Introduction: Ultimate Electronics Helper || Variable Bench Top PSU With Helping Hands
When working with electronics two tools are pretty much always needed. Today we'll be creating these two essentials. And we'll also take it one step further and merge these two together into the ultimate electronics helper!
I'm of course talking about a Variable Bench Top PSU and a good pair of Helping hands!
The PSU features variable voltage and current so it can be used in any number of projects. It also has a constant 5V output from a USB connector. As you've probably experienced a lot of DIY electronics projects require 5V and some other voltage.
Helping hands always need a sturdy base to keep everything still. This is solved by mounting them onto a power supply unit, which usually weighs a lot.
Let's get started!
Step 1: Parts and Tools
Parts
- Old laptop charger
- Buck boost converter $8.24
- Potentiometers 2 pieces. $0.43
- 200k ohm
- Potmeter knobs 2 pieces. $0.60
- LCD with voltmeter $2.48
- Female banana plugs $1.17
- Male banana plugs $1.18
- Toggle switch $0.24
- Step down converter $1.09
- Female USB 1 piece. $0.09
- CNC tubes 3 pieces. $1.44
- Alligator clips 3 pieces. $0.36
- Heat shrink tubing
M3 screws with nuts
- 15 pieces
- Between 10 to 16 mm long screws
Tools
- Super glue
- Soldering iron
- Wire strippers
- A lighter
- 3D printer
- Super glue
Step 2: Wielding the Power
To make the power supply unit I used an old laptop charger. This was free of charge because I have several old chargers laying around. To make this project I used the beefiest I had which was at 65W. Old chargers are a great fit for a compact bench PSU because they are made in small sizes but still provide a decent amount of power.
The voltage and current will be controlled by a chip which is capable of both stepping up and stepping down the voltage. It has a output range of 1.25V to 30V, and 0.2A to 10A. This is adjusted by turning potentiometers on the power controller board.
Step 3: Power Output
To deliver the power to I'm using two different sets of connectors. There are regular banana plugs for the variable output. These are commonly used and you can get a lot of different connectors for these. I used male banana plugs connected to a pair of alligator clips.
For the constant 5V ouput I'm using a female USB connector. A lot of projects require 5V along with some other voltage. This also means the bench PSU can power any USB powered device, so you can also use this to charge your phone!
It's really useful to have more than one output!
Step 4: Upgrading Potentiometers
To make it easier to control the voltage and current I'm replacing the small trim potmeters. I desoldered these by pushing a small screwdriver between the trim pot and the PCB, while applying heat on the solder joints. I did this for a while alternating where the heat was placed until the trim pot fell out. This was then replaced with a regular rotary potentiometer with linear resistance between zero and 200k ohms.
Step 5: The Complete Circuit
Now this is going to be the complete circuit. The laptop charger is connected to the buck-boost converter in parallel with the power going to the LCD screen. This is also connected to the smaller and constant step down converter. The smaller step down module's output is fed to a USB connector.
I also went ahead and added a simple toggle switch in line with the laptop charger output.
The variable output is then connected to a pair of banana plugs to serve as outputs. These also have wires running to the measuring inputs on the LCD screen.
Step 6: 3D Printing
Here you can download the 3D files in both .STL and Fusion 360 files (.f3d). I've included these files to make it easier if you want to edit parts of the case for your own use. Everything is designed in Fusion 360 so the timeline has captured the complete design history if you want to look into it! You can also download the STL files here.
All parts are made with nice margins so everything should fit together easily. This also means you have room for several different power supplies and electronics if you want to switch out anything later on.
I printed everything except the helping hands adapters at 0.3 mm which was the roughest resolution on my printer. The adapters were printed at 0.1 mm. All in all it took about seven hours printing everything in PLA and 5% infill for strength.
Step 7: The Thing About Lending a Hand
As mentioned in the intro of this project helping hands always need a sturdy and heavy base. This is important to make sure the hands stay put when you apply force on them while soldering. You really don't want the hands moving around while they hold a small circuit. In this project this solved by mounting the helping hands onto the side of the bench PSU as this has a sufficiently heavy weight.
Alligator clips has a strong grip. To avoid them biting too hard into the surface or shorting any electronics we're going to add some heat shrink tubing on the teeth.
Step 8: Bring Your Hands Together
The best way to secure the alligator clips is to first cut the edges on the tubes, just enough to slip one in. To make sure everything was held in place I added a tiny drop of super glue. To make the alligator clips better suited for our purpose we're adding heat shrink tubing on their teeth. Slide some heat shrink tubing onto the clip and cut the tube at the end. Repeat this for the other side. Now with both pieces of tubing on the ends apply a heat source. I used a lighter rapidly moving back and forth under the tubing while I rotated the clip.
To prepare the helpings hands for mounting onto the case I first pulled off the orange screw terminals on the CNC tubes. Then with a bit of force I pushed the open end on the tubes onto the 3D printed adapter. The adapter has a ball joint just like the rest of the CNC tubes which means it can freely rotate into whatever position you need!
Step 9: Front Panel
The potentiometers and banana plugs came with the necessary nuts. Just insert these through the front panel and fasten with the nuts. The LCD and switch are simply pushed into its place. Because I tested the complete circuit before mounting it, I had to desolder the switch before it was pushed into the front panel. Luckily all other parts could be mounted without any desoldering!
The USB connector had to be glued in place. To align it flush to the front I taped down a piece of duct tape on the outside. This held the USB in place while I applied hot glue.
I have attached the .dxf file for the front panel so you can still make it without a 3D printer.
Attachments
Step 10: Prepping the Roof
The lid on the case has four pockets with room for an M3 nut each. The nut is pushed into this pocket. I used a pair of tweezers and later a screw through the pocket hole to make sure the nut was perfectly aligned! When the nut was in its right place I applied a dab of hot glue to keep it in place when I removed the screw. Repeat this three more times.
Now the lid has threaded holes in each corner and can easily be screwed on top of the case!
Step 11: Coming Together
Okay! We've made all the parts we need. Now it's just a matter of bringing it all together! On the case itself I started by mounting the helping hands adapters. This was done while I still had room to work on the inside. After this the charger was glued in place, with quite a bit of hot glue. Just to make sure it doesn't come loose. The two voltage regulators were placed on the floor. Making sure the wires weren't tangled way too much.
When everything is stuffed inside it's time to put in the front panel. I used a pair of tweezers to hold the nuts on the inside of the panel while using a screwdriver on the outside.
After preparing the lid in the previous step it's simply a matter of placing it on top of the case and insert screws into each hole.
To finish off the front I added a couple of knobs on the potentiometers. This makes it look much nicer!
Step 12: Finished!
And now with everything complete, just plug in the power and switch it on! Now you can control both voltage and current in whatever circuit you're prototyping, and you have a few extra hands for soldering!
Final thoughts:
The case has room for several different sets of electronics. However you may still edit the 3D files in Fusion 360 to better suit your own. Leave a picture in the comments to let me see!
The potentiometers I used were single turn. I believe it would be better to get the same value, but in a multi turn version. This should make it much easier to fine tune the variable voltage and current.
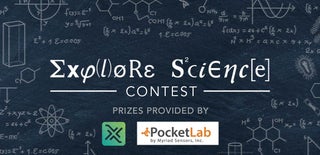
Second Prize in the
Explore Science Contest 2017
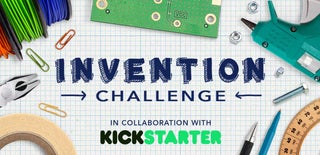
Runner Up in the
Invention Challenge 2017
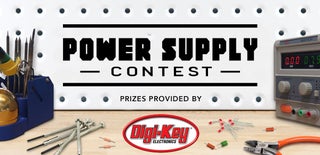
First Prize in the
Power Supply Contest