to line up my drill and did it by hand. The resin block sits right in the wooden frame and can be flipped over. Voila! You have an awesome flippable resin table.
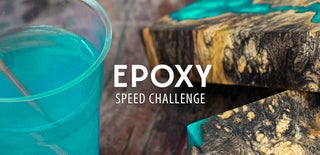
Second Prize in the
Epoxy Speed Challenge