Introduction: 3D Printed Concrete Molding
I really like my 3D printer, but I’m not always a fan of the feeling of plastic. I love the rough, strong imperfections of concrete, so I’ve been exploring options to combine the prototyping abilities of 3D printing and the cost effectiveness of concrete. Here is my first instructable explaining how to make detailed, personalized concrete coasters for a very low cost (besides the cost of a 3D printer). I’ve used this to make much larger concrete pieces with the same detail, so size may not be too much of a limiting factor in 3D printed molds.
Step 1: What's Needed
- 3D Printer & filament
- Portland Cement
- Sand
- Concrete Dye (optional)
- Water
- Small scale
- Polyurethane
- Oil (vegetable or clean motor oil) OR other mold release
Note: I want to test other concrete mixes as well, like countertop mixes, but I haven’t gotten to it yet. Many countertop concrete mixes still use a fine grain sand, but they also use a superplasticizer, which makes the concrete mix much more fluid than normal while still retaining strength. This gives the surface fewer holes and requires less work to pack the concrete into the mold. I also want to try fiber reinforced concrete for added strength. Extra strength would be helpful for accidents.
Step 2: Design and Print
First, design the mold you want to print.
For this project, I chose the 4 elements from the popular show Avatar the Last Airbender. The mold will be done in two pieces to allow easy mold release. There will be an outer ring and an inner plate that fit into each other. See the pictures below. When designing this, make sure the gap between the two parts is sufficient so that the inner plate easily fits down into the outer ring (I made this gap .75mm on each side, or 1.5mm difference between the two diameters). The smaller the gap, the better.
The outer ring is pretty simple; give it a drafted angle (as shown in the picture) so that the concrete slides out very easily.
The inner plate is also very simple, besides the design you want on it. One thing to note here is that you also want to give the decoration a draft as well. I used a draft angle of 30 degrees to ensure that this plate won’t get stuck to the concrete.
Once these designs are made and checked, print them out! I try to watch my printing costs; these cost $0.17 and $0.34!
Step 3: Casting Prep
Molds:
Once the molds are printed out, you have the option of giving them a coating. I gave them a few coatings of polyurethane. I did this because the plastic I use, PLA, absorbs water very easily and becomes brittle. The first time I used PLA as a mold, it was so damaged that I had to peel the plastic off the concrete after it was done. So, Polyurethane is an attempt to waterproof the plastic. Other coatings may work better, but a coating of polyurethane will allow at least SOME re-casts.
Concrete Mixture:
This varies on the type of concrete you choose. I chose standard Portland Cement with a sand aggregate. The mixing ratio for this (per weight, not volume, so grab a small scale) is about 2 parts water to 5 parts Portland cement to 10 parts sand. For 4 coasters, you will need about 300 grams (10 oz) of Portland Cement, 120 grams (4 oz) of water, and about 600 grams (1 lb 4 oz) of sand. Weigh out these amounts and set aside for the next step.
Step 4: Casting
From here on out, gloves are nice.
Once any mold coatings are finished and dried, take a brush or spray bottle of oil and give the mold a decent layer so that all surfaces are wet with oil. However, be sure there are no big pools or puddles of oil on the casting.
Mix the concrete and sand well so it is evenly distributed. Remember, this is dusty, so ventilation and a dust mask is good. Then, mix the water in and stir very thoroughly until it is very consistent. The mixture is going to look very dry at first, but that’s okay.
You’ll want to fill each mold halfway for now and then massage and pack it into all the nooks and crannies. By the end of my time here, I’m basically slapping the top of the concrete into the mold. Then, fill the rest of the mold with concrete and pack/massage/slap it down. If you want to put felt or cork on the bottom side of the coaster, you don't need to smooth out the surface. I didn't want cork or felt here, so I took a little spatula and smoothed out the bottom. Don't worry about making it perfect, you can always sand this down later.
Then, lay a damp cloth over the molds and place the molds somewhere cool or in the shade. I’ve left my PLA molds out in the sun before and they warp in the heat very, very fast, but then again I live in Texas, so yeah.
Leave the castings alone for about 24 hrs, re-wetting the cloth if it gets dry. Then, you should be able to separate the mold by pressing up on the edges of the inner plate and down on the edges of the outer ring. Try not to press too much on the center of the inner plate, as this may break the still-setting concrete. Once the outer ring is removed, you should be able to lightly pry the inner plate off the concrete with a knife edge.
Once the casting is removed, place the damp cloth back over the concrete casting and clean and store your molds. You can then re-apply any kind of coating to the mold if it looks like it has scratches.
Step 5: Painting and Processing
Once the concrete is somewhat set, usually about 2 days after casting, I start painting it. With some lightly diluted acrylic paint, I paint the entire top surface, dabbing the brush into any bug holes that formed on the surface or in the grooves of the decorations. Let dry for at least 3 hours, then sand the top surface with some 220 grit (or any fine grit will do really) sandpaper. This gives the surface the concrete appearance again while leaving holes and grooves painted, resulting in a rustic look I very much like.
If you aren't putting felt or cork on the bottom, you should sand down the bottom side as well to get rid of any ridges.
After the paint dries, leave the finished product under a wet cloth for about a week after pouring. The longer it stays damp (up to about 2 weeks), the stronger the concrete will be.
Then, if desired, give the whole thing a coating of concrete sealing (you could also use polyurethane, but it's not as nice). Once the coating dries, cut out felt or cork board, attach to the bottom of the coaster, and done!
Step 6: Lessons Learned and Failures
I tried a lot of things to get this working well. I tried coating the mold in Plastidip to give it a very flexible, waterproof coating, but the plastidip would wear out and would start breaking and tearing after only one or two casts. I even tried the plastidip primer they offer which is supposed to form a stronger bond between the base and the plastidip, but to no avail. I think this primer is supposed to work only for metal.
I tried making this mold all in one piece and just fidgeting/shaking the concrete out, but this did not work. The PLA I used for the molds is just not flexible enough to do this. Other types of printing plastic, such as ninjaflex,could work better, but I am not going to start testing it for a while.
I tried casting concrete without a coating like polyurethane on the mold, but the concrete just tore it up. I think that the plastic mold actually absorbed the water and dissolved cement from the concrete and the concrete crystalline shape started forming in and around the plastic. It was so cracked and brittle, I basically just peeled off sections of the mold and scraped the rest off. I hadn’t tried it bare with an oil coating, but I don’t think that would last as long anyway. Of course, this may have also been due to some cheap plastic; it may work better with other manufacturers, I’m not sure.
I made some deeper grooves in my inner plate decoration (ridges higher than 0.8mm) and without the draft angles on them. They had problems with concrete getting broken off and stuck on the mold. The depth of the groove really doesn’t need to be deep at all since it gets painted, and the draft really helps in removal.
I also tried giving the inner plate and outer ring a really close fit, so they would basically snap in and no water would get through. This resulted in it being too difficult to remove the mold from the concrete and I broke the concrete piece trying to get it out. A small gap (1.5mm between the two diameters) works really well for me and only leaves a small seam on the part. This seam looks like a rough ring of concrete, but the paint sticks to it pretty well.
I used drylok etch to give the surface a rougher texture after it was done, but in the end, I didn’t like it. It turned out as rough as sidewalk concrete. This may desirable to some people, but I prefer the smoothness with the bugholes. If you try this process, remember that it's an acid bath so stay safe with gloves, goggles, ventilation, etc.
Step 7: Larger Castings
All in all, I've also used poly-coated 3D printed molds to make larger casts, including this Fallout Vault 101 door inspired bookend and this base for a Quantum Nuka Cola lamp, also from the Fallout series. I'd say I am happy with this experiment in cost effective 3D printing and concrete!
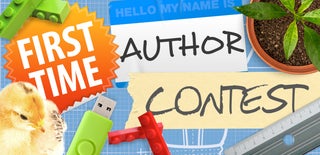
Participated in the
First Time Author Contest
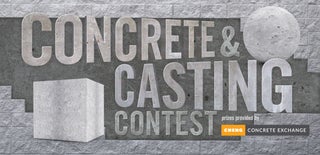
Participated in the
Concrete and Casting Contest