Introduction: Water Organ
Playing with water and making music are both some of the most fun things to do in summer. So when I was asked to make a musical play object for the Muziek op de Dommel festival, I decided to bring water and music together and make a water organ.
The organ makes sound by spraying water on a plastic sheet tensed around the end of a pipe. The pipes amplify the sound of the plastic membrane like a drum. By using different size of pipes, you get different notes and you can build a full instrument! I made three different mechanisms to spray the water: one handle, some valves and a free hanging tube for spraying everywhere. Through this Instructable I will show how I made the organ, and hopefully you can make something similar too! If you like it, please vote for me in the contests. :)
Step 1: Concept
Like any project, I started by thinking hard, drawing a lot and discussing the ideas. Through considering huge thundering structures, to physical sequencers, I finally came to this plan: a structure with many organ pipes, all tuned to the key of C ("the scale of the sun"), and many different mechanisms to play it.
Step 2: Design
To figure out the shape and sizes, I made a few 3d models in SolidWorks. This is for me a really good way to define the object precisely so I get the right information to start building. It helps to make things really concrete.
Take a look at the 3D file, you will find there all the elements in detail.
Attachments
Step 3: Calculate and Order
The pipes needed to be tuned to specific pitches, so I got scared I would need to experiment forever to find the sizes for all 50 pipes. But fear not, some Excel magic can save us from all this trouble.
If you are planning to make your own version of the water organ you can find out how to tune the pipes in the following steps. Otherwise, you can use directly the sizes from the 3D model.
The cool thing about SolidWorks is that you can link a model and an Excel sheet through "design table". There are a few things to keep in mind, by checking out this links you will find everything you need to know to tune your pipes:
- Pipes need to have a specific length for a specific tone
- There is an ideal length - diameter ratio
- The pitch is slightly influenced by the diameter
- Only specific diameters are available (eg. 10cm, 12cm, 15cm etc)
- The instrument needed to be on the right height for children
As you can see in the images, I made some formula's to make sense of all this and made that feed back into the model for the actual sizes. It is also possible to go wild and just try around!
With all the right sizes and the designs of the connector pieces, I went to search for a supplier. Seeing I needed so many pipes, it was really worth it not to settle for the first one I encountered; after a good search online I found a supplier which was almost four times cheaper than my local home depot. It even got delivered to my home, instead of needing to transport myself!
Step 4: Cut Everything
Finally, we get to the practical part. I copied all the sizes from the 3d model and just started cutting.
Hard and long work, but it is very satisfying to slowly see this pile of tuned pipes arising. Very cool is when you hit a pipe with the palm of your hand, you can already hear the tuned note!
Don't forget to cut also pipes for the handles and for the structure. In my version, I used 3 big pipes to support the whole thing (see model).
Step 5: Glue Pieces
The connector pieces can now be glued together.
All the sounding pipes go through two planks. To maintain the pipes at the right height, you can use pvc rings. It will prevent the pipes from sliding down the holes in the plank. Once you decided on the perfect height you should glue the rings to the pipes. For a good seal, it is important to clean very well, I used specific PVC cleaner. I used the glue Griffon T88 for both tasks. Some parts needed to be modified a bit in their shape, I just used a rough wood file for this.
Step 6: Cut Plate
To form the plank structure, I used some waterproof particle board. Again, I roughly took the measurements from the 3d model but kept some freedom of interpretation.
Because you needed to have two identical plates, you can clamp two boards together and start by drilling the biggest holes.
To cut those big holes, I used an adjustable drill. I was happy that particle board is quite easy to drill, because using a drill like this on a hard board might have taken a very long time. That's something to take in consideration when choosing the wood.
After drilling all the holes, you can use a jigsaw to make the outer contours.
Sand everything thoroughly to avoid people from hurting themselves.
And finally, use some glue (any water resistant woodglue) to seal the open edges and make the board waterproof again.
(While the particle board worked fine, for a next time I would choose to use concrete plex, as it's more stiff and better resistant to water. But on the other hand it would have made the drilling take a lot more time. I would totally recommend it if you have better drilling equipment.)
Step 7: Paint Everything
The most tedious part of the construction: painting over 50 pipes!
But it's worth it! The children like it a lot and this way you can set apart the different sections of the organ by giving them a color (in my case parts corresponding with the handle, the one corresponding with the valve, etc.). I chose four bright colors.
First I sanded all the tubes, I cleaned them with PCV cleaner and I primed them with PVC primer once. Then I needed to put on three layers of color with a roller.
Each round of sanding/painting took about two hours and it needed to dry 8 hours. So I spend almost three full days painting!
If anyone has a better suggestion for this process, I think it could get improved!
Step 8: Assemble
Finally all the parts are ready, time for assembly! Again holding the plans from the 3d model close, I could slowly build up the instrument!
First you can set up the three 'leg' pipes and then put the planks over them. Now, all the sounding pipes can be placed in their hole. For the membranes, you can use the kind of transparent, thick, plastic bags. Place it over a pipe and close tightly with a metal pipe clamp and then cut off the leftover material.
At the same time, you can construct the handles and also fit them into the structure.
Step 9: Don't Hate, Demostrate!
Last thing, connect the tubes, let the water flow and have fun!
You can check the water organ in action in this video I made, I was really happy to see the kids having fun with it.
Thanks for reading!
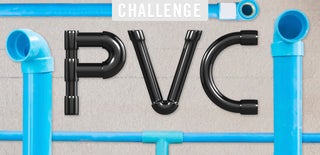
Grand Prize in the
PVC Challenge
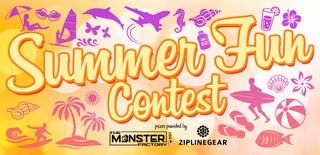
Second Prize in the
Summer Fun Contest
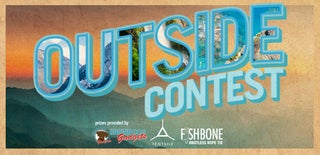
Participated in the
Outside Contest