Introduction: DIY 18650 Lithium Ion Cells Charging Grid
I have been working on motorising my bicycle using a geared DC motor and now I need a battery pack for that. So to make a battery pack I have decided to go with the popular 18650 lithium ion cells from two old hoverboard batteries.
Since the cells are from used batteries so I need to balance charge all the cells before making the battery pack. Everytime I use these 18650 cells I need to go through this stage when I need to balance charge all the cells individually to get them at the same potential.
Now to get through efficiently I decided to built a dedicated charger for 18650 cells. Moreover, I have decided to make it a modular charger so that I can add up modules to form a larger grid that enables me to charge as many cells as I want simultaneously.
Don't forget to vote us in the PCB Design Contest.
Step 1: Design
Since we need the charger to be modular, easy to built and low cost so I came across these TP-4056 lithium cells charging boards. These boards are specifically made to charge lithium ion cells with a micro USB input, over charging protection and above all they are dirt cheap.
For each module I decided to go with two cell holders, each one of which can hold up to four cells. So for each module we are going to need eight TP-4056 modules.
For the main input of the board I have used an XT-60 connector but we have the option for charging two or three cells only using a cell phone charger as well.
Now to keep things simple and neat I decided to design the printed circuit boards.
Step 2: Ordering the PCBs
To save time I decided to order the PCBs. So I visited PCBWAY and after going through a couple of options I ordered 10 boards. These boards will be enough to built a charging grid thats capable of charging upto 80 cells simultaneously.
Once I uploaded the Gerber files I waited for the designs to get verified to make sure there is nothing wrong with the boards. Well thats one of their many useful services and this project is made possible by them so make sure to have a look at their website for great quality PCBs at an outstanding price.
The link to the PCBs and the Gerber files for the circuit boards is:
https://www.pcbway.com/project/shareproject/18650_Cells_Charger_PCB.html
For discounted coupons for PCBs have a look at the link:
Attachments
Step 3: Components and Tools
Within just a week the PCBs were on my workbench and the quality pretty much talks on its own so guy have a look at their website as they made this project possible by sponsoring it. I gathered all the components. The BOM(Bill Of Material) file is attached in this step.
For the tools we are going to need the basic soldering stuff.
- Soldering Iron
- Soldering wire
- Pliers
TP-4056 modules:
https://www.banggood.com/custlink/GKGDDk05kP
Attachments
Step 4: Assembling the PCBs
To assemble the PCB all we need to do is to drop all the components as mentioned on the board. I have started by soldering the charging boards and then moved towards the bigger components.
Once I finished soldering all the small components I then soldered the cell holders. Make sure to match the polarity on cell holders to that mentioned on the PCBs.
With all the components around it took me hardly 10 minutes to complete one module. Now before I make more modules,I tested this one.
Step 5: Testing the Modules
Now to test the module I plugged my cell phone charger to one to the TP-4056 board using a micro USB cable. This allows me to charge up-to three cells.
For charging eight cells I have used a PC power supply with the 5v input using an XT-60 connector. The module flawlessly charges each cell. As the cell is completely charged the light over that particular charging board turns blue from red and we can turn of the switch for that particular cell to save power.
Step 6: Making the Charging Grid
Now to form the whole charging grid I have made some more modules as I have to charge a lot of cells.
After making a couple of modules I then assembled the modules using some nut and bolts as I don't have the required standoffs. now to power the whole grid I have used the same power supply as in the previous step. As each module is connected in parallel across the standoffs so providing the input through any of the modules will provide the power across the whole grid.
Step 7: End Results
The whole project turned out to be a really useful one as now I have a customised charger that can charge as many cells that I want. The whole charging grid costs me a fraction of the price of a professional chargers available in the market and they don't have the capacity to charge as may of them.
The PCBs Made everything neat and the pre Made charging boards saved a lot of hassle and I am really happy with the end results.
For more fun projects stay tuned and subscribe to my youtube channel.
https://www.youtube.com/channel/UCC4584D31N9RuQ-aEUxP86g
Regards.
DIY King
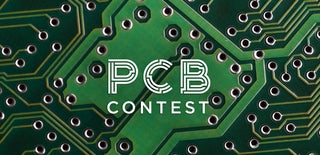
Participated in the
PCB Contest