Introduction: Ammonite (power Carving)
I have always loved the shape, texture and form of ammonite fossils. A spiral is always a satisfying shape that leads the eye well. The texture runs opposing to this but adds more intrigue to the form. Its just a perfect piece to carve.
I finally got motivated to do this project with the pocket sized instructable comp. It was always a great use of scraps. Hopefully you can learn something about powercarving or shaping spirals.
Step 1: Preparing the Timber and Drawing the Pattern
The timber I use is an off cut form a jarrah platter. I knew I kept those piece for a reason. Piece is 64mm wide and 33mm thick.
Drawing a good spiral is the challenging thing. The key is finding a ratio that works. Normally I stick to the Fibonacci sequence. With this one I struggled to found a ratio that worked. Instead of reducing the semi circles by the ratios, I reduced the widths at each half circle by 75%.
Start with a center line that is off center. That way you make the most of the blank. I found the position of the line by trial and error. I then marked my largest semi circle. I wanted my opening to be a 20mm diameter so my second semicircle had to be 20mm smaller, therefore I reduced the radius by 10mm. Working to the center line, i repeated this pattern. My reduced measurements were 20- 15- 12- 8- 6- 4.5.
Step 2: Cutting the Shape
After drawing my spiral, I reduced the thickness of the blank by cutting it on the band saw. This was done at 20mm to match the spirals opening. Important to do this first before cutting the shape because of the flat surface. Basic band saw safety.
The first cut I made was the one straight cut so I could pull out the blade safely. On a curved cut its easier to bind when pulling out of a small cut. As the rest of it is a tight curve, my band saw blade couldnt make the cut in one go, so I made lots of smaller cuts to get the shape.
Step 3: Start the Shaping on the Disc Sander
I started with sanding the back flat to remove the band saw marks. Next step was to sand the outer edge to refine the shape to my pencil line. This was done with the table in place to get a square edge. I then put a line on the side opposite to the opening 2mm down. That was to set the pitch which I then sanded to. That only helps for the largest semicircle but is quick and accurate. Make sure the sanding line is running parallel as seen in pic 4.
Marking the circular shape on the opening, I used a coin that happened to be the correct size. Its a good way to get an even circle to base the carving off. This is the one are that has to have an accurate cross section. After marking the circle I was able to project some lines back which helped in getting a center line. That center line is something that I want to have remain until the very end of the project.
Making the most of the sander, I started to shape the outside the amorite, rounding off the corners
Step 4: Setting the Levels
I use a range of different cutters in my Foredom micromotor. The beauty of this machine is that I can easily change out cutters, perfect for a carving job like this. You can also use a dremmel or similar tools. The cutters i used were different sized cylindrical cutters, dovetail cutter, star cutters, saburtooth burs, spherical cutters and a point cutter.
Using the 2mm star cutter, i started tracing the line. The 2mm is prefect because this is the distance that I wanted to reduce each level at. I also made others markings as depth reference points (pic 3). The Saburtooth bit is my more aggressive bit and perfect for roughing the shape. I used this to start working down the area of the second semicircle. I also rounded the corners and then used the carbide cylindrical cutter to get a cleaner finish.
Before going too far i also wanted to get my center depth set. I used the height of the cylindrical cutting bur as a reference. By rotating the cutter clockwise I widened the hole. I worked up from the center using the 2 cylindrical cutters in a fairly vertical position to set the levels all the way up.
Match this on the other side
Step 5: Shaping the Spiral
Now that I have my levels, I used the star cutter to follow the lines again. With that depth, I can now roll over the corners using the cylindrical cutters and go even deeper with the dovetail cutter. Its now just working with patience and slowly shaping it working from the outside in.
To clean up the bottom of the groove I used an engraving bit which is a 1.5mm spherical cutter. I found that gave me the cleanest finish.
I didnt worry about sanding this piece as I knew most would be remove with the texture.
Step 6: Adding the Texture
The texture is carved out using a 5mm spherical cutter for the first 2 semi circles and then I used a smaller 3mm cutter for the inside semicircle. Start by working in from the middle of the face and work downhill towards the center. After that you can work from the center down hill towards the outside. The reason for working towards the center first is to try and prevent over crowding in the middle. The outside will be widened a bit with more than just one push cut.
At the opening I also hollowed it out a bit using the larger spherical cutter. I didnt bother going too deep, just enough to give the look of it being a type of shell. When you see the fossils, they arent hollowed out much anyway.
Step 7: Preparing for Finish
I lightly sanded the ridges on the form, just to blend it a bit. I didnt bother sanding the groves. The unevenness of the carving give the character that I was after.
I covered the carving with an ebonising solution. This is a mix of vinegar and steel wool. This mixture darkens the tannins in the timber which blackens it. After it dried, I sanded the ridges again, just to get some contrast. Its worked great with it darker in the grooves, creating better shadow lines.
Step 8: The Base
I got another similar offcut, also jarrah. I cut a section off and held it near to the carving. I marked out what I though was good proportions and then cut and sanded it to shape. I marked center and drilled a 3mm hole to suit a brass rod.
Step 9: Fitting the Rod
Before drilling a hole in the carving, hold it at different angles to see what way it best displays the piece. The angle of the drill bit should aim towards the center of the piece. Drill it as straight as possible.
Measure the rod to find a good height to display the piece. This also takes a bit of trial and error. Using a hack saw, I cut the rod to length.
Step 10: Polishing
Being a small piece, spray can lacquer is perfect. I used pylon satin lacquer. It only does thin coats but dries quickly. I did about 5 coats, cutting back after the 4th.
I then used super glue in the holes to glue it together. I used Gorilla glue as its a thicker CA clue. Make sure that it is lined up parallel to the base when it dries.
This piece ended up looking much better than I expected. I really like the form and the finish on the piece. I might look at doing a much larger one in the future.
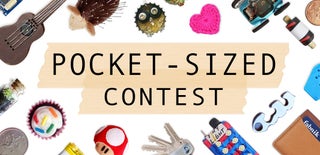
Participated in the
Pocket-Sized Contest