Introduction: Turn an Old Equipment Chassis Into a Retro Cabinet!
Join me in converting a decommissioned gas monitor into a retro cabinet!
Retro computing and equipment chassis are absolutely gorgeous, so I decided to turn an MDA System 16 Toxic Gas Monitor case into a gorgeous cabinet, featuring five shelves, dimmable LED lighting, a power strip, and central power control.
This project can be easily adapted to any chassis you can get your hands on!
Reuse and recycling is not only very important to the wellbeing of the environment, it's also a fun hobby and a great skill to have! Being able to turn other folks' trash into your treasure is great to do, so I made it my goal to make as much of this project out of things I could find in the trash, recycling, or e-waste. In the end, only two parts were purchased instead of found!
Here's how I did it, and how you can do it too.
Supplies
Many of the materials necessary can be gathered for free, or very cheaply, with a bit of patience and networking. I managed to get all but two things for my project from recycling, but it took several weeks of looking to gather them all.
Materials:
- First and foremost, you'll need a cabinet to restore/convert. Large decommissioned equipment can certainly be hard to find, but scrap yards, large antique stores, local colleges, and e-waste recyclers are a good place to start looking. I was lucky enough to pick up this MDA Scientific System 16 Toxic Gas Monitor Cabinet from my university- it had recently been retired from a soon-to-be-renovated lab, and was destined for the scrap yard if I hadn't grabbed it
- Wood for shelving- This can also be found in the recycling! Recycling centers, scrap construction lumber, or free furniture from online marketplaces can be a great source of wood for this project. The wood I used was plywood from shelves that had been thrown out.
- LEDs and drivers- I got my LEDs and LED driver from a light fixture I found in the recycling, but cheap LED strips, Neopixels, or LEDs pulled from old lightbulbs will work just as well, depending on your prior experience with electronics.
- Switches- I got my switches from e-waste equipment, to add to the retro look, but a light switch will work just fine-- just be sure that it's properly rated for any power you expect to put through it!
- Wire- Long scrap wire can certainly be harder to find. If you know any electricians, you may be able to get longer pieces of leftover wire from them, but yard sales and scrap yards are a good place to look as well. Power cables can often be sourced from e-waste, as well. Thankfully, if you can't find wire to reuse, it's not terribly expensive. I collected my wire from a variety of sources. Some was from a repurposed lamp power cord, the plug came from and old window AC, and the smaller wire was leftovers given away by an electronics class. Depending on your base cabinet, you may be able to reuse the original wiring, though it may be quite degraded.
- Casters- While you can certainly find casters from decommissioned equipment, it can be a pain to find ones that work. Since I had to fit a specific screw thread for my project, I wasn't lucky enough to find casters that would fit by the time I needed to finish this project, so I had to purchase mine online.
- Wood Stain- Finding free wood stain is a long shot. You may be able to get some from a yard sale or for free from someone cleaning out their garage, but if you want a specific color, you'll likely have to buy it.
- Rubber cord, or o-rings(Optional)- These may come in handy if there are loose panels on the chassis. You can sometimes find these in the recycling (I did!), but o-rings are more commonly found in junk drawers or stashes of leftover hardware. Worst case scenario, they're very cheap at hardware stores.
Tools are harder to find for free, but with the rise of makerspaces, affordable access to power tools is easier to come by. Alternatively, borrowing tools from a friend or buying cheap hand tools can keep costs down, too! For convenience, I used the tools from a student workshop at my university, but access to all tools needed can be obtained elsewhere rather easily.
Tools:
- Screwdrivers- Access to basic screwdrivers is needed for removing the old internals. An impact driver can make this faster and easier, and is what I used, but ultimately isn't necessary.
- Pliers- Necessary for removing the internals, and also useful for working on the electronics
- Saw- You'll need a saw of some sort to cut the shelves to size. I was lucky enough to have access to a circular saw and a radial arm saw, but a hand saw works just as well. A table saw would be ideal for longer cuts, but sadly I didn't have access to one.
- Clamps (Optional)- Depending on your sawing method, clamps may be necessary. I ended up needing them for the circular saw. If you have extra scrap wood and long enough bolts on hand, clamps can also be improvised.
- Soldering Iron- Needed for the electrical work, at least in my case. Yard sales, thrift shops, and antique stores can be a great place to get one.
- Wire Cutters/Wire Strippers- A pair of cutters and a pair of wire strippers is handy both for removing the old internals, and for wiring up the lights.
- Washcloth, Soap, Paper Towels, Isopropyl Alcohol- The old chassis will almost certainly be extremely dirty. A washcloth and a mild soap will make quick work of quite a bit of the gunk, but isopropanol can help get some of the more stubborn stuff. Avoid using harsher chemicals, as the paint on old equipment can be very easily ruined.
- Heat Gun or Hair Dryer, Tweezers- A heat gun or hair dryer combined with a pair of tweezers will make quick work of any old tape on the chassis.
- Measuring/Marking- A tape measure and pencil or marker are essential. A straight edge is handy as well, but not necessary, and one can easily be improvised. A carpenter's square may be useful, but I didn't use one.
Step 1: Gut the Old Equipment
When I got it, the chassis was extremely dirty, and full of the original equipment. First things first, let's get the inside empty.
Before you start taking things apart, take a few moments to examine the way things are put together. In my case, the modules to be removed were inserts-- They were screwed into a series of smaller frames that were mounted on small horizontal rails running front-to-back in the cabinet.
To get the modules out, I first removed the back panels, which were held on with phillips screws. Make sure to save your hardware! It's essential for remounting removed parts, and if you have extra, you can add to the project later on.
Then, I disconnected the wires connecting the modules together. I cut cable ties holding wiring in place, and removed the wires. The grounding wires were bolted to the case in several places- a pair of pliers was able to unscrew the nuts to free them.
If it's in good shape, you can save the wiring for later reuse. Otherwise, set it aside to recycle.
Next, I removed the phillips screws on the front of the modules, and pulled the modules. These modules can be a great source of electronics parts-- the main power supply had a power switch that still had the key in it, which will make for a nice addition to a future project.
The modules should be recycled, or torn down for parts, if you'd like.
With the modules gone, I was then able to unscrew the bolts holding down the smaller frames, and pull them out of the way.
With the cabinet emptied, it was time to clean!
Step 2: Clean the Chassis
Soap, water, and a washcloth will likely do the job for most of the dirt you're likely to encounter. A broom or vacuum may come in handy if there's debris in the chassis, but aren't strictly necessary.
For tougher gunk, some isopropanol can help to loosen it, if the soap isn't doing the trick. Be sure to scrub gently, as the isopropanol can and will weaken the paint.
The main things you're likely to encounter is old adhesive or tape, from various notes left for others over the years. Take a heat gun or hair dryer, and hit the tape with a bit of heat. This will help to soften the adhesive, but it will primarily soften the tape, making it less brittle. If you can get ahold of the tape with a pair of tweezers, it should come off in one large piece. Be sure not to overheat the tape! If it's melting, turn down the temperature, or hold the heat source further away.
Once the tape is gone, some of the adhesive will remain. Wet a towel with isopropanol, and gently scrub the adhesive residue with it. Note that it isn't the mechanical work doing the removal so much as it is the isopropanol dissolving the adhesive-- adding more isopropanol from time to time helps to carry the adhesive away.
There was a bunch of duct-tape residue right on the front panel, which is acrylic. Technically, acrylic and isopropanol aren't compatible, but it doesn't seem to have hurt it in my case.
With the chassis cleaned up, it's time for shelves!
Step 3: Install the Casters
Carefully tip the chassis on its side, or jack it up on something if you're able to. Screw the casters in, or on, depending on their mounting style. I opted for threaded casters, matching the 3/8" x 16 threads on the chassis' original feet.
Due to how the leverage works out, it is harder to tip the chassis back upright with the casters on than it was to tip it down without them on. A trick for this is to create your own fulcrum- Put a scrap piece of 4x4 (or around the height of your casters) under one edge of the chassis for it to tip up on to. Then, tilt it onto the opposite set of casters and pull the piece out. Now you can move the chassis around without a dolly!
Step 4: Secure Loose Panels
If you have loose panels on your chassis that can't be fixed by tightening screws, rubber cord or o-rings may be the solution. For example, the acrylic window of the door of my chassis was loose.
Cut the o-ring or cord to lengths of 6-8 inches at most. Use a screwdriver to push one end of the rubber into the gap between the frame and the panel you want to secure (preferably, do this from the inside of the chassis). Stretch the rubber to make it thinner, and move along the frame, pushing it in with the screwdriver. The elasticity will cause the rubber to expand, pushing against the panel to keep it in place.
Step 5: Cut the Shelves to Size
With the internals removed, we can now measure for the shelves. I measured the width between the rails, and the depth of the cabinet. The maximum depth my shelves could have been was about 14", but the wood I found was in 2' x 2' panels, so I opted to leave a couple inches of room for the LEDs and potential future wiring. This meant cutting each board in half, making 12" x18" shelves.
Measure out the lumber, and mark straight lines for your cuts if you're free-handing them. If you're using plywood, keep in mind that it may fragment more than solid wood does. Think about what edges on the wood start out straight or square, especially if you're using scrap- if you choose your cuts carefully, you can keep the nicest edges for the front of the shelf.
Dry-fit the shelves as you go! That way, you can tell if you need to adjust your dimensions.
Step 6: Stain the Shelves
There's better guides for wood staining out there, but here's a quick run-down.
Wood stain, unlike paint, is meant to soak into the top layers of the wood it's applied to, and works to bring out the grain rather than cover it. This means it's better wiped on, with a bit of excess, than rolled or brushed on.
Mix your stain well, and dip a rag into it. Wipe down the wood thoroughly. I did the bottom first, and let that dry for a few hours, then went back and did the top and the sides, setting each piece on top of a block of spare wood to keep stain from pooling on the edges, and to keep it from sticking to the plastic drop cloth.
Let the stain dry for 24h after you're done. Because of the drying period, this step can be done earlier on, as soon as you've cut your lumber.
Step 7: Prepare the LEDs
At this point, I should give a brief warning: Do not work with high voltage unless you know what you are doing. Even if you do know what you are doing, use proper precautions; it only takes one accident to severely injure you. If you are not accustomed to working with line voltages (110 V), stick to neopixels or low-voltage LED strips.
That being said...
It's a good idea to test your LEDs ahead of time, especially if there's taken from e-waste. Since the fixture I got my LEDs from was thrown out, hooking up the LED driver and testing the LEDs ahead of time was strictly needed.
Even if they're new, though, it's a good idea to test out your lighting before installing it, so you can troubleshoot any issues that come up.
The LED driver I found runs on 115-240 V, and includes a pair of wires for dimming. This dimmer works in an interesting way- it puts out 10V on the wires, and then measures that voltage. That doesn't seem like it makes sense at first, but there's a catch: there's an internal resistor in series with the +10V wire. This means that by adding a variable resistor between the two wires, you can turn the circuit into a resistor divider, and control the brightness of the LEDs.
For my driver, I found that a 50k potentiometer gave a good range of control over the brightness, but I couldn't find one that I felt would look nice, so I opted to install a switch to alternately short or disconnect the wires, switching between full and minimum brightness.
The LEDs themselves were grouped into three parallel sets of 5 LEDs in series, which meant that by cutting off 5 LEDs, I could shorten the pieces to fit on the backs of my shelves. I also soldered on some small connectors in place of the original wiring connectors, as I'm planning to build computer motherboards onto these shelves in the future, so want to be able to easily disconnect them.
With the LEDs put together, we can build our switch panel!
Step 8: Build the Switch Panel
I wanted a retro and somewhat industrial feel for this project, so for power switching, I collected three switches from older electronic equipment. Two were rotary, and the third was a rocker switch with a power indicator lamp.
I cut a small piece of wood, drilled and cut holes for the switches, and stained it. After using a multimeter to confirm which terminals were connected in what switch position, I mounted the switches in an orientation that I was happy with- the rotary switches are on when rotated to the right.
As always, double-check that your switches are rated for the current you plan to put through them!
This panel was then mounted to the cabinet, ready to be wired to!
Step 9: Plan the Wiring
Plan out the connections needed for the wiring. After you know how many conductors need to go where, you can plan how to physically route them within the cabinet. Since the cabinet came from old electronics equipment, there's plenty of places to tuck wires away to keep them out of sight! Zip ties can help keep wires neat an held in place.
In my case, I planned out the wiring so that power would come in from the bottom, with a cord plugged into the wall. All neutrals would be tied together in the bottom, as well as the grounds. I would run the line wire up to the switch panel, where it would run through the large rotary switch and feed back to the bottom for the power strip, as well as feed the rocker switch, which would in turn power the LED driver. A small neutral wire would also run to the switch panel as a return path for the indicator lamp in the rocker switch. Finally, the LED dimmer wires would run up to the small rotary switch, to control the brightness.
The output of the LED driver would run up the back of the cabinet, branching out a lead for each shelf's set.
Step 10: Install the Wiring
Strip the wires that need to be connected together, and connect them with wire nuts. Technically, junctions of live wires ought to be inside of a junction box, but if you don't have one, electrical tape around the wire nuts is a good idea. Run wires together, and keep them neat-- if you need to add wiring in the future, keeping it neat will make it easy to reconfigure, as well as protect the wiring from accidental snags.
Solder the wires to the switches as necessary, and tape around exposed metal. After you've got everything hooked up, double-check your connections and then test your wiring and switches. Try to get the switches to as many states as possible in as many orders as possible to check for errors. Once you're convinced things are wired up correctly, you can start putting the finishing touches on the project.
Step 11: Install the Shelves
Stick the LEDs to the backs of the shelves, and connect them to the wiring in the cabinet. Secure the shelves to the cabinet however you'd like. I've opted to leave mine unsecured for now, but I plan to work out a peg system to keep them in place but easily removable as part of a future expansion on this project.
Step 12: Play With the Switches, and Enjoy Your Cabinet!
Congratulations! You've now got a retro cabinet with internal lighting, a power strip to power things inside of it, and a cool switch panel to turn it all on and off! The reused switches are delightfully tactile, and fun to play around with. You've got a new place to display trinkets, store things, or build onto! And best of all, you kept it all out of the landfill!
Join me next time, and I'll show you how I plan to make each shelf hold a retro computer, and build an interconnect system to control all of them from a main modern computer.
Attachments
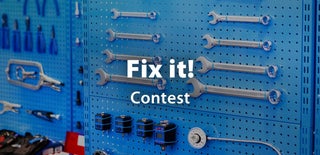
Second Prize in the
Fix It Contest