Introduction: DIY 3D Printed Headphones
A while ago I was wondering if it would be possible to 3D print a great sounding pair of headphones. A search online didn't throw up many other people who have done so, or any literature on how to do it, in particular making them sound great. So it was the perfect project!
After a few mediocre prototypes, a ton of testing to see how different design variables affect the sound and countless design iterations, I've arrived at a design that sounds awesome, looks great and is cheap and easy to build.
The parts should cost you around $35.
If you are interested in reading more about the work I did in creating the design, it's all at Homebrew Headphones. In particular, you can read about how the design variables affect the sound here and about my test setup here.
Step 1: Tools and Materials
Tools needed:
- 3D printer (if you don’t have one, you can get the files printed at Shapeways or 3D Hubs)
- Soldering iron and solder
- Misc hand tools, eg pliers, knife, scraper etc
Materials
- Drivers: I’ve used Dayton Audio CE38MB-32 drivers with great results.
- Ear Cushions: Bose QuietComfort QC15 QC2 replacements, https://amzn.to/3zlGpkw
- Cable: Sol Republic Master Tracks HD V8 V10 V12 X3 replacements work well. https://amzn.to/3vwckNZ
- Audio Jacks: 2 x 2.5mm audio jacks, https://amzn.to/3OPIzOY
- Wire: 4 pieces of approx 10cm (2″) long hookup wire with ends stripped. These from Ebay are pre-cut and stripped.
- Glue: you need a gel consistency glue suitable for plastic, such as Loctite Gel Super Glue or https://amzn.to/3Q8bQFD
- Plasticine, Bluetac or similar. https://amzn.to/3oIkxeg
- Solder, eg https://amzn.to/3BwZaEb
Files to be printed:
1 x headband
2 x baffles
2 x covers
I recommend printing them in ABS. Use 5% infill for the headband to give it flexibility, and about 10-20% for the others. The baffles and covers require support, the headband does not.
Print the parts in the orientation shown ion the photo then clean off all the raft/support.
Step 2: Solder the Hookup Wire to the 2.5mm Jacks
Cut the hookup wire into four approx 2″ or 5cm lengths and strip the insulation about 1/8″ or 3mm from the ends.
Remove the two jacks from their plastic covers. If you are using the jacks we recommend, solder the negative (black) wire onto the large tab and the positive onto the small round one (see the picture)
Step 3: Attach the Jacks and Drivers to the Baffles
Screw the jacks into the holes in the baffles.
Insert the drivers into the baffles. Be extremely careful to not damage the fragile mylar film in the drivers.
Important – the terminals on the driver should be 90° from the jack, oriented towards the hook-up wire retainers (yellow circle in the picture).
Glue the drivers into the baffles with four 1/4″ (6mm) length spots of glue, placed evenly around the perimeter of the driver (blue arrows in the picture). DO NOT glue around the full perimeter of the driver, as this will adversely affect the sound.
Wait until the glue is dry…
Step 4: Solder the Hookup Wire to Drivers
Solder the hookup wires onto the driver terminals as shown in the picture. The red terminal and one next to it are positive and the other two negative.
You won’t need any solder for this – melt the solder tab on the driver with your soldering iron, then insert the wire into the puddle and remove the iron while still holding the wire until the solder solidifies. Be careful not to apply too much heat, as this may damage the driver.
Route the hookup wires behind the retainers so that they don’t get snagged by the headband.
Step 5: Tune the Sound!
Now for the secret sauce! In this enclosure, the Dayton Audio CE38MB-32 drivers are way too bass-heavy and lack high end detail, so we need to reduce the mids/bass to make it more equal to the treble. You may think more-is-more when it comes to bass, but there will still be plenty after completing this step. If you don’t believe me, do a back-to-back comparison.
If you’re not using the Dayton CE38MB-32 drivers, you’ll have to tune them to your taste – some will have a denser fabric on the back and will not require this step.
Using plasticine or similar, roll a small amount into a sausage then block all but one of the holes under the black fabric on the back of the driver. The black arrow in the picture shows the non-blocked hole.
Step 6: Put It All Together
Attach the fabric that comes with the cushions to the baffles using the adhesive that comes on them.
Fit the baffles to the covers, making sure the headband end of the baffle corresponds to the headband end of the cover (ie the two square holes line up). They may take a bit of force to get together – they are deliberately a tight fit so that they don’t require glue and can be disassembled.
Fit the cushions to the baffle. These are quite a tight fit, but go on easiest if you fit the long sides last (blue arrow in the picture).
Insert and adjust the headband, plug the cables in and you’re done. Put on some awesome tunes and enjoy your new headphones! I hope you enjoy building them and listening to them as much as I enjoyed designing them!
Note – there is a left and right side, so if they don’t feel right, swap the sides.
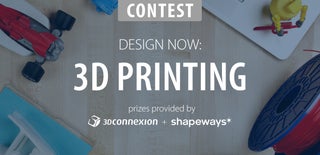
Third Prize in the
Design Now: 3D Design Contest 2016
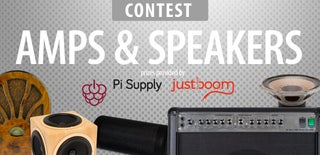
Second Prize in the
Amps and Speakers Contest 2016