Introduction: DIY Granite Slab for Leather Stamping
After completing my new knife handle (Knife Scales Instructable) I wanted to make and decorate a new leather sheath for it. As I initially attempted practice stamping on some scrap leather, I soon realized, after consulting some internet forums, that I needed a hard, smooth slab under my leather work piece to get the good impressions I wanted. There are, of course, very fine commercial marble, quartz and granite slabs available...but they are expensive and extremely heavy, which will be reflected in very high shipping costs. Since I have no idea how much I'll enjoy or maintain a leather stamping hobby, I didn't want to expend a large amount on a product I may only use a few times...so I searched for a DIY slab that I could build on my limited budget.
For the record, this is not an original idea. I found this slab concept in a forum discussion on the topic posted by a third party who did not know where or from whom the idea originated...but that it had been around a long time.
Step 1: Marble, Granite or Quartz
First and foremost, you are going to need a piece of marble, granite or quartz. If you have a good tile and flooring store, or mega hardware store, you should have no problem purchasing a thick marble tile. If they have discontinued samples, you might be able to get a piece for free. Another alternative is visiting a granite counter-top retailer/installer and ask if they have some scrap sink cut outs or small remnants. Last but not least (and this is what I did) check with tombstone makers. I couldn't procure any free scrap, but they were willing to sell me a 4X8 inch rectangular section of one inch thick polished granite for a very reasonable seven dollars.
Step 2: Other Materials
Materials list
Slab of granite or marble
Concrete paver or pavers
Epoxy suitable for concrete or stone
Mineral spirits or other cleaner
Scrap Wood
Rag or paper towels
Clamps
On thickness...you really want a minimum of two inches of combined thickness, but three inches would be better. My slab is 4" by 8" by 1" thick and my paver is 6" by 9" by 2" thick.
If, for example, you end up with a 12" x 12" x 0.5" square of marble tile, you are going to want two 12" x 12" x 1" pavers. You will need enough epoxy to laminate the two pavers together and the marble tile on top. Your epoxy needs to be thick enough to fill every nook and cranny between the layers to avoid leaving a weak area that will crack under the force of the stamping process. I chose JB Weld KwikWeld because it works well on concrete and stone, sets in five minutes, and dries dark grey. If you are doing multiple layers or larger surfaces, Liquid nails concrete silicone may be a more cost efficient choice...or even regular liquid nails.
Step 3: Clean Mating Surfaces
With some mineral spirits or other suitable cleaner, clean the surfaces you plan to epoxy. This is a good time to check the roughness of the paver and slab. My slab had a finished smooth side and an unfinished side which made it easy to decide which side went down, but your decision may not be as easy.
If your slab is exceptionally smooth on both sides, you should consider scuffing one side with 100 grit sandpaper before cleaning, and using that side as your mating surface.
After cleaning, allow the surfaces to dry.
Step 4: Mix the Epoxy
After your surfaces dry, if you are using a two part epoxy, mix it up using the manufacturers directions. Make sure you have enough to get sufficient coverage. As you can see, I have some extra epoxy just in case.
Step 5: Spread the Epoxy
The entire syringe of JB KwikWeld was the perfect amount for my 4" X 8" rough surface. Get good coverage at a thickness of epoxy that insures there are no voids between the slab and the paver.
Step 6: Mate the Surfaces
Center your slab and carefully join the slab to the paver, pushing down gently and evenly.
Step 7: Remove Excess Epoxy
With a paper towel, rag or piece of cardboard, try to remove the epoxy that is squeezed out.
Step 8: Clamp It
Using your scrap wood as a buffer, and to distribute the pressure evenly, with your large clamps secure your work firmly and allow it to cure per the epoxy manufacturers instructions.
Step 9: Cost
This is the cost of the materials that I bought for this project:
Granite slab $7.00
JB Weld KwikWeld $4.99
Paver $1.19
Total: $14.18
Living in a small town limits my options, no marble tile available nor any granite counter-top retailers. Most of you should be able to complete this project for significantly less.
Step 10: And You Are Done!
Enjoy your homemade leather stamping slab. You will find a considerable improvement in stamping quality.
Hope this Instructable was informative. Feel free to post questions, comments or criticisms
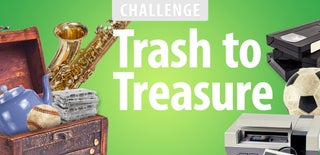
Participated in the
Trash to Treasure Challenge