Introduction: Bentwood Ring. Driftwood From the Oregon Coast and Douglas Fir.
This ring is entirely made form wood found in the neighborhood and at the Oregon coast in Lincoln City.
Materials and Tools Needed:
1. Wood. a straight stick, at least an inch wide or more.
2. Block plane. any hand or finger plane will do, it just depends on how much muscle you want to put into it.
3. Vise.
4. CA glue... (super glue) I use the cheap stuff from the dollar store.
5. Oil. I used to use olive oil because everyone has it at home. I use boiled linseed oil. Both are good. .
6. sandpaper.
7. something round.
Step 1: Find Some Wood.
I found my wood from a tree in the neighborhood, and at the Oregon Coast in Lincoln City. Great gift for anyone you know who loves the outdoors. choose some wood from a significant place. This is my new wedding ring. We spent our honeymoon in Lincoln City.
My favorite thing about this project was finding what the inside of the wood looks like! It's always a surprise. Especially with the driftwood. Driftwood has some great detail, depending on how long it's been soaked, and how many cracks it has in it.
Step 2: Plane the Wood.
Most crappy looking wood or sticks look like gold once you find a smooth flat spot in it.
1. cut a mostly straight piece out of the wood. preferably with less branches growing out of it to avoid knots. Though I managed to get a great one onto the face of my ring, and love it.
2. carve the stick or whatever you find, to see what the inside of it will look like. I brought this knife to the beach to see what pieces of driftwood fwere worth taking home. Pretty fun treasure hunt.
3. plane the wood flat. I used a block plane and a little finger plane. both stanley.doesn't matter. At this point, I wish I had a draw knife. If you have a draw knife, then you know what to do. A spokeshave would have also been nice. But, for me, I just used a knife and some small planes, because that's what I've got.
Step 3: Create the Ring Blank
1.If you used a plane or a spokeshave, try to get some shavings like so... Thin shavings but not see-though. These work better than store bought veneer because they are thinner. When glue-ing, they encorporate super-glue into the ring better with more and thinner layers. This is why DIY is better than buying veneers... they usually come quite a bit thicker. The bentwood process usually calls for boiling or steaming the veneer, and 2 layers is already quite thick. Using this process you can get 4-5 layers at the same thickness, and they are thin enough that you can use them dry.
2. When Glue-ing, always wrap the shaving opposite the way it naturally curls.. >IMPORTANT< On every shaving, there is a smooth side and a rough side. wrapping opposite the curl makes sure the smooth side faces out. Also, as you glue, add glue then hold tight only about an inch or less (half the ring) at a time, and let the glue dry a bit before you continue. Make sure you line it up good and wrap it tight. you can't re-adjust as you go. if you try to bend to wood straight as you wrap, you will have large gaps in the sides of the ring.
3. Glue up the ring. I use a socket to size my rings while glue-ing. >IMPORTANT TIP< don't glue on the bare socket... it will be stuck forever. I usually wrap the socketwith inside out scotch tape. that gives it somethings to wrap around that will be quite easy to slip off after the glue dries, and scoch tape will easily come off of the inside of the ring.
4. Shape and Sand the ring. I use a jeweler's saw to cut the sides off, and then run it along a piece of sandpaper flat on the bench. I use 80 grit for shaping, and up to 400 before continuing to the next step.
Step 4: Add More Veneer
Make the outer Veneer.
1.This step is similar but more involved than step number 2.
Once the wood is flat, you need to cut out a thin layer of it. You won't be able to do this thick enough with a plane, because the wood will crack. I cut under from the side with a coping saw. any saw will do.
To thin it our further, I put some blue tape over the smooth side, (The side I want to show on the outside of the ring) and used some double sided tape to stick it to a flat surface. NOW, you can use a finger plane, block plane, rough sandpaper (glued to a hard block)... whatever, to get it pretty thin and flat. It's going to need to be as thick as you can keep it and still flexible enough to bend around the circumference of the rings without cracking. The tape also helps it from cracking before you glue it to the ring.
2. Glue the veneer to the wood
Once your veneer is thin and flat, glue it to the outside edge of the ring.
I did a few different segments, combining 2 or 3 different pieces of driftwood from the Oregon Coast.
The liner (inner core just used in the previous steps) of the ring was made from the douglas fir branch.
Step 5: Sand Sand Sand
By this point, you can sand it up as much as you want, shaping as you go. I use 150, 220, 400, 800, 1200, 2000..
Pictured above are some of the sanding tools I've made for the process.
I like to round all the edges so it's nice and comfortable, and doesn't snag on anything.
Step 6: Polish
Here's where your ring really shines!
ok, but seriously, watch this video, I'm not claiming this one, but this is the best way to polish your ring, accept I don't use a lathe, I jsut hold it in my hand and rub it on. Works like a charm.
BLO/CA GLUE POLISH Video
Above is the finished product, along with a few other rings I've made.
Hope you're inspired! Check out my website if you're too lazy to make one yourself.
www.etsy.com/shop/naturalbentwoodrings
If you want more details I've already made a much more in-depth tutorial with many more tips and tricks on bentwood rings here. picture are not as good but the information is great. I've upraded my camera since.
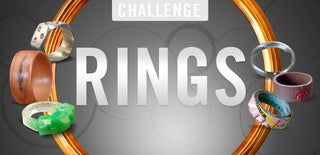
First Prize in the
Rings Challenge