Introduction: 1$ DIY Cable Lug
The goal of this ible is to show you how to make a custom lug connectors for under a dollar. This is so cheap that you should be able to do this with leftover scraps from plumbing jobs.
Step 1: Material
You will need
- Pipe cutter
- Metal shears
- a hacksaw (or replace all three with a circular cutter)
- Pliers with a round opening
- Copper pipe of the size you need (more on this later)
- Pex vise crimper (for some reason Amazon only has a 160$ version of the tool I can get for 29$ at my local hardware store, so the link is for demonstrative purposes)
- Pex crimping copper rings for your pipe size
- Solder
- Soldering torch
- Hammer
- Tapered drill bit
- shrink tube (make sure you have some big enough ones)
Step 2: Figure Out Your Sizes
If you have cable sizing needs, then your connectors should match those requirements. Now resistance over distance is what matters, so if you are at a slightly lower gauge for the 1cm of your lug connector that happens to be thinner, don't worry too much. However, don't exaggerate, or that higher resistance point will become a fuse if you are wildly out of proportion.
First, use the wire gauge chart to figure out what
- the diameter of your wire (to know what size of pipe you need)
- the weight per foot, or surface area of the wire's face (depends on what calculations you prefer, surface area will be more accurate if there is a difference in the allow mixes; so err on the side of caution if you go by weight)
Next, use the pipe sizing chart to figure out (you are almost certainly using type M)
- look at the I.D of the pipes and figure out which one fits your cable size, with enough clearance to put in some extra layers as needed (see step 2)
- what the weight per foot is (to figure out how many layers of a given pipe are required to have the same weight per foot as the cable) or use the wall thickness and circumference to do a surface area calculation
For the record, for size 1 AWG, 2 layers of 1/2 or 3/8 pipe can be used, but 1/2 is easier to account for the layering necessary. This may take some trial and error for your other wires.
Step 3: Cut Your Pipe
First cut some short lengths of pipe (however long you want your lug + about an inch to go over the exposed wire). Add an extra half inch to this to account for hammering down. This will be your lug; cut a slit in it the length of your exposed wire if you are layering, just to make sure it goes on well.
Now cut some shorter pieces that will act as filler if there is too much of a difference between your pipe size and your wire. I needed 2 more inner layers to fill the gap. Make those the length of your exposed wire, and split them open on the length.
Step 4: Fit Your Copper Pipe
As you fit the filler pipes, use the pliers to crush and round out the layers. Once this is done, you may have to use the pex crimper on a smaller size than the rings you will be using, just to round out the copper, so that the rings will slip on.
Put on two rings, and crimp them. Once they are both well crimped, re-crimp the back one with a size too small.
Step 5: Cut and Flatten
Start by flattening the tip with a hammer, this will make it obvious where the wire ends. Where the wire ends(ish), cut a slit across the top of the lug. You can then flatten some more.
Step 6: Solder
Heat up your copper and shove some solder in there. The top slit also has the benefit of giving a good access to all layers and the wire, making sure that they can't just slip from one another.
You can also add a bit in the back, where you crimped harder there should be a small accessible lump. However, this will make the end of the cable a bit stiffer.
Step 7: Drill Drill Drill!
Make the hole the size you need it for your posts or bolts, and enjoy! You can also add a finishing touch by putting shrink tubing. What I like most about this is that I can colour code my cables so I know what's plugged where.
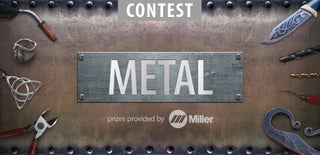
Participated in the
Metal Contest 2016
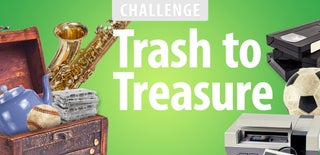
Participated in the
Trash to Treasure Challenge