Introduction: Wood Harpoon Drill
You want to make a calumet? A flute? A bagpipe? A blowgun? A didgeridoo?
You need to drill a very very long tunnel in a piece of wood?
You'll like this!
All you need:
- a flat wood drill bit
- a tube of aluminium or steel (with an inner diameter slightly bigger than the outer diameter of the extension of the drill bit)
- chemical anchor
- pliers
All you do:
- cut the tube to the size you want (mine's more than two feet!)
- put some chemical anchor in one end and on the bit
- slip the bit into the tube
- pince the end of the tube and push the bit a bit further
- let it solidify a few minutes
Now you've got the longest and cheapest wood drill bit ever!
Use: Make 'pumping' movements while drilling.
This allows you to evacuate the sawdust and avoid being stuck.
Use lots of natural oil to cool the drill bit.
I made a calumet with it and it worked just perfect!
Cheap, yak-proof, powerful, effective!
Enjoy!!!
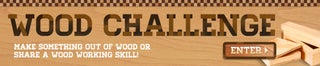
Participated in the
Woodworking Challenge