Introduction: Wooden Clock Designed With Tinkercad
Today, complex and intricate devices are used to define time and measure it. In the past, more simple ways were used to track the day and measure time. You most likely have heard of atomic clocks driving stock markets today, however, our ancestors used sundials, water clocks and mechanical clocks.
In this instructable, I will show you how i designed and built my clock with Tinkercad and a CNC mill.
If you didn't know, Tinkercad is a free, easy-to-use app to create 3D models and turn them into an actual product in a simple, fun and intuitive way. Create your Tinkercad account.
Grade level: 5-7
Science concepts:
- How does a pendulum's length affect its period.
- Gravitational acceleration and it's effect on the pendulum.
- Constructing an experimental setup.
Attachments
Step 1: Gather Your Materials.
Materials:
-1/4" (6mm) Plywood (2'X4') https://www.amazon.com/Premium-Baltic-Birch...
- 1/4" (6mm) Round dowel https://www.amazon.com/Dowel-Rod-Wood...
- 1/4" (6mm) Square dowel https://www.amazon.com/Woodpeckers...
- #10, 1/2" (12mm) Screw https://www.amazon.com/Best-Quality-Screw...
- #6, 1" (25mm) Screw https://www.amazon.com/Best-Quality-Screw...
- String https://www.amazon.com/Norpro-942-Cotton-Twine...
- Bottle https://www.amazon.com/Empty-PET-Plastic...
Tools:
- drill https://www.amazon.com/BLACK-DECKER-BDCDMT120C-20-...
- cnc mill https://www.amazon.com/Upgrade-3018-Engraver...
- 1/8" (3mm) endmill https://www.amazon.com/tool-home-Speed-Steel...
- Files https://www.amazon.com/Topec-Carbon-Steel...
- Sandpaper https://www.amazon.com/Sandpaper-Furniture...
Step 2: Designing a Gear.
It all starts by finding your desired shape. There are a few ways to do this, Basic Shapes and Shape Generators.
Basic Shapes are primitive shapes (Boxes, Cylinders, Spheres), these shapes can be combined with one another to create almost anything.
Shape Generators can allow you to create complex shapes faster. You can find springs, curved text and gears.
In >ALL >Shape Generators you can find the useful gear. Place a gear on the work plane. To change the properties of the gear, click on it in the pop-up we can change the pitch, height and number of teeth.
Some gears will require a spacer to function correctly. To make one, place a cylinder and cylinder hole. To resize you can click on the cylinder, then click the white square on one of the bottom of the cylinder and change its length and width. The white square at the top of the cylinder will change its height.
Using the align too, l align both parts to the center. Grouped both parts to combine them.
Step 3: Designing the Gear Train.
The gears will be 6mm,1/4'' thick because that is the thickness of the plywood used and have a bore of 6mm,1/4'' as that is the size of the dowel.
We need to calculate the gear ratio and direction. You can chose to do it by hand or use a gear calculator to do that for us.
Then we need to create the rest of the gears and form the gear train. The gear properties can be found in the photos above.
Step 4: Designing the Escapement and Pendulum.
Escape wheel
The escape wheel is made up of 5 duplicated boxes and 11 hole cylinders(10 at the side and 1 in the center).
The sides got 10 20mm, 25/32" dowels and the center got a 54mm, 2 1/8" dowel.
Upper pendulum
The upper pendulum consists of a cylinder with a slot at the top of the assembly and two arms that interact with the escape wheel and the latch. The arms are made with a cylinder and a box. Spacers on the top and bottom of the shaft keep it in the right position.
Pendulum bob
The pendulum bob is made up of 3 cylinders stacked together. The center cylinder has a slot in it to allow the pendulum shaft to slide and adjust its period.
Step 5: Designing the Frame
The base of the frame is a box stretched to fit the whole clock. The holes are made using hole cylinders that I duplicated from the gears.
The frame has tubes that fit the gears and boxes to connect the tubes together to form a cross bracing design. I did this so that the gears can be easily seen.
Step 6: Exporting the Parts for Cutting
We have finally finished designing our model!
You can check out my design and tweak it here: https://www.tinkercad.com/things/2Ri1n8pY8o6-clock
Move all other parts away place the part that we want to export on the workplane. Only parts on the workplane will get exported.
To export the model for CNC milling, click on the "Export", then ".svg".
Step 7: Cut Out Parts
Cutting out parts with a CNC mill.
I used a 3 mm, 1/8' endmill. You can use a smaller endmill, but not bigger than 3mm, 1/8' because the gears will not be cut properly.
Mount your stock onto the waste board. Use double sided tape on small parts and gears as tabs will be hard to clean up.
Some sanding will be required as there will be some blowout caused by the endmill.
There will be some parts that require right angled corners. As the CNC mill can't cut right angled corners, you will need to create them using needle files.
Cutting out parts by hand.
Download the cutting template. Cut out the template. Then, glue the template onto the wood. Cut out the wood using your saw of choice. File and sand the edges smooth.
Cutting out the clock hands.
The clock hands will be cut out of polypropylene. First, download and print the clock hands template. Cut out the template and paste it with glue to the polypropylene sheet. Using sharp scissors cut out the clock hands.
Now, time to assemble...
Attachments
Step 8: Assemble Parts
After about 3 hours all the parts are ready to be assembled.
All the gears are test fitted, then glued with some wood glue.
Most gears went smoothly... except the blue gear, its clutch bearing was too lose. I made the gap smaller in Tinkercad and milled it again. This time i made it slightly undersized so that i can sand it down to its final size.
Step 9: Calibrate the Pendulum
Now that the clock is assembled, you need to calibrate the pendulum for the clock to work efficiently. If you are lucky you would have gotten it exactly the first time.
First mount the clock to the wall or hold it on the edge of a table at 90°. This will decrease the inaccuracy of the pendulum.
Turn the escape wheel clockwise or attach the weight to the clutch and push the pendulum. The arms should lift the latch and catch the dowel of the escape wheel alternatively.
If this motion is inconsistent, change the angles of the arms and try again.
When the motion is consistent, insert a screw through the pendulum assembly to fix it in place.
Mount it to the wall if you have not.
Step 10: Final Assembly.
First, glue the supports onto the base with wood glue. Insert the gears into the base. Glue the top plate onto the supports.
With hot glue glue the clock hands onto the shafts.
Step 11: Its Finished!
Finally its done, it looks great and functions well. However if I were to do it again, I would 3d print the clutch bearing, it was extremely difficult to get it designed with the right tolerances on the CNC mill.
Share this project with your teacher friends to enlighten their students on physics phenomenons and mechanical devices!
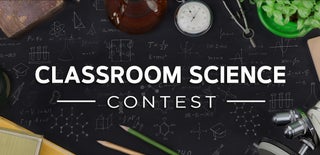
Participated in the
Classroom Science Contest