Introduction: Wing From Scratch
This Instructable is going to show you how to make a cheap inexpensive airfoil or wing for your project. Airfoils or wings are found on things all around us. They can be found on boats, planes, cars, windmills, and much more. A lot of research has been done on airfoil shapes but for this instructable we are going to have fun and hope for the best.
Supplies
Super Glue, knife, tape measure, heat gun, saw, wood, pencil etc...
Step 1: Collect Wood and Tools
Collect your supplies and tools. The wood in the photo is balsa wood. Balsa wood is a very light weight wood. We got our wood from a yard sale but this type of wood can be found at craft supply stores.
You will also need tools. The tools I used are simple tools that can be found around the house or in any tool shop.
Step 2: Tracing and Cutting
We are now ready to design the shape of our wing. The shape of our wing and any other wing serves a purpose. The purpose of the shape is to create lift. In a wing, lift is a force that lifts the plane. The math formulas to figure out the best design for lift is beyond the scope of this project. If you are unsure of wing shape just search the internet.
Next, we are going to make a template of the wing shape. We used a thicker piece of balsa wood but templates can be made from anything. The template is going to give us the same size parts to cut out many times. Lay the template on the wood so you get the most parts from one board. Trace the template with pencil or marker.
Safety is very important when cutting wood. Wood can be unpredictable and give to stresses or loads in an instant. Always cut away from yourself and others and wear cut resistant gloves. Power tools are an overkill for balsa wood but always follow the manufacture safety instructions. Dust from cutting and sanding can get into eyes and lungs so use a dusk mask and safety glass. And have adult supervise you.
When cutting the wood it is easiest to cut away large sections then work your way around the trace lines. The pieces you just made are called "ribs". Notice in the photos that a large and small square were traced and cut out. These squares are for a long wood stick to lay in. The next step will show more.
Step 3: Pin and Glue
The long "stick" is called a "spar". A spar is the backbone of the wing supporting the ribs.
For this project we used a 1/4"x1/4" wood stick and a slightly smaller one that would be our spars. One on the bottom and one on the top. You can use anything for a spar but it needs to be strong and light. Measure and cut spar notches in your ribs like my square ones. Measure and mark your spar so that you will have evenly spaced marks down the length. These marks are where the ribs will be glues. We used 3" spaces between ribs.
The first step was to hold down the bottom spar. We used sewing pins and a styrofoam table top. The goal is to pin our parts in place so we can super glue. Next, we lined our ribs up on our spar marks. We pushed pins through the rib wood into the styrofoam. Once the ribs are in place and lined up you can glue.
Super glue is toxic and dangerous. Fumes can get into eyes, lungs, and mouth. Super glue is permanent and will instantly glue fingers together or fingers to balsa wood! However, super glue is strong and fast. Drying time can be even faster if you use an "accelerator". Accelerators can be sprayed onto the glue for instant dry. Also, super glue solvent is a handy item to have when working with this type of glue. Super glue solvent will prevent an embarrassing trip to hospital if you glue your finger to your forehead.
Step 4: Leading Edge of the Airfoil.
On this airfoil we decided to cove the leading edge(front) of the wing with wood. Covering the front of the wing was a design option for this project and isn't necessary.
We cut a length of balsa wood that was wide enough to wrap around the front of the ribs. This wood needed to be flexible so we wrapped it in paper towel and soaked it. Water and 30 minutes was enough time to bend the wood easily. We pinned and slowly wrapped the wood. Water will squeeze out of the wood grains as you bend. Once the bend is done, pin it in place. Glue and let dry.
Step 5: Wrapping the Wing.
For a wing to function properly it must be covered with some sort of material. This material should be light and strong. Remote control planes typically use Monokote as a covering. Monokote feels like a thin plastic that sticks to itself when heated. Heat will also make the Monokote tighten and shrink.
For this project Monokote was not available so we improvised with plastic that is used to seal house windows and doors. The plastic is very light, shrinkable, available and the price was right. The box contained a roll of two sided tape and a large sheet of plastic.
On our wing we laid down the double sided tape on the bottom wood of the leading edge. The tape must stick to the wood. Peeling the top of the tape off will expose the sticky strip underneath. Next, take the window plastic and lay it down on your work space so wing can lay on top. Now pull the plastic so it comes up and around the leading edge of the wing. Push the plastic into the double sided stick tape. Press the plastic into the tape.
Now, add more tape onto the top of the last tape strip. This will create an plastic envelope around the wing. Pull the protective cover off the tape and press wrapped plastic into tape. Tape the ends of the wing in the same fashion. Once, all the plastic is taped you are ready to shrink the plastic.
Step 6: Heat and Shrink.
Using a hair dryer or heat gun can burn skin and start fires, use cation!
This part seems the easiest and the most fun if done correctly, if not then you may need to go back and rewrap the wing with plastic. The plastic melts fast if you use to much heat!
Lay the wing down and using low heat blow on the wing. Stay 6-8 inches away and move quickly. Stopping will melt plastic. As the plastic heats it will also tighten. When wrinkles in the plastic disappear you are done!
*Note-water vapor is trapped inside my wing causing water streaks and fog. This is due to not allowing enough time for the leading edge wood to dry.
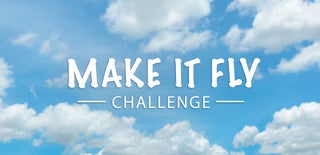
Participated in the
Make It Fly Challenge