Introduction: All You Need to Know About a Relays
What is a Relay?
A relay is an electrically operated switch. Many relays use an electromagnet to mechanically operate a switch, but other operating principles are also used, such as solid-state relays. Relays are used where it is necessary to control a circuit by a low-power signal (with complete electrical isolation between control and controlled circuits), or where several circuits must be controlled by one signal.
- Relay Module - AliExpress
Step 1: Parts & Design of a Relay
IMAGE:
- Relay inside its Plastic Case.
- Relay separated from its case using a screwdriver.
- Parts of the Relay.
- Relay Leads which can be soldered to a PCB
- Parts of the Relay
Start by removing the Plastic or PVC case of the relay by using a screwdriver. You can see the design and various parts of the relay. The main parts of the relay are: Armature, Spring, Yoke, Contacts & Coil.
A simple electromagnetic relay consists of a coil of wire wrapped around a soft iron core, an iron yoke which provides a low reluctance path for magnetic flux, a movable iron armature, and one or more sets of contacts (there are two in the relay pictured). The armature is hinged to the yoke and mechanically linked to one or more sets of moving contacts. It is held in place by a spring so that when the relay is de-energized there is an air gap in the magnetic circuit. In this condition, one of the two sets of contacts in the relay pictured is closed, and the other set is open. Other relays may have more or fewer sets of contacts depending on their function. The relay in the picture also has a wire connecting the armature to the yoke. This ensures continuity of the circuit between the moving contacts on the armature, and the circuit track on the printed circuit board (PCB) via the yoke, which is soldered to the PCB.
Step 2: Working of a Relay
IMAGE:
- Armature & Insulated Coil of Relay.
- Relay without Insulated Coil.
- Contacts Of the Relay when No current is Applied across the terminals of the relay.
- Contacts Of the Relay when Current is Applied across the terminals of the relay.
- Spring of the Relay.
A simple electromagnetic relay consists of a coil of wire wrapped around a soft iron core, an iron yoke which provides a low reluctance path for magnetic flux, a movable iron armature, and one or more sets of contacts (there are two in the relay pictured). The armature is hinged to the yoke and mechanically linked to one or more sets of moving contacts. It is held in place by a spring so that when the relay is de-energized there is an air gap in the magnetic circuit. In this condition, one of the two sets of contacts in the relay pictured is closed, and the other set is open. Other relays may have more or fewer sets of contacts depending on their function. The relay in the picture also has a wire connecting the armature to the yoke. This ensures continuity of the circuit between the moving contacts on the armature, and the circuit track on the printed circuit board (PCB) via the yoke, which is soldered to the PCB.
When an electric current is passed through the coil it generates a magnetic field that activates the armature, and the consequent movement of the movable contact(s) either makes or breaks (depending upon construction) a connection with a fixed contact. If the set of contacts was closed when the relay was de-energized, then the movement opens the contacts and breaks the connection, and vice versa if the contacts were open. When the current to the coil is switched off, the armature is returned by a force, approximately half as strong as the magnetic force, to its relaxed position. Usually this force is provided by a spring, but gravity is also used commonly in industrial motor starters. Most relays are manufactured to operate quickly. In a low-voltage application this reduces noise; in a high voltage or current application it reduces arcing. When the coil is energized with direct current, a diode is often placed across the coil to dissipate the energy from the collapsing magnetic field at deactivation, which would otherwise generate a voltage spike dangerous to semiconductor circuit components. Some automotive relays include a diode inside the relay case. For instance when a relay switches in your car the voltage spike can cause interference on the radio, and if you have a faulty battery or are silly enough to disconnect it with the engine running it can damage the ECU etc.
Step 3: Pole & Throw of a Relay
IMAGE: 1. Circuit symbols of relays. (C denotes the common terminal in SPDT and DPDT types.)
Since relays are switches, the terminology applied to switches is also applied to relays; a relay switches one or more poles, each of whose contacts can bethrown by energizing the coil in one of three ways:
Normally-open (NO) contacts connect the circuit when the relay is activated; the circuit is disconnected when the relay is inactive. It is also called Form A contact or "make" contact. NO contacts may also be distinguished as "early-make" or NOEM, which means that the contacts close before the button or switch is fully engaged.
Normally-closed (NC) contacts disconnect the circuit when the relay is activated; the circuit is connected when the relay is inactive. It is also called Form B contact or "break" contact. NC contacts may also be distinguished as "late-break" or NCLB, which means that the contacts stay closed until the button or switch is fully disengaged.
Change-over (CO), or double-throw (DT), contacts control two circuits: one normally-open contact and one normally-closed contact with a common terminal. It is also called a Form C contact or "transfer" contact ("break before make"). If this type of contact utilizes a "make before break" functionality, then it is called a Form D contact.
The following designations are commonly encountered:
SPST – Single Pole Single Throw. These have two terminals which can be connected or disconnected. Including two for the coil, such a relay has four terminals in total. It is ambiguous whether the pole is normally open or normally closed. The terminology "SPNO" and "SPNC" is sometimes used to resolve the ambiguity.
SPDT – Single Pole Double Throw. A common terminal connects to either of two others. Including two for the coil, such a relay has five terminals in total.
DPST – Double Pole Single Throw. These have two pairs of terminals. Equivalent to two SPST switches or relays actuated by a single coil. Including two for the coil, such a relay has six terminals in total. The poles may be Form A or Form B (or one of each).
DPDT – Double Pole Double Throw. These have two rows of change-over terminals. Equivalent to two SPDT switches or relays actuated by a single coil. Such a relay has eight terminals, including the coil.
Step 4: Change-over (CO) or Double-throw (DT) Relay
A Change Over type relay is much like a Single Pole Double Throw( SPDT) relay.
Inorder to explain the working of a Change Over Relay, I have compared it to a SPDT relay.
A SPDT relay configuration switches one common pole to two other poles, flipping between them. Consider a SPDT relay with a common pole 'C' and let the other two poles be 'A' and 'B' respectively. When the coil is not powered(inactive), the common pole' C' is connected to the pole 'A'(NC) and is in resting position. But when the relay is powered(active) the common pole 'C' is connected to pole 'B'(NO) and isn't in resting position. Hence only one position is resting position while the other position needs the coil to be powered.
Step 5: Voltage & Current Parameters of a Relay
IMAGE: 1. Voltage & Current Parameters of the relay in-scripted on the Case of the relay.
2. Voltage & Current Parameters of the relay in-scripted on the Case of the relay.
Most relays are available in different operating voltages like 5V, 6V, 12V, 24V, etc. If the required operating voltage is supplied to the relay, the relay is activated. The operating voltage of a relay is generally in DC.Small signal relays and low voltage power relays are usually in DC, but mains control relays and contactors quite frequently have AC coils.The rest of the terminals of a relay are used to connect either a AC(generally 50/60Hz) or DC circuit. The switching and contact pins of the relay have their respective Maximum voltage and current ratings/Parameters. These Parameters are generally in-scripted on the plastic or PVC case of the relay.On the contact ratings, they will frequently have something like 5A@250VAC / 10A@12VDC. These are the figures you have to be within. Having said that you can run a higher current than stamped on it if your voltage is lower, they aren't directionally proportional though and the datasheet for the relay should be consulted. If a relay is overloaded, it can burn out and damage the circuit or appliances connected to it. Be sure to choose a relay that can handle your voltage and current requirements to ensure the relay coil doesn't burn out and your circuit doesn't get damaged.
Step 6: RECYCLE AND REUSE OLD RELAYS
- Relays Can be desoldered from any old or exisiting circuit and can be re-soldered/ Soldered back on any new circuit or project since relays do not get burnt by excessive soldering.
2. The Windings of the coil can be reused as Jumper wire in Various Circuits.
3. The contacts and Screws, Nuts, Bolts, Washers of the relay can also be reused.
If you like this instructable feel free to vote for it. Follow me on instructables so you can get updates to any of my other instructables. Post queries and questions in the comments section below and I will certainly answer all of them. Thanks for reading.

Participated in the
Gadget Hacking and Accessories Contest
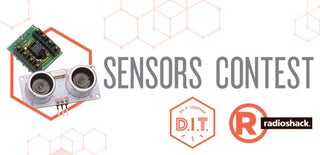
Participated in the
Sensors Contest
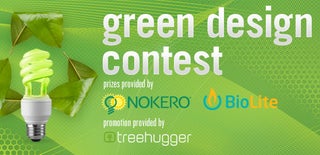
Participated in the
Green Design Contest
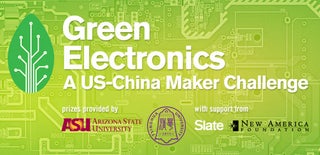
Participated in the
Green Electronics Challenge