Introduction: Build and Upholster an Oversize 'couch'
I built this in the showroom of the handbag company where I am a designer. Space was limited, but with a lot of improvisation, I was able to make it work.
Step 1: Gather Materials
Materials are given for the specific size and shape of the 'couch' that I built, and any variation will affect the supply needs.
3 sheets 1/4" 4' x 8' Lauan Plywood (wood type doesn't matter; I went with the cheapest option. In hindsight, I also would have used 1/2" thick; to prioritize strength rather than lighter weight.)
1 2"x4" x 96"
1 2"x4"x 92 1/2"
2 2"x4"x 75"
1 2"x4"x 56"
3 2"x3"x 16"
1 2"x4"x 15" (I did purchase & use additional 2"x4"s for reinforcement. If you start with the 1/2" plywood, you may decide this is unnecessary.)
3 pre-made Queen Anne French style chair legs (make sure that if you order online, you are sure about the height of the legs. the site I ordered from included the tenon height in the overall height -which none of the other websites had done: this is why some of the tenon is visible on ea leg.)
3 sheets of 4" x 40" x 72" foam
2 packages of 81" x 96" batting (as thick as possible)
7 yards poly/velvet fabric (I actually bought 8 and had a lot left over...)
1 package Crystal Upholstery buttons (24 to a pack- I used less)
spray mount adhesive
a couple yards of ribbon or string
Tools:
power drill
jig saw
staple gun & staples (the serious kind, not the office kind)
long piece of wire
electric turkey knife (cuts foam like butter!)
utility knife
**I didn't get photos of all the supplies; but everything except the wood and fabric was purchased on Amazon. And I'm happy to take questions.
Step 2: Measure, Re-measure and Cut
I laid out and marked all my 2"x 4"s (which I had delivered, pre-cut from the lumber yard). I also laid out some of my other supplies, in a mock-up, just to check that I had enough of everything.
I had drawn the curve shape for the back, in Illustrator, so I was able to print & piece the pages together. I used this printout as a template for drawing the topline of the back. You can free hand it or use various drafting tools. Once I had traced the template, I used the jigsaw to cut out the shape. I also cut the plywood rectangle to fit the seat/bench part of the piece.
And I painted the front 3 legs that I had ordered premade and the back 3 legs that I used the 2"x4"s.
Step 3: Drill, Baby Drill
Screw all your frame pieces together, for the back and bench. Attach the pre-made legs and the 2"x4" legs and double check that everything is square and level. (do not attach the back to the bench yet)
Screw the plywood back shape to the back frame and the bench portion to the bench frame. I used an additional 'wing' piece on each side of the back, to get the curve shape.
Step 4: Glue and Cut the Foam
Lay the foam pieces out for the bench and the back & plan your arrangement. Use the spray adhesive (or any strong glue) to attach the foam to the plywood. Then use the electric turkey knife to cut the foam to the shape of the back and bench. (I glued and then cut; however, if you can manage; I would recommend cutting first. The glue gummed up the knife & it eventually died. Was still able to use the blades to cut the foam- but it was significantly more difficult/annoying.)
Step 5: The Batting...and the Fabric...
Lay out your batting on the back piece and the bench. Cut roughly around the shape, allowing yourself lots of extra to wrap around and finish at the back.
Do the exact same thing with the fabric, on top of the batting.
At this point; if you wanted to use a few staples to temporarily tack the fabric and batting in place, you could. However, I found the the texture of the foam and the batting and even the fabric meant that everything stayed pretty well in place.
Step 6: Tufting
This part you definitely need two people.
Plan out how many and where you want your button 'tufts'. This took a lot of measuring and remeasuring for me.
Using a small drill bit, drill through the plywood where you want the first button. Take the wire: doesn't matter what kind; it needs to be soft enough to work with, but firm enough to force its way through the foam, and fold in half. Poke the bent center (not the two loose ends) through the hole you just made and through the foam and batting. Don't feed the wire all the way through, hold on to the loose ends from the back. You will need to use a utility blade or scissors to get through the fabric. From the front, thread a button onto a foot or so of ribbon and feed both ends of the ribbon through the bent wire- like threading a needle. Pull the wire back through, bringing the thread with it. Have someone stand in front and help you gauge how tight to pull the ribbon. Once your tuft is how you like it, use the staple gun to attach the ends of the ribbon to the back of the piece. Repeat for as many tufts as you desire. -There are probably easier/ better ways to do this, but I chose to do it this way; so that I could easily remove the buttons and change the fabric if I decided.
Step 7: Finishing
Now it's time to attach the fabric and the batting. Choose a starting point and pull the fabric and batting tight, wrap around the edges and staple to the back. Work your way around the whole back piece, pulling and smoothing as you go. After you've gone around once, you may need to go back around and neaten the ends of the fabric- cutting or adding more staples.
Once you've completed the fabric on both pieces, you can attach the back and the bench pieces.
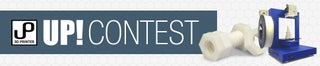
Participated in the
UP! Contest