Introduction: Build a Replica Skyrim Shield
This shield is from the video game Skyrim. Each of the nine holds, or cities, has this shield with a unique symbol . I'll take you through my process of creating two shields. One I approximate as game accurate size at 24" with the Dawnstar symbol and another at 18", with the Windhelm symbol.
Preparation:
• The shield is based on in-game images from Google image search.
• I sketched the shield in Google Sketchup based on various images extrapolating the size of the shield from the size of the in game character.
Supplies:
• 1/8" plywood for shield faces
• 1/2" extruded polystyrene insulation or expanded polystyrene insulation sandwiched between the plywood to reduce weight
• hard board for edge banding
• polystyrene plastic as a guide for the 'metal' edging
• Evercoat Z Grip body filler to create the perimeter 'metal' edging
• 1/2" wood blocking recessed into the foam for the handle and strap
• aluminum handle for the back
• scrap leather for the back strap
• screw in snap buttons to hold the leather in place
• spray primer for the perimeter body filler
• metallic silver spray paint for the perimeter banding
• black paint to weather the silver
• stain for the plywood
• paint, various colors including blue for the shield face and white for the symbol
• paper, printer, and tape for the symbol stencil
Tools:
• tape measure
• circular saw
• compass
• jig saw
• router
• scroll saw
• exacto knife, optional cutting mat
• electric sander -sanding block
• drill
• paper towels
• gloves optional
Safety concerns:
• A table saw can remove fingers very quickly if you don't pay attention. Proceed with caution when using jig or scroll saw, don't cut near or on your favorite antique.
• When drilling, make sure you don't accidentally drill through anything you don't want to.
• Spray paint must be used outdoors in a well ventilated area. A respirator or mask is recommended. Allow time to dry fully.
• Wear old clothes for painting. Chances are paint will find a way to get on your clothes.
Step 1: Crafting Planks
I sized the shield according to the elbow to knee length as seen in the in-game image which scales to twenty-four inches. The shield is comprised of the 1/2" insulation sandwiched between two sheets of plywood to keep the weight down. The perimeter edging is body filler painted to look like steel.
The plywood sheet was cut into two 24.25" x 24.25" squares, a front and back. I cut it larger for trimming later. Mark the center of the wood. This needs to be done for both sides. I also created a smaller shield that was cut to 18.25" squares.
Fashion a compass with a nail and a wood dowel. to measure the circle. Use a jig saw or band saw to cut the circle. Cut it a bit larger for sanding and shaping later.
I used photoshop to sketch the wood grain based on screenshots from the game. A bit of interpolation was used as screen grabs lacked clarity.
I created a projector to trace the wood grain onto both sides of the shield. A magnifying glass, a cardboard box, and tape are the minimum of what you need to make a projector with your phone. It would have been easier to just print out six letter size sheets and tape them together, but the cardboard box projector was a fun project.
I mirrored the image and re-projected it for the other side so that the pattern is continuous front to back.
The paper was sprayed with adhesive. I let it set up for ten minutes to make removal easier so that it won't stick to the plywood as well. A router v-groove bit was used to create the grain in the plywood on both sides.
The plywood was cut with a scroll saw along the board joints and the edges lightly sanded to distinguish the individual planks.
I drew a circle on the insulation and cut that as well. For the handle mounting, I cut a piece of 1/2" MDF to embed in the insulation between both sides, so the mount would be solid. I also trimmed the corners off the insulation. I measured where the blocks were and drew this on the 'back' side of the shield. It's best to already have your handle for the back to ensure the block is the right size. I cut the block first which almost created a problem.
I applied wood glue to the edges of the bottom sheet of plywood, fit the
planks together and then applied Gorilla Glue to the back side of the plywood. The plywood was placed face down. The bottom of the insulation was dampened, per Gorilla Glue instructions, and placed on top of the wood. Then the top side of the insulation was dampened, gorilla glue was applied to the insulation. Wood glue was applied to the edges of the top sheet of plywood, and that was placed onto the insulation. Once everything was lined up, I placed weights on top while the glue dried.
A belt sander was used to sand the insulation and shape the wood to be perfectly round based on the original pencil line from the compass.
For the edging, I used 1/8" hardboard strips cut to 1/2" tall. Gorilla glue was used for the edging, dampening surfaces before use.
There are a couple of ways to glue the edging in place. I tried multiple clamps on one shield, but came up with a better idea on the second shield. I used a belt from an automobile engine and a clamp to hold the edging in place. Since the belt is continuous pressure it avoids the slack between clamps. You will need to weight down the shield as the pressure from the clamp will cause it to flip. That's sixty pounds in the picture.
Step 2: Forming Metal Edging
To begin forming the metal edging I pulled out my compass again. I created circles for the peak and inner ring of the metal banding. This was done on both sides. I cut half inch strips of polystyrene. This will serve as a guide for shaping the banding. Using super glue I glued the polystyrene to the circle representing the peak of the banding.
Body filler is used to shape the metal banding. It's comprised of the filler and a catalyst. I like the Evercoat brand and avoid Bondo brand. I used a 4" plastic spreader to mix the body filler on a piece of cardboard. Don't mix too much at a time. Start with a golf ball sized amount.Mix the gray filler and blue catalyst fully. The mixture should be a consistent green color. The working time is ten to fifteen minutes. You will know when it begins hardening. You can try to continue spreading, but it will get extremely difficult. The finish doesn't have to be completely smooth. The imperfections will help the weathering process.
Painters tape was used to serve as a guide for the inner ring. Just a pencil line will become difficult to see once you start spreading filler. Remove the tape before the filler is fully cured. Once cured the tape will be much tougher to remove. I waited too long for one shield and had to carve the curve with an exacto knife.
Once the rings are done, use the electric sander to shape it. I started with 40 grit paper. The sand marks will add depth during the weathering process. Once I got the overall shape, I used a sanding block to knock out any high spots. The electric sander doesn't offer precise control. I moved to a sanding block with 220 grit paper to smooth out the finish.I then took a Dremel grinding bit to clean up the edge of the inner circle by hand. This cleans up the edge making it uniform. This is done for both sides.
Step 3: Paint and Weathering
Now that we've built a shield, we need to paint it. Tape off the wood portions of the shield on both sides. Primer the body filler with spray primer. Spray the first coat, wait ten minutes and spray a second coat.
Wait a day and then spray a silver coat. I used a metal look finish spray.
I used a dark stain for the wood. I didn't tape off the silver. The stain rubs off easily. Don't erase the pencil marks locating the wood blocking. It should be visible even after staining, just barely. You will need these later.
To weather the edge banding, I wiped on a thin coat of black enamel paint with a shop towel. I then wiped it off with a clean shop towel. The paint will stay in the voids and imperfections, adding depth. The black paint tinted the silver slightly darker which made it look more like metal.
I used blue Rustoleum enamel paint for the symbol side of the shield. I use a roller to apply two coats waiting ten minutes in between. The Windhelm shield could have used a third coat to make it more vibrant to match the game. I mixed blue and black to approximate the Dawnstar color.
I created the symbol in photoshop based on in-game images. I printed them on printer paper. The Windhelm symbol fit on one sheet and the Dawnstar took four. I taped the Dawnstar sheets together and used a exacto knife to cut out the stencil. I left 'bridges' for the Dawnstar stencil to keep it together as it has multiple unconnected pieces. I sprayed the backside of the stencil with spray glue and let it sit for fifteen minutes. This way it's tacky enough to stick to the shield but won't stay stuck. I applied enamel paint with a brush for the symbol. You don't want too much paint on your brush. Dry brushing creates a faded looked the lends to the shield looking old. Remove the stencil while the paint is still wet. I used a small brush to fill in the bridges. Once the paint is dry, I used water color washes of browns and blacks to dim the symbol and add more depth. Weathering is about adding subtle colors and depth and making an item look used and real.
Step 4: Handle and Strap
Earlier I mentioned that I added wood blocks cut into the foam when I sandwiched the panels. Marks should still be on the back of the shield. I used a window sash handle on the smaller shield and a steel handle from the hardware store on the larger shield. Mark the holes and drill pilot holes. Be careful not to drill all the way through the shield. It's best to have your handle to accurately size the block first. I installed the block first and had to bend the handle slightly to make it fit the block. The window sash handle was weathered bronze and didn't require additional finishing. The steel handle was bright. I used black enamel paint, wiped it on and wiped it off to give it a bit of a grimy look.
For the arm strap, I bought scrap leather from a hobby store, cut it to size and used the screw part of a snap button to hold it in place. Again, pre-drill the holes. You can tell in the images that I have not added the smooth heads for the snaps, but you easily could.
At this point you could clear coat the shield. Use a matte finish paint as gloss wouldn't look right. I skipped this step.
I would advise using a piece of foam at your wrist if you plan to wear it for any amount of time. The shield hits my wrist in just the wrong way.
Your shield is now done. Wear about town, shield yourself from hail, or use it to decorate your house. Mine hangs on the mantel.
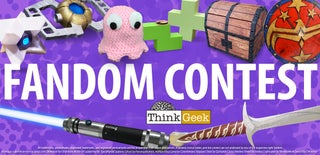
Participated in the
Fandom Contest