Introduction: 3D Design As Tool for Jewellery Making
Designing something is typically associated with sketching. Most of the time, when making a new jewellery design, I also make sketches, in the most obvious form: a pen/pencil sketch on a piece of paper.
With all the current software available for making 3D designs, I started realising I could also use the technique to make jewellery designs. Being able to zoom, rotate, measure (and so much more) would enable me to explore shapes I otherwise wouldn't even consider using.
During the past year, I already got more experience with 3D designing when creating visualisations of university design projects. Because of this, I had already installed and started working with Fusion 360. One of the main things I focus on in my projects and designs is making the connection between classic forms of craftsmanship and new forms of technology. This project perfectly fits in that image, and I hope to be able to use this technique for future projects as well.
Step 1: Opening Up the Workspace
For this project, I used the Sculpt workspace in Fusion 360. When opening the program, you can find this option by looking at the "create" tab and going to the "create form" option. I personally feel like the Sculpt option gives a bit more freedom of working with and exploring shapes, which is exactly what's useful for jewellery design.
Step 2: Adding a Basic Shape
Under the "create" tab, you'll find a small list of basic shapes you can add to the workspace. Experiment, explore and simply try out things!
Step 3: Building Bridges
After adding a torus to the work area, I moved on to the "modify" tab.There's a ton of interesting options, and again I'd say go ahead and experiment! One option I really like is the "bridge" option, especially in combination with the torus shape. Because of this, I decided to keep exploring the specific option until finding the look I liked.
Step 4: Experimenting
Experimenting can be seen as the main theme of this entire project, but this entire step shows the intermediate results of messing around with the bridge option. When using the bridge option, you start by selecting the sides you want to build the bridge between. In the menu that pops up, two of the most important things you get to select are the number of twists and the number of faces.
Step 5: The Final Shape
For the final shape, I selected four faces on both sides to get the bridge part nicely in the middle of the torus.
Step 6: Making Adjustments
To slightly simplify the shape, I deleted a few of the lines on the twisted part. To do this, select the line and delete it.
Step 7: Changing the Shape
The basic torus shape is quite round, so I deleted the outer ring of lines. This makes the circle a bit flatter.
Step 8: Visual Style
Another useful feature when seeing 3D design as a tool, is the option to change the visual style. You can, for example, decide to only look at the outer lines. For me, this is something I still want to try out when soldering jewellery, since you can exactly see the lines needed, length and all.
Step 9: Colour Distinction
To get a proper view on the parts that need to be made, the "appearance" option can come in handy. To go to the menu, open the "modify" tab first. You can either change the appearance of the entire model at once, or make a selection of certain parts first. This way, I was able to get a good look at the way the shapes wrap around each other in the twisted part.
Step 10: Measuring
The measuring tool, found under the "inspect" tab, is really useful to get an idea of ratios in the design. Even without using the exact measurements, you can, for example, get an impression of how wide parts should be approximately.
Step 11: Inspecting Shapes
Another way to take a better look at parts of the design is to copy/paste it and move it next to the complete model.
Step 12: Switching to Wire
After making the shape and exploring it in all possible ways, it's time to move on to the wire! To start getting the basic shape down properly, I made two wire circles. This makes it possible to put the middle part between two layers, giving it the support it will need.
Step 13: Wrapping Time
For the twisted middle part, I used two wires joined by a piece of wirework. To keep the wires at equal distance from each other, a piece of reinforced cardboard can be used.
Step 14: A Few Centimeter Later
For the twisted part, approximately two centimeter should be enough, as measured in the model. Another important thing to take into account is to have the wrapped part in the middle.
Step 15: Twisting
With those two centimeters of wire wrapped, it's time to make the twist. Instead of trying to make the twist at once, gently try twisting it further a bit at the time.
Step 16: Making It Match I
Once the twist looks right, start shaping the remaining part of the wires.
Step 17: Making It Match II
WIth one of the wire circles next to it as reference, shape the wires to match part of the circle as good as possible The better the match, the easier it will be to add the twisted middle part to the wire circles.
Step 18: Final Preparations
Before joining everything together, cut off the wires as shown in the first picture to make sure there aren't any double wires left in the middle part. To make sure it fits, hold one of the sides between the circles and check if the other side still properly fits between the wires as well.
Step 19: Wrapping It Up
Holding the wires in the position described in the last step, start wrapping the part where the middle part sits between the two circles. Wrap a bit on the other side as well to prevent that side from not fitting later on. I decided to wrap the entire outer circle to give the pendant a complete look.
Step 20: Final Touches
After a bit of experimenting with the options of turning this pendant into a necklace, I ended up using 8-loops on two sides of the pendant, with the two ends of the lace knotted to them.
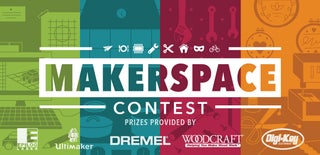
Participated in the
Makerspace Contest 2017