Introduction: USB Microscope Guided PCB Drill
Most of the printed circuit boards I make at home are simple single sided boards. Drilling requirements are minimal, mostly holes to mount the board and an occasional through-hole component or connector that is only soldered on one side. For these boards I generally use a small, high speed drill press with carbide drills, eyeballing the location and hoping it is "good enough". Unfortunately, often it is NOT good enough, and a lot of the holes have to be enlarged or elongated to fit.
Now that I am attempting double sided PCBs using my modified E260 laser printer to print toner directly on the copperclad board (see E260 Instructable), I realized that my hole drilling has to be a lot more accurate. So I decided to build a USB Microscope Guided PCB Drill.
The subject of PCB drilling has come up many times on the Homebrew_PCBs Yahoo Group. Among the many interesting thoughts was Harvey White's description of the PCB drill he had constructed using a TV camera and a homemade drill that drilled holes from the bottom of the PCB rather than the top. It also featured a stepper motor driven Z axis carrying a high speed rotary tool as a spindle.
The main advantage of bottom-up drilling is that dust from the drill does not obscure the camera's view. A secondary advantage is that the camera does not have to take up a lot of space below the drill table. I decided to build my PCB Drill in the inverted configuration but elected to use an off the shelf drill press with a manual Z axis.
Confession:
I am not a machinist. I have a $60 Chinese drill press, an electric drill and some hand tools but it is important to note that I am not a very good machinist, and my machining tends to be of the "Machining for Dummies" variety. The drawings are to scale and accurate, but careful inspection of the photographs will show that some of my holes are not perfectly centered or placed. It all works because I have designed this "build" to be self correcting and self aligning. Unless you are a competent machinist I suggest you drill and cut following my directions, rather than just going by the drawings.
Step 1: Parts and Tools
Parts
Drill Press - I am using a small Chinese 3 speed drill press that has a maximum speed of 8500 rpm and can be purchased for $69.00 USD or less from many vendors. See the photos then do a search for "6 mm Drill Press" for sources. Note that this modification has only been used with this drill press. With any other drill press you are on your own!!
USB Microscope - I am using a Digimicro unit purchased on eBay for $28.00 USD, but any similar one should work.
Aluminum Rectangular Tubing - 2"x4" x .125" wall thickness cut to 3.5 inches long. Available at Online Metals, 6061-T6 aluminum.
Aluminum Plate - 4"x6"x.250" thick. Available at Online Metals, 6061-T651 aluminum.
Aluminum Bar - 1'x.125" thick x 1 foot long. Available at Online Metals, 6061-T6511.
Polycarbonate strip - .093 thick x 1" wide. You can buy 12"x12" from Online Metals and cut it or a 1" wide strip is available at McMaster-Carr.
Note that I have given the alloy type on the aluminum parts for reference only in finding them on Online Metals. The actual alloy used is not important and any reasonable alloy will work.
Tools
Drill Press and drills.
Drills and Taps for 4-40, 8-32 and 10-32 screws. Metric equivalents are also fine.
Thin double stick tape. Double sided masking tape or carpet tape will do.
Super Glue.
The usual workshop tools.
Warning: Wear safety glasses at all times! Some of these
operations can result in metal or plastic pieces flying towards your eyes!
Step 2: Definitions
In the text I will be referring to various components that I have added to the drill press. Drawings of each are appended below.
Rectangle - An aluminum rectangular tube, 2” x 4” with .125 inch thick walls, cut to 3.5 inches long. This is the part that mounts directly to the drill press.
Plate – An aluminum plate, 6 inch x 4 inch x .250 inches thick. This part is bolted to the Rectangle. It has a flat surface for the PCB to rest on and supports the Spacer and Bar.
Bar – An aluminum bar, 1 inch wide x .125 inches long x 5 inches long. This part is cantilevered over the Plate and holds the microscope over the PCB.
Spacer – A piece of the same material as the Bar, 1.75 inches long. It sits between the Plate and the Bar and keeps the Bar .125 inches above the Plate.
Mic-Mt – The microscope mount is a 1 inch wide x 2 inch long x .093 inch thick piece of polycarbonate plastic. It is glued to the microscope and attaches to the Bar to support the microscope over the PCB.
Step 3: Preparing the Drill Press
The Drill Press has a cast aluminum case enclosing the motor and spindle assembly. We are first going to remove the motor to get access to the bottom of the enclosure for the purpose of drilling mounting holes for the Rectangle. Using the photos for reference:
Remove the top cover of the Drill Press.
Remove the belt.
Remove the Spindle Pulley. Loosen the setscrew then use 2 screwdrivers as shown to lift the pulley off the shaft.
Remove the 2 screws holding the motor bracket to the spindle.
Remove the Grounding Screw.
Remove the Motor, giving it support so there is no tension on the wires.
Use painter's tape or masking tape to cover the spindle for protection from chips generated in the following steps.
Remove the Head Stock from the column, turn it upside down and replace it on the column.
On the bottom of the enclosure there is a pattern of rectangular holes around a central square cutout. As per the photos drill a #21 (.159) hole in each of the 4 corner holes and tap them for 10-32 screws.
Deburr the holes with a file, then use a shop vacuum and/or blower to remove all the metal chips.
Remove the Head Stock from the column, turn it right side up and replace it on the column.
Remove the protective tape from the spindle and do a final check for metal chips.
Replace the Motor in the enclosure.
Replace the Grounding Screw.
Replace the 2 screws holding the motor bracket to the spindle.
Replace the Spindle Pulley. The setscrew goes on the shaft flat.
Set the Drill Press to the highest speed by replacing the belt on the uppermost set of pulleys, then retension the belt if necessary using the two nuts on the motor mounting screws.
Replace the Cover.
Remove the Head Stock from the column, turn it upside down and replace it on the column.
Step 4: Making the Rectangle
File the cut edges of the 2x4 rectangle. Note that the cut ends of the Rectangle are not square. Unless you have the tools and skills to face the cut and make it square, you will have to layout the 4 holes below using a line perpendicular to the side of the Rectangle as a reference line. The line should be approximately .375 from the cut edge. See Rectangle.pdf.
Using Rectangle.pdf, appended below, as a guide, layout, center punch and drill the 4 x .203 mounting holes on the bottom of the rectangle to match the holes drilled in the Drill Press enclosure. The open end of the rectangle faces the column as shown, with the rear edge just clearing the raised ring that circles the column. The holes have to be completely through both sides of the rectangle. If you have a very good drill press and a long enough bit you can just drill it in one pass. If, like me, your skills and tools are limited, you can lay out the other side of the Rectangle and drill it separately. The upper side is not critical since you will be enlarging the holes to clear a screwdriver or hex key.
The screws holding the Rectangle to the Drill Press will be tightened from the top of the Rectangle, so you must enlarge the top holes to allow your screwdriver (or hex key if you are using cap screws) to pass through the rectangle. I am using regular slotted screws so I used a .5 inch drill to allow a large screwdriver to pass.
Deburr the holes.
Mount the Rectangle on the Drill Press to be sure the holes line up. If they don't, you can enlarge the holes a bit and try again. If it still won't fit, you can "elongate" one or more of the holes with a small file.
Take the 6 x 4 x .250 inch Plate and draw a centerline down the long axis. It doesn't have to be perfectly centered but it should be close.
Put a short bit in the drill chuck so that the tip does not project above the plane of the Rectangle.
Align the Plate on the Rectangle as shown in the photos, with the centerline down and the overhang over the spindle. Slowly raise the spindle. The drill should hit the Plate approximately on the midline. If it doesn't, loosen the screws on the Rectangle and readjust the position of the Rectangle. If you still cannot align the Rectangle properly, make the holes in the bottom of the Rectangle larger. If the holes end up very large just use a lock washer and a washer on the screw to hold the Rectangle in place. No Problem!
Attachments
Step 5: Making the Plate, Bar, and Spacer
Remove the Rectangle and use thin (not foam) double stick tape to temporarily attach the 4x6x.250 inch aluminum Plate to the Rectangle as shown in the photos. I used 2 inch wide double-sided masking tape, but carpet tape would probably do. The rear of the plate should be even with the rear edge of the Rectangle. Make sure it is oriented properly with the holes on the bottom of the Rectangle on the side opposite the overhang. The centerline drawn in the previous step should be on the bottom of the overhang.
Cut a 5 inch piece of the 1x.125 inch bar. The piece I had was anodized, but plain aluminum is fine. Place a piece of double stick tape as shown, approximately centered and running the length of the Plate. Carefully place the Bar on the tape so it is on the center of the Plate with one end of the Bar aligned to the rear of the Plate, i.e. over the Rectangle. See the photos. One way to do this is to put a 1.5 inch wide piece of cardboard on each side of the Bar making a 1 inch channel for the Bar. Check to be sure the Bar is centered. If not, pull up the tape up and redo it.
Using Plate.pdf as a guide, layout and center punch the 4 x .136 (#29) corner holes in the Plate and the 2 holes in the Bar. Then drill the six holes going through both the Plate and the Rectangle in the corners and through the Bar, the Plate and the Rectangle in the 2 center holes.
Mark the top surface of both the Bar and the Plate, then remove the tape and separate all three aluminum parts.
Tap the 4 corner holes in the Rectangle for 8-32 screws.
Use a .1719 (11/64) drill to enlarge the 2 center holes in the Rectangle to clear the 8-32 screws.
Tap the 2 center holes in the Plate for 8-32 screws.
Use a .1719 (11/64) drill to enlarge the 4 corner holes in the Plate to clear the 8-32 screws.
Countersink the lower 2 holes as shown in Plate.pdf so that the screw heads do not project above the surface of the Plate. I used a .3125 (5/16) inch drill as a countersink. Make sure you drill from the top of the Plate. Use a depth stop if your drill press has one, but in any case be careful not to countersink completely through the Plate!
Cut a 1.75 inch piece of the 1 x .125 inch bar. This will be used as a Spacer between the bar and the Plate to raise the Bar above the Plate. Drill 2 holes as shown in Bar.pdf. The holes are shown as .1719 (11/64) inch to clear the 8-32 screws, but they can be much larger in diameter if your measurements are a little off. File the cut ends and deburr the holes.
Step 6: Mounting the Rectangle to the Drill Press
Position and mount the Rectangle to the Drill Press using 4 x 10-32 x .5 inch long machine screws and lock washers. Use a washer if your holes are very large. Do not fully tighten the screws at this time.
Put a short bit in the drill chuck so that the tip does not project above the plane of the Rectangle.
Mount the Plate on the Rectangle using 4 x 8-32 x .5 inch long screws in the corners. Slowly raise the spindle. The drill should hit the Plate on the midline. If it doesn't, try sliding the Rectangle by tapping it with a rubber hammer or the handle of a screwdriver. If it won't move, remove the Plate, loosen the screws on the Rectangle and readjust the position of the Rectangle. Once the Rectangle is properly positioned tighten the 4 screws holding it to the Drill Press. You will not be removing the Rectangle again.
Step 7: Drilling and Mounting the Bar and the Spacer
Mount the Bar to the Plate using 2 x 8-32 x .375 inch screws. Do not use the Spacer at this time.
Turn the drill on and gently raise the spindle to mark the center of the spindle on the bottom of the Plate. Do NOT try to drill completely through the Plate - the drill might break! Stop and unplug the drill, then remove the Plate with the attached Bar.
Place the assembly on your drill press, Bar down. Place a piece of .125 aluminum on each side of the bar to support the Plate, and drill a pilot hole completely through the Plate and the Bar. Put a small piece of plastic or wood on the drill press table so that the screw heads don't touch the table.
Now drill a .5 inch spindle hole through the Bar and the Plate, enlarging the pilot hole. You can drill them both together or separate them and drill them one at a time. Separate them and deburr the holes.
Mount the Plate. Examine the holes in the Plate at the countersinks and spindle hole to be sure there are no burrs or "lips". You can lightly sand the Plate go provide a smooth, flat surface for the PCB to slide over when you are drilling PCB holes.
Mount the Bar, this time using the Spacer between the Bar and the Plate. Be sure the Spacer is oriented properly, with the long end towards the rear. The spindle holes in the Plate and Bar should also be aligned.
Now raise the spindle. The drill should be more or less centered in the hole. If it is not, remove the Plate and Bar, loosen the 10-32 screws holding the Rectangle to the Drill Press, and reposition the Rectangle. Yes, I know I said we won't be loosening these screws again, but this is Machining for Dummies, and you always get a second chance! If you cannot get it centered, enlarge the holes in the Rectangle. If they are already very large, you can enlarge the holes in the Plate, but I would save this as a last resort.
Step 8: Testing and Mounting the Microscope
Download and install the Celestron MicroCapture Pro ver 2.3 software at Celestron.com
Plug the Microscope into a USB port and open the program. The Microscope should be recognized and you should be able to see a centered crosshair.
Place the Microscope on its included stand and aim it down at a PCB. Turn the LEDs on and focus on the PCB. Note that moving the PCB under the microscope results in different movements on the display depending on the orientation of the Microscope. For my Microscope, orienting it so that the LED switch faces away from me, gives a "normal" perspective on the display, i.e. moving the PCB up is up, down is down, left is left and right is right. There is a small black square at the interface of the black case and the clear plastic end of the Microscope at both the switch and opposite sides. These will be useful landmarks when you mount the Microscope on the Drill Press.
Remove the Microscope from the stand.
Cut a piece of .093 thick Polycarbonate or other acrylic-like plastic to 1 x 2 inches. Following Mic-Mt.pdf (below) drill a .5 inch hole as shown.
Drill two .250 holes in the plastic as shown. Smooth the holes and all edges.
We are now going to glue the microscope to the Mic-Mt. We will need some way to support the Microscope while the glue is curing. You can use the stand that comes with the Microscope, but I chose to put a hose clamp gently around the body of the Microscope and slide it into a hollow post on the top of a shelf. This was very sturdy and kept it out of the way for the 24 hours it took for the glue to completely cure.
Clean the front of the Microscope and the Mic-Mt. Place the Mic-Mt on a clean flat surface and put the front of the Microscope against the Mic-Mt with the opening centered in the large hole. Make sure the Microscope is oriented properly so that the image will move correctly on the screen! The small black square should be facing the short end of the Mic-Mt.
Keeping moderate pressure on the Microscope, squeeze a few drops of Super Glue at the interface and gently rock the Microscope a bit to allow the glue to distribute itself completely around the interface. Hold the position for 30 seconds.
Lift the Microscope. The Mic-Mt should be attached but you should still be able to move it in the softened plastic. Gently position it so that the Microscope is centered in the opening and oriented correctly with the switch pointing towards the long end of the Mic-Mt. Put the Microscope safely away for 24 hours to allow the glue to fully cure.
After the glue has fully cured, plug the Microscope into a USB ports and open the MicroCapture program. Place the Microscope on the Bar, positioned over the large hole with the short end of the Mic-Mt to the front, closest to the spindle. Turn on the LEDs, put a PCB on the Plate, between the Plate and the Bar and focus the Microscope. Make sure moving the PCB results in the proper orientation of movements on the display.
Remove the PCB. With no drill in the chuck, close the chuck and tighten it. Focus the Microscope on the center of the chuck then carefully center the Microscope over the center of the chuck so that the intersection of the crosshairs is directly over the center of the chuck. Hold it in position with your fingers and place a dot on the Bar with a pencil or Sharpie in the center of each of the .250 holes in the Mount. Remove the Microscope.
Remove the Bar from the Plate.
Center tap the Bar at both of the dots, then drill a #43 (.089) hole at each location. Tap the holes for a 4-40 screw.
Mount the Bar and Spacer being careful to align the large hole to the hole in the Plate
Use two 4-40 x .250 long screws with 6-32 nuts as washers to mount the Mic-Mt to the Bar as shown in the photos. Leave the screws loose for now.
Connect the Microscope to a USB port and open the software. With no drill in the chuck, close the chuck and tighten it. Focus the Microscope on the center of the chuck then carefully center the Microscope over the center of the chuck so that the intersection of the crosshairs is directly over the center of the chuck. Tighten the 4-40 screws. Check to see that the alignment is still good. If not, loosen the screws and try again. It doesn't have to be perfect for now.
Attachments
Step 9: Using the PCB Drill
The drill is designed to use the 1.5 inch long carbide drills commonly used to drill PCBs. These drills have a .125 inch diameter shank and come either with or without depth rings. I like the rings, but the drill can use bits of any diameter up to 6mm, with or without rings.
Since the spindle is so close to the plate, it is necessary to completely open the chuck and "wiggle" the bit into place. Once you’ve done it a few times it’s pretty easy.
For "final" calibration of the Microscope loosen the screws holding the Microscope. Put a small hose clamp around the chuck, leaving it loose for now. Place a small piece of .125 material under the front edge of the Bar to support the Bar, and put a small diameter bit in the drill. Now, using the lever arm of the Drill Press bring the spindle up so that the tip of the drill is just a little above the Plate. Tighten the hose clamp so it holds the drill in that position by resting on the Rectangle. See the photos for details.
Connect the Microscope, open the software and turn the LEDs on. Focus on the tip of the drill point and center the tip in the crosshairs. Now tighten the Microscope screws. Recheck the calibration and loosen the screws and redo if it is not in perfect alignment. Your drill is now ready to be used!
The drill can handle PCBs up to about 4.5 inches wide. To drill, insert the proper drill bit, start the drill, turn on the Microscope and set the software to Full Screen. Carefully position the crosshairs on the center of the hole. Hold the PCB in place with two fingers of your right hand and gently bring the spindle up with your left hand until you see the bit coming through the PCB on the screen. The photos show a .021 inch hole being drilled in some lettering on a PCB.
After using the drill a while, I noticed that the vibration of the drill had a tendency to shake the Microscope out of focus. This is easily remedied by focusing on the PCB then putting either a piece of tape or a rubber band around the Microscope and focusing knob.
Note that you can use the Drill Press for normal drilling by removing the Plate, attached Bar and Microscope and reversing the Head Stock to its normal position.
Step 10: Going Forward
The USB Microscope guided PCB Drill is an easy way to drill accurate holes in printed circuit boards, but if I had to drill a lot of holes, I would want a motorized plunge, i.e. a motor to raise and lower the spindle. This could be a linear actuator directly pressing on the motor mounting plate in the head or possibly it could raise and lower the feed wheel lever directly. A third possibility is a geared motor and belt connected to a pulley on the feed wheel hub.
Another place that could use improvement is the Microscope. The Microscope and Bar take an inch of width where you cannot see the PCB. If there are a lot of holes to be drilled in a small area you can sometimes lose track of which hole you are seeing on the screen. Perhaps a Borescope with a 5mm head would be a better choice than a Microscope, but that will be left for another time.
Now that I can drill accurate holes I will be experimenting with making double sided PCBs using my modified E260 laser printer. Look for my next Instructable!
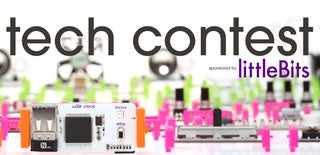
Participated in the
Tech Contest