Introduction: Wire Hose Clamp Tool
Here goes... everyone has a first, here is mine. I need a hose clamp for my project, but it's 11:30pm and Bunnings ain't open... also hose clamps cost money, and I don't like spending money. Argh!, and hose clamps leak........BAHHHH!!!
So I needed to make a wire hose clamp tool. I Googled it, and found a bunch of different designs - none that seemed very simple to make. I jerry-rigged something for that one problem and then started coming up with better designs. This is my favourite of my designs.
This very handy tool not only makes hose clamps, it mends broken handles and makes insanely tight lashings. It is not only a tool for the shed, but also for out bush or on the road.
Step 1: Tools and Materials
So you need some stuff....
Tools
Hammer, butane torch (https://goo.gl/QdQv5h), vice, 2.5mm and 5mm metal drill bits, drill, centre punch, ruler, hacksaw, sidecutter, safety glasses and leather gloves.
Material
~6mm mild steel rod, ~270mm long (a thick tent peg works). This if for the turner, if it is smaller than 6mm you run the risk of it breaking where you drill it (see picture).
~5mm mild steel rod, ~230mm long (medium tent peg!)
Step 2: Measuring, Cutting, Heating and Bending
Cut your 6mm steel rod to ~270mm long. Mark at 70mm from one end, then 70mm again from that mark.
Chuck on your heat resistant leather gloves. Heat up your first mark with the butane torch till its red hot, then clamp it in the vice and bend to around 80 degrees.
Heat up your second mark and bend it almost all the way around to about 170 degrees as shown in the picture.
Step 3: Marking and Drilling
Mark:
Now we need to drill the holes. They need to be 30mm apart in the middle of the 70mm end of your turner.
Once you have marked these out, then pull out your centre punch and give them a little tap. Of course you can drill without a centre punch mark but it will make it a lot easier to seat the drill bit and stop the drill bit sliding around.
Drill:
Grab your safety glasses, 'cause flying metal shavings and corneas don't do well together. If you have a pedestal drill and drill vice - perfect! If not, clamp your wire turner in the vice and load up a 2.5mm drill bit in your drill... hold it as steady and straight as you can so as to not snap the bit.
Once you have drilled the holes, load in a larger drill bit (~5mm), and countersink the holes just a touch to remove the bur and make it easier for the wire to slide through without catching.
Step 4: Bending Your Tent Peg
So now you need to get angry and show this piece of metal that you can bend it without even heating it up!!
We need to bend the 5mm piece of metal around the wire turner - twice. Place your wire turner (that you just drilled) into the vice and tighten it nicely. If you are using an old tent peg, that's perfect because you already have a bend in the end which slips nicely into the vice, and then you can start wrapping it around the 6mm steel as shown. 5mm steel is not too hard to bend... but if you need help, a short section of pipe to sleeve over it will work great for leverage.
The 5mm steel needs to be wrapped around the 6mm steel twice, so that it won't have too much flex.
Step 5: Making the Notch and Unbending
Notch:
You need to make a notch in the end of your 5mm steel, which will ensure the wire loop doesn't slip out when tightening. This needs to be a rounded notch so it doesn't damage the wire loop. Put your 5mm steel in the vice and grab your hacksaw, cut a 1-2mm slot in the top IN THE SAME DIRECTION AS THE WIRE TURNER. Once this is done, you can widen the cut into a 'V' shape by sawing with your hacksaw on an angle.
Unbending:
Next, we need to unbend the end of the tent peg. This I did with a hammer and a piece of railroad track, but you can smack it straight on the back of the vice. Or, heat it up to red hot and unbend it.
Step 6: Putting It Together and Keeping It That Way
Keep it together:
Slide the 5mm steel onto the wire turner, then beat the end of the wire turner with a hammer till it starts widen. If you heat up the end it will flatten a bit easier, or you can just smack it cold. You just need to widen the end enough so the 5mm steel won't come off the end.
Step 7: How to Tighten It Up
Tightening it all up:
Cut 400mm of wire (that is less than 2.5mm diameter), and fold it in half.
Loop your wire around your hose, or handle, or whatever you want to fix... and pull the excess through the bend so as to tighten on to your hose like a slip knot - as in picture above.
The two free ends of the wire go through the two holes of the wire turner.
The 5mm steel notch slots into the bend of the wire.
Start turning the wire turner so that the tool eats up the slack wire, then re-position and turn till pretty tight.
Move the whole tool down over the bend, which tightens the wire a touch more.
Cut off the wire 10mm from the loop.
Bend sharp bits down into the hose for safety.
Step 8: What Next? Make Some Stuff!!
Fix axe handles; plumb air compressor and irrigation hoses; or make furniture lashed together with wire. I have seen small wooden barrels made with tightened wire instead of strapping.
If you have a unique use for this, I'd love to hear about it!!
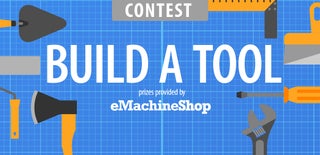
Participated in the
Build a Tool Contest 2017