Introduction: A Spherical Flying Machine With No Control Surfaces
This our entry for a local flying machine design competition. For the competition, we were tasked with designing and building a flying machine that can be described as 'unconventional'. Being hardcore fans of many science fiction shows ourselves, we immediately drew our inspiration from the mapping drones in Prometheus, Kinos in Stargate Universe, IT-O Interrogator drones in Star Wars, and many many other movies to unanimously decide on building ourselves a spherical shape drone.
Our first task was to find our what has been done along this line of spherical flying drones. The most notable examples we found were the spherical flight vehicle by Japan's defense ministry and the Gimball by EPFL's LIS group. There were also a multitude of coaxial counter rotating rotors rc toys with a spherical cage mounted on the outside. Our first thoughts regarding these drones were that their design, although ingenious, may have the issue of the main airflow going through the body of the aircraft, drastically reducing the available spaces on which payloads can be mounted. Now our main focus is to try to come up with a way that eliminates this issue.
Step 1: Step 1: Conceptualization and Design
We decided to go the way of a coaxial counter rotating rotors setup for our propulsion. This setup allows us to control the yaw of the aircraft by adjusting the differential rotation speed of the propellers. In order restrict the body of the airflow to the centre of the aircraft, we design a shrouded propeller system as the air intake. At the bottom of the air intake, the airflow is split into four output ducts that direct airflow to the side of the sphere. The shape of the output ducts were shaped such that they conforms to the spherical geometry of a sphere.
For the attitude control, we want to do away with the conventional control surfaces that is the hallmark of most flying machines. We thought to ourselves, why not use the whole propulsion assembly for this purpose? The solution we came up with is this: The propulsion system is mounted within a spherical cage. Right below we mount an x-y translation stage meant to carry the heaviest component in the drone, the batteries. Thus when the center of gravity (c.g.) of the battery is in line with the line of thrust, the aircraft is in vertical flight or hover. When the battery is shifted in one direction, the c.g. of the aircraft is shifted, and thus the whole aircraft will re-orientate, directing thrust in the opposite direction. This sort of c.g. steering can be found in hang gliders and small one man helicopters.
Midway through our design phase, we found a similar design has already been implemented in the Department of Electrical and Computer Engineering in University of Toronto as a Master Thesis research. Although for their case the propellers are not shrouded.
We also dapple a bit into the electronics trying to use a 10 degrees of freedom IMU (AltIMU 10) for stabilization, but that was stopped halfway given the time constraint of the deadline for the competition.
Attachments
Step 2: Step 2: Fabrication
The cage of the sphere drone was laser cut out of paper laminated foam. Unfortunately we did not anticipate the 0.2mm precision of the laser cutter. The parts do fit together but not as tight as we had hoped. The air intake duct, airflow separator and output ducts were 3d printed using ABS. As the support settings were far from optimized, removing the support structures from inside the ducts were a nightmare. The xy translation stage was also printed in ABS. Significant filing was done before the stages ran smoothly with the help of some grease.
Step 3: Setp 3: Assembly and Testing
Additional processing was done to the spherical cage by means of spray-on lacquer. The air duct was fasten together by means of M3 screws and nuts. Using the same screws and nuts, the air duct assembly was bolted into the middle plate and the cage assembled around it. Lastly all the vertical ribs was installed and fastened using a cable tie that ran along the equator of the sphere.
Additional rc parts needed:
From Hobbyking:
1. CR23L Contra Rotating BL System1100kv x1
2. F-30A/15205 Hobby King 30A ESC 3A UBEC x2
3. Counter Rotating Three Blade 5x4.5 Propeller -Black x1
From our stash
1. S3003 Futaba servo x 2
2. 9CHP Futaba 9 channel transmitter
3. R156F Futaba 6 Channel reciever
4. Alight High-Power LiPo 12C 11.1V 1800mAh battery x1
The video that we made for the competition which simulated the assembly can be found here:
Probably the rc electronics connection can be easily found online. There was also some mixing of the yaw and throttle channel of each motor to effect the differential rotation speed. Unfortunately, when we powered up the electronics it became clear that the trust was grossly inadequate for the 1kg or so weight of the drone. The main issue was that the constriction of the airflow imposed by the airduct. Air was just escaping through the gaps between the blades of the propellers. So we designed and and printed fan blades similar to those found in compressors instead. In the final hours before the deadline of the competition we tested the drone with the fan blades installed. We bumped the voltage up to 14.8V (4S) using a dc power supply and conduced our test. Alas that proved to be too much for the small motor to take and it burnt out. Well given the 1.5 weeks build schedule from conceptualization to final build with no initial calculation of the generated thrust, we were not really hopeful for a successful flight. For our efforts which so brilliantly went south we were awarded the most innovative design, for a aircraft that did not manage to fly, apart from one of the top compressor blade taking off because we did not secure it tightly... Back to the drawing board.

Second Prize in the
Move It
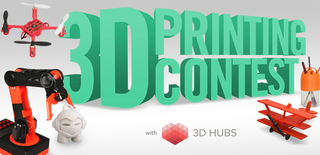
Participated in the
3D Printing Contest
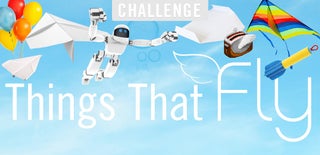
Participated in the
Things That Fly Challenge