Introduction: DIY Huge Sewing Table for a Craft Room | Custom Storage Shelving Unit
I have wanted a sewing table for a long, long time. I actually got lucky a few months ago and found myself with a craft room of my own, and so decided that it was time to create exactly the table I always wanted.
Equally as important as the tabletop space is the storage underneath...particularly storage space for very awkward items.
I have an A3 guillotine, an A3 paper creaser, 3 long greeting card boxes, and a disassembled tabletop loom, and let me tell you that those things are a real pain to store! They are mostly long and thin which is why they do not fit on your normal shelves or in your normal cupboards. In my previous home, they had to be kept on top of tables, and that was really not a good solution because then there was no table space spare.
So I set about designing a table that was easy to build, as cheap as I could feasibly make it, and had storage areas underneath to keep all my awkward crafty things organised.
In order to keep the cost, time taken and the weight of the table to a minimum, a few parts are bought from IKEA. The areas that need to be custom sizes have been made by me and my helpful boyfriend (i.e. the owner of the power tools :))
We have not built furniture before so this is a pretty basic and simple build - and it proved to be a good starter project for woodwork newbies.
I really hope you like what I've created, thanks for reading!
Step 1: What You Will Need
- Wood: I used 25 mm and 18 mm MDF, plus a piece of 3 mm hardboard. I wanted an even and smooth white finish so that it would match the white IKEA Kallax unit as closely as possible - meaning that all of the units would match in the final assembled table.
You could use plywood instead if you wished, or even a wood with a nice grain on it that you want to leave exposed and on display. It's up to you!
I had the pieces cut out for me at B&Q (a DIY store in the UK) which was a huge help, and was vital for me as I don't have any other way of cutting wood pieces that big. I believe you would need a track or table saw to cut the pieces yourself.
(Please see the next step for information on the sizes & dimensions of wood I needed.)
If you need to trim any wood pieces, you will also need a band saw, circular saw, or even a hand saw...or for small adjustments you could use a well-sharpened plane. Luckily, all of the wood pieces we had cut for us were accurate and so we didn't need to do any cutting ourselves.
- Router: To make 'through dadoes' (grooves/slots) in the wood surface. The dadoes I cut were 5mm deep and 12 mm wide, so I used a 12 mm straight router bit. Your router cutter size will depend on the width of the dadoes you want to cut.
If you're in the U.S. you could use a table saw instead of a router.
- Tape measure & ruler
- Clamps
- Hammer
- Paint, Paintbrush, Roller & Tray: I bought some matte white MDF primer (by Dulux) and some 'white' spray paint. However, the spray paint turned out to be more of a creamy yellow colour, and so since the MDF primer was already a really good match for the white Kallax unit that we already had, we just ended up painting the whole thing with only the primer. Maybe not what you are supposed to do, but it is exactly the finish I wanted!
- Masking tape
- Sanding block & sandpaper (240 grit or so)
- Breathing mask, safety specs, face shield & good ventilation; MDF dust is not good to breathe in, so you'll need these items particularly when cutting, driilling, sanding and painting.
- Wood glue
- Wood screws, plus a few washers.
- Drill & drill bits; I used an electric drill and a pillar drill, along with drill bits of 1.5 mm, 4 mm & 6 mm.
- Wooden dowels; The ones I used were 6 mm but I wouldn't go larger than that.
- Scrap wood: To make various jigs, and also to join the tabletops together. These pieces were mostly made using MDF we had left over from the initial sheets we bought, plus some small pieces of plywood and pine scraps we already had.
- Tabletops:I bought 2 IKEA Gerton tabletops, which are solid beech wood and measure 1550 x 750 mm each. Either find tabletops to make up the size of table you want, or of course you could make your own instead.
- Filler & scraper tool (optional); I used a tiny amount of white Polyfilla to smooth the joins and the MDF edges at the front of the units.
- Pencil
- Kallax flat-pack unit from IKEA (optional) & Inserts: We used the Kallax as part of the assembled unit, but of course you could make everything from scratch instead if you wanted. I also bought 6 ready-made inserts from IKEA; 4 cupboard door inserts and 2 drawer inserts.
- Felt pads; for underneath the units to protect the floor.
- Wallpaper, wallpaper paste, bowl, wallpaper brush, glue, utility knife & scissors (optional); This is what I used to cover the hardboard backing, however you could just glue the wallpaper (or other decorative paper) on instead. This is an optional step, as you may decide you don't want a backing at all, or you could paint the board instead of papering it. Also note that you can just glue the wallpaper on if you don't have paste.
Cost
I estimate that it cost me around £350 to make this table, with £72 being spent on the wood (although I had a fair bit left over too), £150 on the tabletops, £110 on the Kallax and inserts from IKEA, and a little more spent on paint and bits 'n' pieces. The tools and other things we already had, such as the router, glue and Polyfilla.
Although not cheap, I'm sure that if there was a product like this for sale it would be a lot more expensive, especially if it was custom built!
Step 2: Designing & Cutting
You will first need to design your units to make sure it will fit in everything you want. In my case, I had to measure all of my most awkwardly shaped craft items and figure out how and where to fit them all in.
I also needed to work out how high I wanted the table to be, considering I will mostly be standing up to use it, and also how big overall I want it to be. Once these dimensions are known, the sizes of the wood pieces you need can be calculated.
Diagram 1: This shows a wide but quite shallow unit which will house my paper creaser at the top, my guillotine in the centre, and then at the bottom I wanted to be able to have 2 IKEA Kallax inserts. These inserts will be ready-made cupboard doors, as they are just easier and cheaper to buy than make to be honest! For these to fit, the opening needs to be 335 x 335 mm exactly. The narrow gap in between is just what is left over, but would be big enough for A4 paper/card.
Note: In this unit only, I will be adding a hardboard backing. I have therefore made the top 2 shelves and the shelf dividers 5 mm shallower than the other sections. The effect will be that these pieces will be recessed at the back to create space for the hardboard back.
Diagram 2: This shows a narrow but deep unit which will house my 3 long card boxes. As with the other unit I'm making, the sides are made from 25 mm MDF, the shelves are made from 12 mm MDF, and 5 mm deep dadoes (grooves) cut into the sides will hold the shelves.
Diagram 3: This shows the pre-bought IKEA Kallax grid storage in grey, and then on top are the 2 blocks of 25 mm MDF that I'm going to need to add. This is mostly to make the 770 mm height of the Kallax up to the 850 mm height I want, but also to create more storage space in between these blocks that is long enough to house my loom pieces :)
Diagram 4: This shows the cutting guide that I took to B&Q to get my wood pieces cut. On the left is the 25 mm MDF and on the right is the 12 mm MDF. The smallest pieces I could buy of each thickness were 2440 x 1220 mm, so there was a fair amount of leftover wood.
Step 3: Routing
According to my design, I needed to cut dadoes (grooves) into the upright sections (/sides) of the 2 units I wanted to make. The shelves will slot into these dadoes.
Each 'upright' needs to have 2 dadoes cut into the surface. These dadoes must be created only on the surface which will face the inside of the units.
Note: If you plan on making a set of 'grid' storage units, you will need to put dadoes on both sides of the shelves as well, to house the shelf dividers. Therefore, you will need to use thicker wood for the shelves, in order to accommodate the dadoes. This Instructable (not made by me) is particularly good if you want to see how a grid design would be made.
I made my dadoes 5 mm deep, 12 mm wide (i.e. the thickness of my shelves), and they were cut all of the way across the width of my 'uprights'.
In total, I had to put 2 dadoes into 4 pieces of wood. As we hadn't made furniture before, we practised on some scrap wood first to work out where we needed to position the router to get the dado in the correct place.
We used our 'practice' piece of scrap wood to guide the router, as it has a straight edge. You can buy a straight edge or a clamp guide to do this bit instead of using a long piece of wood, but whatever you use, just make sure that it is long enough to span the width of the wood piece you're cutting into.
We used our practice run calculations (see the whiteboard photo, where the circle is the router and the top rectangle is the scrap wood guide) to place the scrap board into position on the wood piece we wanted to cut, and clamped it in place. In our case, the dado would be positioned 72 mm from wherever we placed the straight edge.
We then used the straight edge of the scrap wood to guide the router all of the way across the wood pieces to cut the dadoes.
From the photos you will see that for the the 2 narrowest uprights, we placed them next to each other with the sides lined up perfectly, then cut the dadoes across both pieces at once in order to make the position of the dadoes identical on both pieces. Just make sure the router moves smoothly across this join.
We didn't have the space to cut the 2 largest uprights side-by-side, so we instead made a jig (322 mm long) that helped us ensure the scrap wood was the correct distance from the edge when we cut the dadoes into the individual uprights.
What you are aiming for is for the sides of the units to be identical on the inside, so that the shelves won't be wonky and will go in smoothly. Repeat until you have cut all the dadoes.
Note: Don't cut too fast otherwise the cuts may not be smooth.
Your shelves should now fit snugly in these dadoes.
Step 4: Drilling the Dowel Holes
We're going to insert wooden dowels into the base of each unit (one in each corner), that will go up into the upright sides of the units. This is mainly for alignment purposes.
You need to make a little jig using scrap wood in order to drill holes into the bottom edges of the uprights, and into the corners of the base pieces.
You want to drill 2 holes into the bottom edge of each upright, a decent distance from each end (in our case, about 1.5" from the ends). The holes need to be placed centrally along this edge.
Our wooden dowels were 6 mm, and we used a 6 mm drill bit for the holes. Please do a test run of making these holes first on the edge of a scrap piece of MDF - to make sure that the dowel will fit into the hole snugly, but not so tight that pushing the dowel in would cause splitting. If anything, err on the side of caution and have a looser fitting dowel, rather than risking the wood splitting.
Step 5: Drill Holes Into the Base Pieces
Now you need to use the jig from the previous step to drill holes into the base pieces. I'm making 2 individual units, so I need to drill 4 holes into each of my 2 base pieces.
Each base piece needs 2 holes in each side. Make sure you place the jig on the edges of the base which will be the sides of the final unit (i.e. where the uprights will be attached).
(As seen in the photos, I placed the base piece on 2 scrap planks of wood, so that I didn't end up drilling into the floor during this step.)
Then carefully hammer the dowels into these holes.
Step 6: Sanding, Starting to Paint & Adding Screws
Lightly sand the surfaces of all of your wooden pieces with a sanding block and sandpaper, particularly the edges which will be at the front of the units. Make sure to wear a breathing mask and safety specs, and to have good ventilation.
Then thoroughly vacuum/wipe off all of the dust on the wood.
Mask the dadoes with masking tape and then paint the inside surfaces of the uprights. I did this with MDF primer.
Adding Screw Fastenings
I don't have a photo of this bit, but you can just about see in the 3rd photo above that we added 4 wood screws into the base of each unit to secure the uprights (alongside the dowels).
We used 4 x 25 mm pozidrive wood screws for this, and the holes to house these screws must be added before the units can be assembled.
So, we drilled the pilot holes (1.5 mm) for these screws through the base pieces and into the bottom edges of the uprights, then enlarged the pilot holes in the base (to make 'clearance holes'). These holes need to be in line with the dowels we previously inserted.
Then we can proceed onto the next step where we assemble the pieces together - just make sure you don't tighten the wood screws too much, as it is easy to strip the thread.
Step 7: Assembling & Painting
Then assemble the units, positioning the shelves into the dadoes, and the uprights into the dowels. Put a minimal amount of wood glue on the shelf edges going into the dadoes, and a dot of glue on the dowels (when you are happy that everything goes together as it should). We barely needed to add glue as the pieces fit so snugly.
Note that if you are making a unit which will have a hardboard backing added to it, the front edges of the shelves will need to line up with the front edges of the uprights. This will mean that at the back of this particular unit, the shelves will be recessed (to make room for the backing).
One extra step we then did was to add a tiny amount of slightly-watered-down white Polyfilla to the joins at the front of the units - where the shelves meet the uprights - and along the front edges of the shelves and the base. This was just to make a smoother look, as often MDF edges are difficult to create a smooth painted finish on.
Then we left the Polyfilla to dry and gave it a quick sand & a wipe, before applying a couple of coats of MDF primer to the narrow unit (not the wide unit - as we still have shelf dividers to add to that one first).
We mainly used a paint roller to apply the paint in order to create a smoother, more professional looking finish.
The painting is definitely the most time consuming bit of the whole process!
Step 8: Adding the Shelf Dividers
The 2 vertical shelf dividers then needed to be added to the wider storage unit.
We made a couple of lengths of scrap wood that measured 335 mm long, as this is how far the dividers needed to be placed from the uprights. We used these guides to position one divider into the unit, and then added wood glue along the top and bottom edges.
We added mitre clamps to keep it in place and left it to dry.
Then we glued the other divider into the unit - and this one needed a bit more creative thinking (!) regarding the clamping, due to the small gap in between the dividers.
We took the end pieces of our clamps and turned them around so that we could use the clamps to push outwards, rather than squeeze wood pieces together. So we used the clamps to push from one side, and the scrap wood guides to push from the other side.
Again, leave the glue to dry before removing the clamps.
Step 9: Finishing the Painting
Now that the shelf dividers have been put into the wider unit, it can now be painted in the same way as the narrow unit was.
If you haven't already, you can also (before painting) add Polyfilla to the front edges of the unit to make them smoother (refer to Step 6 if you need more info on this step).
Step 10: Adding the Hardboard Back
First make sure that the hardboard backing fits into the back of the unit. In my case, I'm only adding a back to the wider unit and have made the shelves slightly recessed at the back to accommodate it.
I had some wallpaper left over from when I decorated my craft room, so I used that to cover my backing.
I had to cut out 2 strips of wallpaper, each a bit taller than my backing. The first strip is easy to cut because you can use any part of the pattern, but make sure that the second strip you cut out is the part of the pattern that will match up with the first strip. Pattern matching between the wallpaper strips (down the centre line) is very important.
Once you have 2 strips that match up, double check that you have the board the correct way up (!), then measure and mark out the centre point of the board at the top and the bottom.
Then attach the wallpaper strips to the board so that they meet up at the centre point marks. You can use wallpaper paste or just glue to attach the paper to the backing board. Making sure the wallpaper lies flat and smooth with no bubbles
I only used wallpaper paste as I had some left over, but it was messy and awkward to use, so I would recommend glue instead - a thin layer of slightly-watered-down PVA might be the best option here.
Once the paste/glue is dry, use a utility knife or craft knife to carefully cut off the excess paper all of the way around.
I then used superglue (on the back edges of the shelves) to attach the hardboard to the back of the unit.
Step 11: Assembling the Kallax
Then it was time to put the flat pack Kallax together. However, I needed to add 4 holes to the top section of the Kallax first. This is so that I will be able to attach the supporting wood blocks onto the top later on.
I wanted the blocks as far apart as I could get them, so I positioned each block so that the face lined up with the short edge of the Kallax top. You will notice that in the photos I'm using pine blocks rather than MDF blocks for this, but that's only because we drilled the MDF blocks wrong the first time so had to go to plan B :p We also made the blocks 40 mm thick (rather than 25 mm like we planned) for greater stability.
You want the screws to go through the Kallax top, from bottom to top, and then into the centre of the wooden blocks. To make sure all of the holes are the same distance from the edges, we made a jig from scrap wood and used that to add a hole in each corner.
Note: It's important that when you are drilling these holes, you have a block of wood firmly clamped onto the other side where the drill bit will emerge, otherwise it will have a tendency to burst out and leave a mess, especially with this kind of coated wood.
You want to create 4 clearance holes in the Kallax top, and corresponding pilot holes in the 2 wooden blocks.
(Ignore the other smaller holes that you can see in the photos - they were already drilled into the Kallax top.)
I then attached this drilled top piece to the Kallax.
Don't forget to paint these wooden blocks too!
Step 12: Arranging the Units
Simply arrange the almost-completed units in the room. We're almost there!
Step 13: Attach the Blocks
Drill the screws up through the holes inside the Kallax, and up through the holes in the wooden blocks, to secure them in place.
I used pozidrive wood screws approx. 75mm long, and placed a washer on each one to protect the surface of the Kallax (because the Kallax is fairly soft and is not solid wood). Don't tighten the screws too tight.
Step 14: Attach the Tabletops
The last step is to add the tabletops. As I bought the 2 tabletops, all I have to do is attach then together to make sure they don't move apart. I'm not going to attach the tabletops directly to the units as they are heavy enough to not move easily anyway.
I cut out a couple of pieces of plywood that I already had, and drilled a couple of clearance holes in them.
Luckily the tabletops I bought already had screw plates embedded into the underside, so I made use of these. If you don't have these, you'd obviously just need to drill holes into the underside of the tabletop, making VERY SURE not to drill/screw through to the top of the tabletop! Err on the side of caution when drilling into the underside of the tabletop.
I simply chose screws that fit into the screw plates and would go only halfway through the thickness of the tabletops. I then screwed the plywood sections on (one at each end of the tabletops), so that they each straddle the central join.
Then it's time to fill your units with lovely stuff and feel so much more organised!
I absolutely love the look of the finished table, and it works so well for all types of crafting. I now have a place for all of my awkward objects, and it's exactly what I wanted! *Doubles thumbs up*
I hope you enjoyed this project, and thanks for reading :)
Step 15: A Video
In case you would like to watch rather than read, I've made a video where you can choose to watch a shorter demo or a longer & more detailed tutorial :)
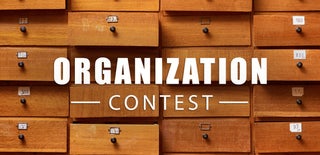
Second Prize in the
Organization Contest