Introduction: Adirondack Beach Chair W/ 2 Positions
I have always wanted to make my own camping chairs. I started out with a Kentucky Stick Chair, which was cheap to build and surprisingly comfortable, but not very elegant. After years of searching, I found the answer in these two-piece beach chairs in the classic Adirondack style. I purchased the plans from Phil Barley off of Etsy here and proceeded to read and reread the plans as I'm wont to do when tackling a new project.
The plans were exceedingly well written, documented, etc. and I've purchased plans from various professional woodworking magazines. After poring over them, I realized that I had a real challenge. All of my "real" woodworking tools were in storage. I needed to make a pair of these without access to my table saw, drill press, etc. and only had access to the tools I had in my small apartment storage closet. Challenge accepted!
If you like this Instructable, please vote for me in the Hand Tools Only Contest 2016:
Step 1: Templates
The first step was to print out the downloaded PDF, which is a 24" wide document. I called my local Kinko's and they could do it for about $6. Sold!
Then, I used some spray adhesive to attach the full-sized template to some 1/4" masonite from Home Depot, which cost about $6. All right!
Without my bandsaw, I had to fall back on my old friend, the Japanese pull saw that I used to build my son's boat. It could handle the curves of the templates and allow me to get close to the lines, which I could then sweeten up with a file or hand sander. It took a few hours, but I was able to cut out all the template parts. The only part with no template was the rectangular seat slat. I took my time to cut the templates out perfectly because I was envisioning the possibility of using these as a router template for future chairs.
The next step was to start cutting out chair parts. Since I had waited so long to find these plans and I was going to build them by hand, I wanted them to last, so I chose to use oak. Without my more advanced woodworking tools, I had to rely on S4S red oak from Home Depot for about $5 per board foot. Expensive, but I felt it would be worth it in the long run. Without being able to nest the template parts in the aisle at the store, I bought $100 worth of oak boards that were wide enough for the back and leg parts that have a pretty decent curve to them, meaning I had to buy 8" wide boards. For the slats, I was able to go with 3.5" wide boards. The plans also call for 1" dowel ($5) and the accompanying 1" forstener bit ($11) chucked up in a hand drill. A hole saw would accomplish much the same thing, but the holes aren't quite as exact or a smooth. I made sure to use a backer board to avoid tear out on the back side.
Once I had them home, I dropped the tailgate on my truck and laid out the templates on the boards, trying to optimize efficient use of the expensive wood. I used a mechanical pencil which leaves a sharp line as my guide. The first thing I noticed was that the 1" notch the dowel clicks into was really close to the edge. The best way to drill this would be before I cut the parts out so that the center brad point would have some wood to bite into to establish the hole. I then shot Phil a little note suggesting that this tip might be included in the plans.
Using the fine toothed side of my pull saw, I proceeded to cut out all of the parts from the oak. I made sure to line up every straight edge on the template with the straight edge of the wood to save the number of straight cuts I'd have to do by hand. The width of the blade makes it easy to sight down to ensure square sides. That took several hours across two days. Whew!
Step 2: Bones
While I had the forstener bit chucked up, it was time to drill the 1/4" deep holes in the leg and back parts. This is a bit hit a miss and affects the final fit of the chair. I was using waterproof glue (Titebond III) and glue is always dependent on surface area. Once the holes were drilled, it was time to cut the dowels. It's a bit tricky to cut the dowels square, so wrap a piece of masking tape around the dowel at the mark. If it overlaps, then you have a square cut. The pull saw does a great job on this step too. I was even able to hold the dowel by hand with no vice needed. Before you proceed to any assembly, make sure to sand all the parts and ease the edges. I used a hand sanding block, but a 5" random orbital sander will work just fine. If you really want to take your build up a notch, use a small round over bit on a router.
Now it was time for the first sub assemblies. The dowels get screwed and glued into their respective back and leg parts with the understanding that the leg half fits inside the back half. I deviated from the plans and just used drywall screws to hold the parts together while the glue dried. I was planning on countersinking all screws and plugging them with oak for a more finished look. More on that later. Make sure you hold your sub-assemblies up against a wall or on a flat floor to make sure all four corners touch before the glue dries. This is important so the chair sits flat. You also need to measure diagonally across all four corners to make sure opposing dimensions match to ensure the chair is square. Once you're happy with the above, set aside to dry for at least four hours.
Hint: If you're in a hurry to build a chair, only cut out the back and leg parts, do the glue up, then start to cut out the back and seat slats while the glue is drying on the sub-assemblies.
Before the two sub-assemblies become structural, there are a few parts that you need to install. First, the forward slat on the seat opposes the dowels. Cut that to size, center, the fasten in place. Once again, I countersunk, screwed and glued to eliminate that unpleasant squeaking chairs sometimes have that undermine your confidence in them.
Next is a spacer to hold the top of the back at the correct distance so you can install the curved back spacer. Once again, screwed and glued. The trickiest part of this step is fitting the bottom spacer for the back. It has to fit inside the back uprights and tilt at the correct angle to accept the back slats. I used a back slat to get the proper alignment then permanently fixed in place using the method described above.
You can now slide the leg assembly into the back assembly and see the bones of your new chair for the first time!
The plans call for some furniture screws to hold the legs and dowels together. Knowing the strength of Titebond III, I drilled a deep 1/4" hole, slathered a bunch of glue onto some 1/4" oak dowel, drove it home and sanded it flush. Like the plugged screw holes, it disappears almost completely after the finish is applied.
Step 3: Back
Now on to the back slats. Find the centerline of the top and bottom back spacers. Locate the center slat so that the bottom edge is just flush with the bottom of the 1" dowel. This is important so that the chair assembles easily. Once I had the center slat located, it was a simple matter to repeat the process for the symmetrical slats on either side. The directions called for a 1/4" space between the slats and I had used 1/4" masonite to make my templates, so I was able to use a scrap as a spacer.
The two outside slats need a notch cut into them so they sit flat on the spacers. I held them in place and traced the notch. Then using the pull saw at an angle, cut the notches. They're not especially pretty, but nobody will see them.
Once again, all parts were countersunk, screwed and glued...
Step 4: Seat
I already had the first slat in place, so it was a simple matter to add the other six slats in place using the 1/4" spacer. You have to eyeball the spacing on the curve a bit since the 1/4" rule doesn't really apply there. Once you get to the last curved part of the seat, you'll need to trim it to fit to capture the back slat ends. This is another really cool part of the design. I also beveled the back edge to fit up flush against the back slats. If you're careful, you can get a really nice fit.
Step 5: Plugging Screw Holes
Since I knew I was going to be plugging my screw holes, I bought a plug cutter specifically for hand drills (3/8" for the size screws I was using), so they have a self-centering, spring loaded spur. Most of them are for drill presses and impossible to use in a drill.
I then cut a bunch of plugs out of scrap wood, dab some glue into the hole, align the grain of the plug with the grain of the chair part, then gingerly drive the plug home and sand flush. I used to use a flush cut saw to cut the plugs flush, then sand them but not only is it an extra step, but I found the saw usually damages the wood, which you have to then sand out anyway.
Step 6: Irony and a Fix
It's more than a little ironic that I had to make these chairs with hand tools from the tailgate of my work truck, considering I have a semi-professional wood shop's worth of tools in storage, but the end result was worth it.
Now, just in case you glue up the back and leg sub-assemblies and you find that the legs don't fit into the back, don't sweat it. Worst case scenario is you have to buy some more dowel. This happened to me on one of my chairs, hence the fix.
Remove any screws holding the dowels in place and cut the dowels on the leg sub-assembly on one side only. Take your forstener bit and hog out the end of the dowel to the 1/4" depth. Be careful because the end grain will drill differently than the face. Dry fit the end of the dowel into the hole, using a screw to draw it up tight. Check the fit to see if the legs now fit into the back. If it fits, then glue it up and you're back in business.
On mine, I now had way too much of a gap, so I cut off the other end of the dowel, repeated the process and cut a new length of dowel so that the legs fit into the back perfectly.
Step 7: Finish
Discussing the finish for an outdoor chair is almost on par with mentioning religion or politics at a dinner party. Some will swear on oil, some varnish, some paint, and a lot of options in between. I think a lot depends on its intended use. If this is on a protected porch/patio, then you don't have to worry so much about UV and that opens up a lot of options. I intend on using these on the beach, half submerged, so I'll be using penetrating epoxy to soak into the wood, basically making it a wood grained piece of plastic, with a UV protection top coat (epoxy has no built in UV protection, even though it's super hard and durable). That will let the wood age naturally into that classic gray color of driftwood on the beach, but never rot.
If I had planned on exclusively using these on our covered porch (they're actually replacing our expensive and uncomfortable teak furniture), then I'd probably go with a Watco Dark Walnut Danish Oil. It's a one-step process that polymerizes/dries/cures into a durable finish that's just the right color.
Almost all of the products mentioned above can be applied with cheap, throw-away foam brushes, so the beginner need not worry too much about this step.
Of course, when building anything like this, in some ways it's much easier to sand and finish all of the parts before assembly. That way you don't have to sneak in between parts or into corners. However, unless you have significant real estate to lay these parts all out flat while one side is drying, then flip the next day and do the other side, finishing the assembled chair halves is much easier.
Step 8: Wrap Up
The design of this chair is really ingenious. In the full upright and locked position, it's a very comfortable chair for reading or sitting around the campfire. In the reclined position, it's very comfortable for a nap, to watch the clouds go by or gaze at the stars. Thanks Phil!
My plan for future chairs is to be able to cut out all the parts with a CNC machine. I took one chair into work just to show the guys what I did over the weekend and got orders for six more chairs!
As I've said before, I was extremely happy with the plans as purchased. Most of the deviations I made to the plans were either personal preference choices, tools at hand or processes that I had successfully done on previous projects. Another suggestion I made to Phil was to label the parts as to how many of each template to make. When you're looking at that pile of templates for the first time, it's difficult to envision how many of each to make and it's too much work/expensive to make more than you need or think you're ready for a sub-assembly and discover you are missing a part. Oh, I did mention that it would be nice to locate the centers of all the 1" dowel circles on the templates too.
Assembly and reclining takes literally about 3 seconds. The way the seat is designed, it locks against the back and positively locates the dowel in the notch. These chairs are so comfortable that when I brought them upstairs, I carried them into the living room and we watched a movie while sitting in them envisioning toasting marshmallows.
Stay tuned for the CNC version of this exact same project, which is why I entered the contest. First prize is an X-Carve from Inventables!
Step 9: Adding a Little Embellishment - Beach Style
So the little lady was so happy with the his & hers chairs that I decided to add a little embellishment to them. She's all into Hawaii and since these are beach chairs, I thought a hibiscus and honu were in order.
I did this by hand with a Dremel tool and a 1/16" burr bit, but this is definitely something that the X-Carve would excel at. Hint, hint...
First step is to print out some clipart of the design that's the correct size to fit on the center back upright piece toward the top. Then I used some spray adhesive to stick the printed design to the wood. Taking the Dremel tool, I carefully carved out the design, making sure to keep the direction the bit spins in mind at all times. I originally was going to do a black epoxy treatment, but the designs are so small, I was worried that the thick epoxy wouldn't settle down into the crevices. So, I painted it with acrylic paint instead and had much better control over the detail. The entire chair is going to get coated with epoxy to make it waterproof, so the paint will be encapsulated beneath the epoxy anyway.
Note, this would have been considerably easier to do before assembly. Regardless, end result, the wife's even happier!
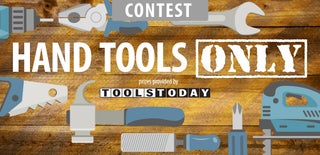
Participated in the
Hand Tools Only Contest 2016