Introduction: Ballpoint Pen With a Lathe (bolt Action)
If you thinking about making your own ballpoint pen and you are not content with a cap for the tip, you maybe come across a bolt action mechanism. It is actuated by pushing a little button along a cam path. This is the simplest retractable pen design and therefore the one most people choose to make. I am no different in that regard, but I do some things in building this pen I didn’t see anyone else doing.
Namely, I use tubing in order not to have to drill a very deep hole (at least 15x diameter) or to have to make the body in two parts and I use a hole saw to one shot the cam without a mill.
Supplies
- 10x1mm soft metal tube (brass, aluminium,copper (at least 150mm))
- Round connector nut with a outside diameter of 8mm (mine are 12mm high and have a m4 thread and a stainless) (buy 10 make some more pens)
- Grub screw according to your nut
- Stainless steel rivet 2,5mm diameter and 8mm long
- Ballpoint refill
- Ballpoint spring all these can be found on ebay pretty easy and cheaply (the materials should be less then 30$ for ten pens, but it may make sense to turn these yourself)
Tools
- Lathe, there is a difffrent way to avoid having a Lathe, maybe I’ll also make a Instrucable for that one day.
- Some basic Lathe cutting tool
- Needle files
- Abrasive paper
- 12-15mm hole saw with a 3mm wid tooth (all the carbide one are that size)
- Some kind of drill, but since you have a lathe you probaböy have a drillpress
- Torch
What you turn beforehand
- Steel arbor 8mm diameter and at least 150mm long (just turn a 60 degree point on one end)
- Metal forming tool (just a old roller bearing pressed on a shaft, that can fit in one of your toolholders, will do. maybe turn a shoulder on the shaft and hold the bearing with a screw and some washers)
Step 1: The Tip
We will form the Tip out of the Tube by metal spinning!
In order not to mare the soft tubing it's a good idea to use some patting on your jaws (e.g. copper sheet). Now or before cut the tubing to a manageable size that doesn’t waste too much (depending on how long you want it, depending on your refill). Put the arbor in the Tube so the point is not sticking out but isn't far back either. Now chuck it up with about 40mm stick out (the less the better). you shouldn’t be able to move the arbor in any way. Finally put your aforementioned metal forming tool at an negative angle on your toolholder. I used around 1000 rpm. Depending on the rigidity of your Lathe and the used Bearing you might increase that.
with both hand engaged on both handwheels you should start touching the Tube with the bearing. The tube deformes easier than I expected, but you need to use some light pressure, comparable to that of taking a few mm cut in steel. Try to maintain the pressure throughout a pass by moving the cross slide in while moving in positive Z direction (form spindle to tailstock). Be careful and take light passes on just to tip of the tube. The tip will deform into a point and the hole will decrease diameter.
Most pens have a 2.5mm hole for a 2.5mm refill. When your tube is about half the way there, there tends to be some work hardening.cut of the burr. It's a good idea to heat the tip with the torch to release those stresses. In case of brass you can heat it up to a dim red glow and quench it in water. Now the the piece back to the lathe and finish the tip the the described technique. Check with your refill if the hole is small enough. make it a little bit smaller than the refill is thick and drill out to the correct diameter after. Maybe a little filing and abrasive can smooth out the tip, but you should try make it as smooth as possible with the bearing.
If you want a knurled grip, now is the time.
Step 2: The Cam “C”
Before I thought of this method, I just milled a channel (on the lathe) and filed the rest of the CAM channel, but the results weren't that good and it was pretty labor intensive. The result was a “J”. I wanted to make a “C” like the fancy bolt action pens, but doing that by hand was even more labor intensive. So I had a Idea to use a hole saw and it works. It works really good even.
This is how it works: Put the holesaw in the chuck, put the “pen” in the tool holder in a way that there is a angle of 80 degrees between it and the lathe centerline on the left side (see picture!), adjust the height of the toolholder in such a way that the centerline of the holesaw mets the uppermost edge of the pen (a few mm below is also OK), now adjust the X-axis in such a way, that there are about 5 mm between the holesaw and the refill. Best to hold the refill next to the pen and measure that way.
Now Turn the lathe on a slow speed, maybe 500 rpm and feed in very carefully and slowly until the hole saws edge, that is nearest to you, slightly behind the centerline of the tube and the other edge is slightly before the centerline of the tube.
Now cut the Pen to the desired length.
Please tell me if you have any suggestions or questions how I can phrase and picture it better.
Step 3: Deburring
Puh …. That was a little much...
Now you are almost done! just deburr all the harsh edges with the needle files. Especially the cut “C” cam, because there is where you acuate the pen.
Step 4: Cross Drilling
Grab a marker. Now put the spring on the refill ,drop them inside the brass body, drop the round connector nut on top and then push all these parts inside till the refill sticks out as much as you want it to stick out in normal operation. Make a mark on the low right point of the “C” (see the Picture). Now take everything out again and center punch the round connector nut, before crossdrilling it 2,5 mm diameter 7 mm deep.
Then deburr the hole.
Step 5: Polishing and Assembly
Polish the pen to your heart's content, before assembling it. Put the spring on the refill and drop them inside the brass body. Screw the grub screw in the round connector nut. Use the allen key to push the nut inside until you see the cross drilled hole in the c and put the button / rivet inside that hole. Now tighten the grub screw. and you are done !!! Yeah, not thaaat bad right!
PS.: If you don’t like how much the Refill sticks out you can shorten the round nut a little or even drill on a different place.
PPS.: If someone actually makes a version of this pen are inspired by this, let me know I really want to see the results and hear your thoughts. If you use Instagram hit me up and or tag me @astjaegermaker ( https://www.instagram.com/astjaegermaker/ ) otherwise send me a message here or a comment, whatever... Email me if you want Astjaeger@gmail.com… and tell me about my nigerian uncle that died… just don’t make it the subject line!
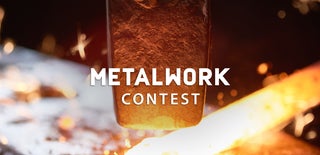
Participated in the
Metalworking Contest