Introduction: Corner Notcher
I do a lot of sheet metal work, mainly in Aluminium, I am forever cutting corners or 90 degree notches for folding boxes and so on. I wanted to make life easier, to cut out the sawing and filing, I needed a corner notcher.
I picked up a 1/2 ton arbor press second hand from ebay and the build began!
Step 1: The Arbor Tool Attachment
Other than the hole in the middle, which needs to be a good fit on the arbor, the sizes of material for the ring is unimportant, it just needs to look right :) The ring has 2off M4 tapped holes opposite each other that will attach the completed cutting tool.
Step 2: The Cutting Blade
I found an old rusty file that was the same width as the collars diameter, using a hammer I broke it up until I had a piece that was about right for the blade, I suggest you wrap the file up in a piece of cloth whilst clouting it with the hammer as, being glass hard, chips will tend to fly!
The cutting edges must be ground at exactly 90 degrees, keep checking this angle with a set square, and need to be sloped back very slightly. The rest of the angles and cuts are unimportant.
Step 3: Joining the Parts of the Moving Blade
The cutting needs to happen in the same way as scissors come together, in a sliding action. There are 2 ways to get the desired result when welding the parts together, the drawing shows a thin steel packer between the front edges of the two parts, this will melt in as it is welded. I ground a slight angle on the collar as can be seen in the photo of it clamped together ready for welding.
Step 4: The Fixed Blade
Cut from a piece of 3mm MS plate, it needs a 90 degree notch and 2 fixing holes, work out the sizes and positions by making a quick template as follows. Fix the moving blade onto the arbor using a pair of screws and locknuts to hold it tight. Place a piece of card on the base of the press, bring the arbor down until it touches then mark the sides of the cutter and the size of the press casting. From this you can work our where to put the fixing holes. Be careful in positioning the holes as you will need to be able to copy drill and tap them into the frame casting.
Transfer the dimensions from the template to the steel, drill the holes and cut the notch. The angle of the notch will need to be filed pretty accurately using the moving blade to gauge the fit. The fixing holes will need to be countersunk so that the screw heads do not stick up above the plate.
Step 5: Drilling the Frame
After marking out the fixing holes on the base of the press casting I could see that I would not be able to drill it with my pillar drill so I had to break out the flexi drive drill!
Step 6: Ready to Go!
With the parts assembled it just remains to adjust the arbor carefully so that the blades will slide past each other.
To use the notcher place the material to be notched in the correct position, lower the moving blade until it touches....then clout the top of the arbor with a heavy rubber mallet! Do not use a metal mallet as it will distort and damage the top of the arbor.
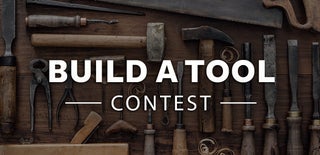
Participated in the
Build a Tool Contest