Introduction: DIY-SLS-3D-Printer
In this Instruction, I want to show you how to build a DIY Selektive-Laser-Sintering (SLS) 3D-Printer. I am 17 years old and made everything by myself. Since 6 month my big dream was to build up a working SLS-3D-Printer, but there is a problem. The most SLS-3D-Printers are very expensive and only aviable for the industry. So I build my own printer. Often I was disappointed. Especially with the material, but after a month of experiments I found the right powder for a test print.
Here are some specs:
- 1W 445nm Laserdiode
- 8x8x8cm Buildvolume
- 36x54x60cm Outsidedimensions
- CORE-XY Movement
- Speed: 60mm/s tested, 300mm/s possible
- costs around 400€
### You can find a more advanced second version of the DIY-SLS-3D-Printer here ###
If you like my Instructable, please vote for me in the 3D Printing Contest :-)
Step 1: Video / Test Prints
This is my first test print with this printer.
The gear is printed in black powder coating material at 60mm/s.
It has a size of 3x3x0,5cm and took one hour to print.
Video of the gear:
Step 2: CAD-File
(If you can't see the interactive 3D model above, its probably because you're not using a WebGL-enabled browser, or you're using the Instructables Mobile app)
Here you can download the complete CAD-file. .f3d is for Fusion360, .step for other CAD-programms :
Step 3: Mechanical-Parts
20x20mm Aluminium-Extrusions:
- 4x 600mm
- 12x 500mm
- 8x 320mm
- 1x 300mm
smooth rods:
- 2x 8x500mm
- 2x 8x285mm
- 2x 8x450mm
- 4x 8x255mm
threaded rods:
- 2x M5x140mm
bearings:
- 16x F624zz bearing Aliexpress
- 2x 608zz bearing Aliexpress
belts:
- 3x (2m GT2 Belt + 2x Pulley) Aliexpress
Aluminium plates:
I found my plates at the local scrap yard, so I don't have a link for you.
Screws:
- 8x M4x40mm
- 2x M3x30mm
- 24x M3x8mm
- 8x M3x18mm
- 4x M2x6mm (Endstops)
- 200x M5x10mm DIN912
- 100x M5x10mm ISO7380
Step 4: Electric-Parts
Here are all required electronic parts for the SLS-3D-Printer:
- 1x Arduino Mega 2560 Aliexpress
- 1x Ramps 1.4 Aliexpress
- 4x DRV8825 or 4x A4988 Aliexpress
- 6x Nema 17 Steppermotor Aliexpress
- 1x 445nm 1W TO-18 Laserdiode Ebay
- 1x Laserhousing for TO-18 Laserdiodes Aliexpress
- 3x Microswitch Aliexpress
- 1x Webcam Aliexpress
- 1x Raspberry Pi Pollin
- 1x ATX-Power Supply (from an old PC)
- 2x 120mm fan Aliexpress
Step 5: Printed-Parts
Here is the part list of all required printed parts :
2x powder box.stl
2x Z-Table.stl
2x Z-Motor.stl
2x Z-Axis Top.stl
2x Piston.stl
2x Pusher-Motor.stl
2x Pusher-Idler.stl
2x Pusher.stl
4x 8mm-Rod-holder.stl
2x Motor.stl
1x Idler-Endstop.stl
1x Idler.stl
2x Y-Carriage.stl
1x X-Carriage.stl
1x X-Carriage Top.stl
2x Idler Clamp.stl
2x Belt tensioner.stl
Last change: 10.06.2016
I printed all parts with:
- 25% Infill
- 0.2mm layer
- black PLA
Step 6: Build the First Stage
What you need:
- 2x 500mm Extrusions
- 2x 320mm Extrusions
- 4x M5-Corner Bracket
- 14x M5x10mm DIN912 Screws
- 14x M5 Extrusion Nut
- 8x M5x10mm ISO7380
At first you attach the two Z-Motor printed parts to your base frame. Then you add four M5-Corner brackets to the frame
Step 7: Build the Pistons
What you need:
- 4x small wood plates
- 3x big wood plates
- 12x wood dowels
I build my pistons out of screen printing plywood, because it is very easy to work with wood. Also it is very cheap :-). An other plus point is that the surface is very smoot, which is better for the piston.
I use some wooden dowels to connect the woodplates to eachother.
I recommend to download my Fusion360 that you can cut the plates very accurate.
Also please look at my additional PDF:
Attachments
Step 8: Connect the Wooden Box to the First Stage
What you need:
- 4x M5x25mm DIN912 Screws
- 4x M5 hex nut
- 4x M5 washer
Now you can screw the wooden box to the first stage. Use some washers for the M5x25mm screws.
Step 9: Build the Second Stage
What you need:
- 2x powder box printed part
- 2x Z-Axis Top printed part
- 4x Cornerbracket M5 Nut
- 22x M5x10mm DIN912 Screws
- 22x Extrusion Nut
- 2x 500mm Extrusion
- 2x320mm Extrusion
The main frame of the extrusion is very similar to the frame of the first stage. The only difference between them are the printed parts. For the second stage you need the powder box and the Z-Axis top parts. Connect the parts like in the pictures
Step 10: Pusher
What you need:
- 1x 300mm Aluminium Extrusion 2020
- 2x Pusher printed part
- 4x LM8UU
- 6x M5x10mm DIN912 screws
- 6x M5 extrusion nut
At first you have to push the 300m Extrusion inside the printed part. Then you connect the extrusion with six M5 extrusion nuts. Before pressing the LM8UU inside the printed part, please predrill the printed part with a 15mm drill.
Step 11: Connect the Second Stage to the Wooden Box/ Install the Pusher Motors
What you need:
- 2x Nema 17 Motor
- 2x Pusher Motor printed part
- 2x Pusher Idler printed part
- 8x M3x8mm screws
- 12x M5x10mm DIN912 screw
- 2x 608zz Bearing
At first you have to connect the second stage to the wooden box like the firts stage. You simply use four M5x25mm screws. Then you can attach the pusher motor printed part to the second stage. You screw the printed part to the extrusion by using three M5x10mm DIN912 screws. For the Nema 17 motr you use four m3x8mm screws. Once you screwed the motor to the printed part, you attach a 20th GT2 Pulley to the motorshaft. At the other end of the second stage, you attach the pusher Idlers printed parts. Then you push an 608zz Bearing inside the printed parts. This is necessary for the 8mm smooth rod, which will be insert later.
Step 12: Install Z-Axis
What you need:
- 2x Nema 17 Motor
- 2x Z-table printed part
- 8x M3x8mm screws
- 8x LM8UU
- 2x 8x255mm smoothrod
At first you need to press the LM8UU Bearings inside the Z-Table printed part. Then you simply insert the Z-Table with the LM8UU into the 8mm smooth rods.
Step 13: Pusher
What you need:
- 2x 8x500mm smoothrods
- 4x 8mm Rod-holder printed part
- 8x M5x10mm DIN912 Screws
- 8x M5 Extrusion Nuts
Now you finished the pusher and the pistion unit for the SLS-3D-Printer. So now you can attach them together. You simply need to push the smooth rods trough the pusher bearings. Then you can screw the smooth rods to the second stage.
Step 14: Y-Carriage
What you need:
- 2x Y-Carriage
- 4x M4x40mm DIN912 Screws
- 8x F624zz Bearing
- 8x M4 self locking hex nut
- 4x M4 washer
- 4x LM8UU
This is the first step for the X/Y linear Laser movement. The X/Y Movement of this printer based on CORE-XY. If you don't know what COREXY is, please visit the this website COREXY. The Belt is appropriate on different levels, so the belts don't rub to eachother. The big advantage of COREXY is, that the weight of the moving mass is lower than conventionell cartesian movement systems. This means that you can drive extremly fast, because you don't need so much force to accelerate the mass. I've tested 400mm/s on my printer :-)
To build up the Y-Carriage, please take a look at the pictures. Don't forget to screw the F624zz bearing on different levels. Later this will be very important.
Step 15: Idler
What you need:
- 2x Idler Clamp printed part
- 1x Idler printed part
- 1x Idler with endstop printed part
- 8x F624zz Bearing
- 4x M4x40mm DIN912 Screw
- 8x M4 self locking hex nut
- 4x M4 washer
Like in the step before. Don't forget to screw the F624zz bearings on different stages that the belt don't rub to eachother.
Step 16: X/Y Motor
What you need:
- 2x Nema 17 Motor
- 1x X-Motor printed part
- 1x Y-Motor printed part
- 8x M3x8mm Screws
- 2x GT2 20th pulley
You need to repeat this step two times. The only difference is, that you use for one the X-Motor-printed part und the other one Y-Motor printed part. Also you have to turn the GT2 pulley of one motor in 180°.
Step 17: Attach the Third Stage
What you need:
- 2x 8x450mm smoothrods
- 2x 8x285mm smoothrods
- 4x LM8UU
- 12x M5x10mm DIN912 Screws
- 12x M5 Extrusion Nuts
Now you can combine the Y-Carriage, Idler and Motor with the third stage. You push the the smoothrods inside the defined holes. Now you need to screw the X/Y Axis to the third stage. Use the twelve M5x10mm screws to connect the Motr and Idler printed part to the extrusions. Don't forget to insert four LM8UU for the X-Carriage.
Step 18: Attach the X-Carriage / Last Stage
What you need:
- 1x X-Carriage printed part
- 4x belt tensioner printed part
- 4x small metal pin
- 8x M3 hex nut
- 2x 2m GT2 Belt
- 8x M3x18mm screws
- 2x 500m Extrusion
- 2x320mm Extrusion
At first you have to install the last stage of extrusions. You simply have to install it like the other extrusions before. After that you can attach the X-carriage to the LM8UU Bearings. You simply have to push them inside the printed part. Then you fix the X-Carriage with four zip-ties. For the Belt you have to put an small metal pin inside the Belt-tensioner. Then you can tighten the belts with the M3x18mm screws. Make sure that your belts have the same lenght!
Step 19: Build the Piston
What you need:
- 8x M5x25mm screws
- 8x M5 Hex Nut
- 4x Aluminiumplates (12x14cm)
- 8x M3 hex nut
- 2x packing material (From your mechanical parts or etc.)
This step is one of the most important ones, because the pistons are the heart of the printer. I made a lot of experiments, how to make a good piston. So this is my solution :-)
I am using an aluminium || packing material || aluminium sandwich as a piston. You have to cut the packing material so that it will press itself to the wooden box. The result is that no powder will fall through the piston. You can level the pistons by pressing the aluminium plates together.
Step 20: Install Small Extrusions to the Pusher
To garanteer that all the powder will push inside the next piston, I attached some small 10x10mm Extrusions. Make sure, that the pusher can move freely. The space between pusher and extrusions should be <1mm.
Step 21: Install the Laser
What you need:
- 1x Lasermodule
- 4x M3x10mm DIN912 screws
Now can can screw the lasermodule to the X-Carriage. You do that by using four M3x10mm screws. Once you installed the laser, make sure that you are not static charged and touch the lasermodule. The laserdiode is a very sensitive element and can break easily.
Step 22: Outsite Plates
Now you can attach the Aluminium plates for the housing by using some M4x6mm screws. I'am using 1.5mm Aluminium plates for the housing. It is highly recommend to download the Fusion file from the the Top, so you can cut your plates in the exactly dimensions.
Step 23: Powersupply
You can use nearly every ATX-PSU which has a 12v Output. The printer needs all in all less than 100w of power, so you don't need a strong powersupply, but If you want to change later to an heated piston I recommend not to buy a ATX-PSU. Search on Ebay for server powersupplies. Mostly they are cheaper and have a lot of amps on the 12V Line.
Step 24: Arduino / Ramps 1.4
The Ramps 1.4 is one of the most used electronic boards in the reprap community. It is very cheap and it can be used for many projects. I marked on the picture, where you have to plug your wires that it will work.
Step 25: Laserdriver
If you build your own Laserdriver, I recommend a LM317 constant current circuit. It is cheap and can provide max. 1A for the Laserdiode. You can calculate the current for the laserdiode with this formula: [ I = 1,25 / R1 ]. I'am using an 1,5 Ohm power resistor, so I provide max 0,83 mA for the laserdiode.
I attached a circuit drawing with all the requierd electronic parts (see pictures)
Step 26: Repetierhost
In my opinion Repetier-Host from Repetier the best all in one Software for FDM-3D-Printer. With some modifications you can also use it for my DIY-SLS-3D-Printer.
You don't have to modify Repetier-Host, beacuse it is just a host software, you have to modify the arduino code and the gCode-generator, that it will work.
Step 27: Arduino-Firmware
To controll the SLS-3D-Printer, I'am using a modifed Repetier-Firmware from Repetier.
This firmware has an feature, that overrides the E-Steps of your Slicer to an Laser, called "Laser-Mode". That means that I can use normal FDM-Slicers like Slic3r for generating the Gcode for my printer.
You can upload the config.h to the Repetier configuration tool . Then download the complete firmware, open it in your Arduino IDE and upload it to your Arduino mega 2560.
Once uploaded, go to Repetierhost-->Config-->Firmware EEprom Configuration.
Then you upload my default Eeprom file, which includes all the parameters like steps per mm, acceleration, feedrate...
You can download my default configurations here:
Attachments
Step 28: Modify Slic3r
I'am using Slic3r to generate the Gcode, because it has some features like custom Gcode on layer change, which is very important for my DIY SLS 3D-Printer, because I need an custom Gcode for the powder pusher.
Slicer is allready included in Repetierhost, so you don't need to download slic3r as a standalone programm.
You need to open the Slic3r configuration. See pictures, where you have to click
Then you go to -->Printer Settings--> Custom G-code:
Here you type in:
Start G-code
G28 // home all axis
M3 S50 // acctivates the Laser with a power of 50 from 255
End G-Code:
G28 X0 Y0 // home X- and Y-axis
M84 // disable motors
G204 P0 S0 // disable extra Motor for the powder pusher
After Layer change G-code:
G202 P0 X0 // move extra Motor for the powder pusher to 0mm
G201 P0 X300 // move extra Motor for the powder pusher to 300mm
G201 P0 X0 // move extra Motor for the powder pusher to 0mm
( //... = comments, to understand the custom Gcode)
For the other configurations, please download my slicer config file:
Attachments
Step 29: Make Your Print Material
Normaly SLS-3D-Printers printing with Nylon Powder like PA12 which is very expensive. It costs around 200€/kg. This is too expensive for me. If I would fill my buildvolume of 8x8x8cm with PA12. The Material would costs more than my complete printer. So I searched for untypical Materials, which can be sintered, like powder sugar. I mix the powder sugar with some carbon powder, but I had no success. The sugar clumps into small drops (see pictures) und doesn't create an flat surface.
So I've been searching for an other material. Accidentally I found black powder for powder coating on Ebay. It has better characteristics than I expected. I can print the material without a heated bed and with just 200mW laser power at 60mm/s. This is great, but not perfect. The disadvantage of this material is, that it is not very rigid. It breaks easily. But for test prints it is ok.
I think it will work with a material like nylon or an other thermoplast when I add a heated bed, because everything else works nearly perfect (electronics, mechanics, laser...)
If there is someone out there, who has some Ideas about a new material which is inexpensive and can be sintered, please let me know. You would help me a lot.
Step 30: Safety First!!!
Lasers are very dangerous and can make you blind. Don't work without safety glasses!
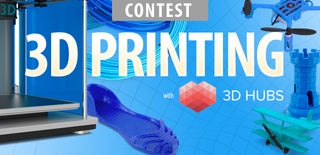
Grand Prize in the
3D Printing Contest 2016
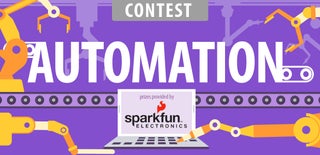
First Prize in the
Automation Contest 2016