Introduction: A Solid Wood Gift Box
This Instructable will show you how I made a box for some special Christmas ornaments. The only improvement would be to be able to laser engrave something on the top. It could be a fancy design, a person's name, an image, a holiday greeting, or any other thing that you could imagine. That would be cool!
I hope you enjoy it.
Step 1: How It Began
Several years ago, we started a tradition of giving special Christmas ornaments to our kids and now to our grandkids. One would always recieve Santas, another would always get angels. Now the grandkids get a snowman, a nutcracker, an angel, or Santa. Last year I decided to do something a little different and make them myself. I had some round aluminum bar stock left over from another project and made some highly polished disks with the ornament design engraved on one side and a personal message on the other. Rather than just wrapping them up or putting them in a regular box, I wanted to do something special. This instructable will show you how I made the little boxes to put them in. The only problem in doing this is that next year they are expecting a more elaborate ornament and fancier box. I think I have created a monster.
Step 2: Decide on Your Wood
Your choice of wood will make a big difference in the appearance of your finished project. You want to use a piece that is thick enough to allow you to make the inside of the box deeper than the object you want to put in it. That sounds like a 'no brainer', but it would be pretty hard to put a 3" item in a 2" space. The next thing to consider is the type of wood. A cheap piece of wood will be more difficult to make it look good than a nice piece of hardwood, in most cases. You may have more finishing talents than I do, but I find it easier to start out with a quality piece. If your choice of wood is not thick enough, one option be to laminate pieces together using some wood glue and clamping them together. That would also give you the chance to use more than one type of wood and end up with some interesting combinations.
For this project, I had a piece of walnut that a friend gave me, (thanks Jerry). My little ornaments were 2" in diameter, so I wanted my box to be 3" x 3" and a little under 2" high. I cut this out on a table saw. Be sure to use safety glasses, a fence, and a push block.
Step 3: Sanding
This is the part that I never like. In order to get a nice smooth finish, you must sand - sand - and when you think you are finished, yep, sand some more. I started sanding with some 120 grit sandpaper and worked my way up to 600 grit in several steps. I did this with an orbital sander, but found that it was difficult to hold it and sand at the same time. I ended up clamping the block in a drill vice with some soft wood placed next to the block for protection.
The perforated board that you see underneath the block in the first picture is the top of a sanding box that I made out of mdf and connected my dust collector to it. The vacuum created by the dust collector will help keep the dust down in the shop, and will also help hold down the work piece. The little pegs also help. Hmmm, that sounds like another Instructable that needs to be done.
Step 4: Round Over the Edges
Now that you have a nice square block cut and sanded, you should smooth off the edges. I used the router table for this step. A 3/16" roundover bit was used on the bottom and side edges. A 1/2" roundover bit was used on the top. If you don't have a router, you could use sandpaper just to smooth the edges out a little and eliminate the sharp corners.
Step 5: Cut the Block in Half
You should now have a nice smooth block with no sharp edges. I hope you made the box big enough to allow for a top piece to be cut off. As you can see, my block had a knot hole in it. I wanted to make a cut on one side of it, but instead, the cut went right down the middle of the knot. So things did not go as planned. It ended up being a 'UEDC'. We have all made some. A UEDC is an 'unintended engineering design change', in other words -- a mistake. So, we'll just say that it adds character to the box.
For this step, I used the bandsaw to keep the kerf as narrow as possible. This would help the grain pattern match up on the sides of the box.
Bandsaws usually will not cut straight -- even with a new blade. To correct for this, I made a 6" cut along a straight line drawn parallel to the edge of a test piece of wood which was about the same thickness as my box and about 12" long. Sure enough, I had to angle the board to keep the cut on the line or the cut would drift off to one side. Leaving the test board on the bandsaw table at that angle with the blade still in the cut, I clamped my fence to the table parallel to the edge of the board. This is the angle that the blade wants to cut. Using the fence set at this angle, the cut came out very straight.
Step 6: To Hinge -- or Not to Hinge
I was unable to find some small hinges that looked good, so I tried something different. I decided to use magnets to keep the top closed, but I did not want them to show. The little 5/16" diameter round neodymium magnets are 1/8" thick. I cut a 1/8" groove all around the top and bottom sections of the block. I wanted to get the magnets as close as I could to each other without risking cracking the edges. A slot cutter was used on the router table to do this.
Step 7: Make Recesses for the Magnets
The slot cutter did not cut deep enough for the magnets to rest in, so a 516" deep and 5/16" long recess was cut in the bottom of the grooves in each corner of the top and bottom pieces.I used a 1/8" dia. endmill for this. Each half of the block was put in a drill press vice which was clamped to the mill table. The endmill was carefully positioned so that it would not cut into the sides of the grooves. These recesses allowed the little magnets to stay positioned without sliding around.
Step 8: Make Some Filler Strips
In order to keep the magnets in place and to hide them, I used some 1/8" thick red oak that was cut into strips a little wider than my slot and a little longer than the width of the block. That would give me some extra material when I do my finish sanding. These strips will hide the magnets and hold them in place and will look like an accent piece.
The little neodymium magnets were paired up with the north and south ends mating together. You have to do this so the magnets will attract each other. If you don't do this, you might have a box top that wants to open, not close. Match up 4 pairs of magnets and put them in the recesses. Double check that the magnets are oriented correctly, because after this step you will not be able to get to them. You can see the magnets in their little recesses in the third picture in the previous step.
Put a small amount of wood glue in two slots on opposite ends of the top and bottom pieces of the box. Push the strips into these slots and let the glue harden. Before it does harden, clean any excess glue out of the other two slots that may have squeezed out when you pushed the strips in place. The ends will be sticking out a little, but don't worry about this now. After the glue sets, trim the remaining strips off so they will fit into the other two slots and glue them in place like the others.
Step 9: More Sanding
After the glue has dried, the strips need to be trimmed. This was done with a disk sander, but could have been done with utility knife, regular sandpaper, a saw, or several other methods. After you trim them off, the strips should be sanded flush with the sides of the blocks. This will leave you with nice smooth sides on your box.
Step 10: Cut a Cavity for the Ornament
Depending on what you will be putting in the box, cut a cavity to the required depth. I used a frostner bit to cut a hole 2-1/4" diameter and 1/4" deep. Use some padding in the vice, so you won't scratch up your fresh sanding job.
Step 11: Finish Your Project
I did not want the aluminum disk to get scratched, so I glued some scrap felt to the bottom and sides of the cavity. You can finish the wood with your favorite polish, paint, varnish, oil, or any other finish you like. I used some furniture polish and then buffed it out with a micro fiber towel.
I think that this little box turned out better than I thought it would, and will use the magnet idea in future projects.
Thanks for looking at my box.
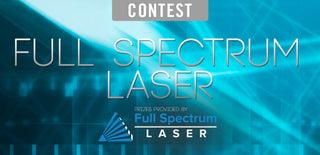
Participated in the
Full Spectrum Laser Contest 2016
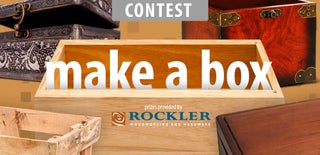
Participated in the
Make a Box Contest