Introduction: 2x4 Mega Bench
I decided to make this workbench out of 2x4's because I needed something stable and strong enough to take a lot of abuse. Also, for the cost, it's "cheaper" and stronger than just about anything you can buy.
In this instructable I'll direct the reader through a step-by-step process on how to replicate this project and even offer a few tips on how to save you a lot of time!
Step 1: Tool, Supplies, and Costs
Tools:
- Planer
- Miter Saw
- Circular Saw
- Drill
- Hand Planer
- Sander
- Hot Glue Gun
- Safety Gear
Supplies:
2x4's, 32 @ $2.78 ea.
Carriage Bolts, 8 @ $1.00 ea.
Rod Coupling Nuts, 8 @ $1.30 ea.
Rubber Furniture Cups, 8 @ $3.00
Pack of Hot Glue Sticks, 1 @ $6.00
Box of 2.5" Screws, 1 @ $15.00
Simpson Tie plates, 16 @ $0.60 ea.
Wood Varnish, 1 @ $16.00
Wood Glue, 1/3 gal @ $30.00 gal
Total Costs: $186.96
Time to complete project: about 8 working hours (2 days when accounting for drying time of glue)
***Note: Following a tip later in this instructable would cut this time in half***
Step 2: Safety First!
Whenever working with power tools, safety gear and protocols should always be strictly adhered to. I tend to learn things the hard way, but I'm sure you're smarter than that.
Step 3: Prepping the Wood
Take a little time to square up the sides of each 2x4 to help improve contact area for gluing in the next step. I suggest doing this for all 4 sides of the boards since most lumber has a fair amount of defects.
Step 4: Gluing
- Divide your boards in to even number groups.
- Each group should have the same crowning (bow in the same direction). Get them to be as uniform as possible.
- Once organized, begin applying a liberal amount of glue to the top surface of the first board then stacking the second on top of it. Repeat this process until the last board is stacked (no need for glue on the last board).
- Apply pipe clamps approximately every foot, alternating from top to bottom.
- Double check to make sure the boards are still aligned before fully tightening the clamps.
- Make sure each clamp is very tight by going back and re-tightening them several times following a pattern of starting in the middle and working outward.
- Allow 24 hours to dry
Repeat this step for each group
***TIP: Check your local lumber yard. Often times they have an industrial size planer you can use for a nominal fee. In my case, the local lumber store would run my boards through their 35" planer for only $15. I discovered this after the fact, but doing this would have saved a lot of time. I could have cut out the next 3 steps and had it all done in 1 with a perfect finish!!***
Step 5: Plane Each Section
Once the the glue has dried, run each section through the planer, both top and bottom.
Keep track of the final thickness of each section. They need to match each other by the end.
Note: You'll notice in my pictures that one section is shorter than the others. This was by accident from making 2 trips to home depot and not paying attention. I only realized my mistake after standing them next to each other in this picture.
Step 6: Glue the Sections Together
- Align the sections together in a way they fit best. Even after all the prep work there will likely be some bowing in each section. Match these as best as you can.
- Stand them on the side and apply glue to the surfaces that will connect. Glue only needs to be applied to one of the surfaces that connect together. Most of the glue gets squeezed out so there's no need to waste it.
- Secure good alignment between sections and apply the clamps in alternating top and bottom positions.
- Allow 24 hours to dry.
Step 7: Hand Plane the Imperfections
In the pictures you can see that, despite my best efforts, one section was still 1/8th of an inch off on each end.
A little love from a hand planer will smooth out these joints.
Do this for both sides.
Step 8: Sanding
The love from the planer is a little rough and tends to leave small grooves after each pass. Sanding with progressively finer grits starting with 80 and ending with 250 or so will clean these up nicely.
3 steps in sanding should be plenty and will produce a nice result.
Step 9: Trimming the Ends
Use a straight edge (level) and square to get a nice line to even out the ends of your bench top.
With a circular saw cut along the line.
Because my blade didn't have the depth needed, I had to repeat this process after flipping the table over.
Step 10: Building Support
I fastened a couple 2x4's together to make a base support to attach legs.
On the underside of the table align these supports and secure them down with some wood glue and a couple of wood clamps.
I used a Kregg jig to help seat in a few screws.
Step 11: Making Legs
By gluing together a couple of boards and securing them with some screws, I was able to build a few legs.
Note: The supports in the previous step was made this same way.
Step 12: Leg Footings
A board was placed on top of the supports and marked underneath to easily assure proper distances between legs.
The legs were then attached to the table using the Simpson Tie Plates. I found these to be very stable in holding the legs in position.
A 1.5" gap was left on the backside of the table to allow space for an additional support (shown in a later step).
Step 13: Cross Supports
Additional supports were added to give rigidity to the legs, front to back.
Step 14: Cross Beams
These supports were added to the back side of the legs to resist side-to-side motion.
I positioned the boards using clamps and marked off where the cuts needed to be made. It's a little faster and easier than measuring.
Step 15: Foot Holds
Under each leg was drilled a hole using a spade bit.
The proper depth needed can be marked off using a piece of tape on the bit.
The rod coupling nuts were then pushed into the holes. These will hold the feet.
Step 16: Make a Few Feet
With the bolts, furniture cups, and hot glue you'll make some leveling feet for the bench.
Follow this instructable HERE
I was surprised at how well these work. Hot glue doesn't seem strong enough but I'm very happy with the results.
Step 17: A Finished Look
I added a soft edge to the table using a palm router just for a little aesthetics.
Step 18: Varnish
I applied a couple coats of varnish to limit the amount of staining and help preserve the natural colors in the wood.
Let dry overnight and it'll be ready to go!
Step 19: Thanks for Reading!
I hope you enjoyed this project. I've put this workbench through a lot of abuse since then so it was worth it! Please feel free to comment and add suggestions for improvements, if needed.
I have many more projects on the way so please follow me if you want to see more. Thanks again!
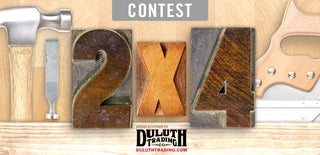
Participated in the
2x4 Contest
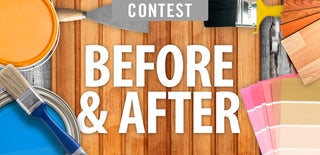
Participated in the
Before and After Contest 2016
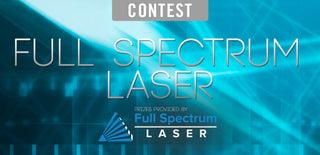
Participated in the
Full Spectrum Laser Contest 2016