Introduction: DIY Tool Chest With Shallow Drawers
I had tried different ways of storing tools and parts and finally decided that a chest of drawers with shallow drawers would be the best solution. Stuff is completely hidden till you pull the drawer out and you can find the right part or tool at a glance. I started off thinking of making 8 foot wide drawers but the thought of moving such a brute was scary so decided to go with a 4 foot wide drawer chest.
The chest is about 3 feet high, 50 inches wide and about 24 inches deep. Pretty capacious!
I also wanted it to look a bit antique-ish so finished it the same way that I did my folded horn speakers.
Step 1: Making the Sides for the Chest of Drawers
The sides of my chest of drawers were shelves from a wall unit that I got from a freecycler. These are oak veneered high density MDF like material.
I added a 3 inch oak extension (also from another freecycler - wooden flooring) with biscuits and glue to the bottom of each side panel (biscuits are wooden ovals that are placed in a slot cut into the wood, the ovals connect two the pieces of the wood).
The MDF panels are reinforced with oak molding (from the wall unit) which were glued and screwed to the MDF.
Step 2: Making the Drawers
The size of the drawers were dictated by the free panels I had for drawer bottoms. I had got perforated hardboard panels (pegboard) from another freecyler who had used them on the walls of his garage. These panels were precut to 4 feet by 2 feet and some of them had small cutouts for switch plates, etc. So the drawers would have to be 4 feet wide and two feet deep.
I decided to keep each drawer shallow, making it is easy to find stuff without it getting buried in deep drawers.
For the chest I went with four drawers that were 2 inch deep, three that were 3 inches deep, two that were 4 inches deep and one that was about 5.5 inches deep. A total of 10 drawers.
I had leftover pieces of sheet goods from various projects so tried to use as much of that for the drawer sides. The 3/4 inch scrap wood pieces were cut into strips of 2, 3, 4 and 5.5 inch widths. And then cut to 24 inch and 46.5 inch lengths.
The drawer sides were attached with glue and screw using simple butt joints. The joints were kept square by using a manufactured drawer box (yes, from another freecycler) that was exactly 90 degrees to assemble the sides.
Drawer bottoms were glued and screwed onto the drawer sides on top of a Hardieboard panel. The Hardieboard has lines etched into the board which help align the drawers and keep them square.
Photographs show the assembly process and at the end a set of 10 drawers that are in the process of being stained.
Step 3: Assembling the Chest (cabinet)
Had not saved photos for the first part of the assembly of the cabinet for the chest of drawers. The drawing show how the assembly was done. Full extension drawer slides purchased from an ebay vendor were attached to the side panels. These side panels were then bridged with two 2x4's on the bottom, an oak strip at the top front, and a 12 inch wide plywood panel (leftover from my speaker project).
The back plywood panel was attached with glue cabinet bolts and screws. The carcass was then strengthened by gluing and screwing pergo floor panels (from freecyclers again) to the back.
The chest was flipped onto its back and a 12 inch by 2 inch wood joist, that was trimmed to 9 inches, was attached to the top with metal joist hangers. Pergo panels were attached to the bottom of the 9 x 2 x 50 inch wooden slab to hold the other two wooden slabs that I would attach later to the top.
An additional oak strip was attached to the front to tie the two sides together.
Caster wheels (from a Harbor Freight dolly) were attached to the bottom 2x4s and cross beams from 2x4s were screwed to the bottom beams.
Step 4: Making the Counter Top
The chest was flipped upright and the two remaining wooden slabs for the countertop were added with biscuits and glue.
First the front slab was biscuited, glued, and clamped. The glue was allowed to completely cure and then the back slab was glued and clamped. Heavy buckets were placed on the top to prevent the wooden slabs from bowing.
Long screws were also used to screw the top slabs into the sides of the chest. Hopefully, the natural movement of the slab from changes in temperature and humidity won't tear the whole thing apart.
Step 5: Finishing the Chest of Drawers
The countertop was completed by attaching a 2x4 was attached to the back of the wooden countertop.
All the drawers were reinforced with a wooden strip that was attached to the sides and the drawer bottom to prevent the drawer bottom from sagging. This wooden strip divided the drawer into half.
The drawers were painted with black acrylic paint diluted with water.
Drawer slides were attached to the sides and the drawers were slid into the mating slides in the cabinet. Two holes were drilled into the front panel of each drawer so that the drawer front could be attached later on.
For the drawer fronts, oak strips were glued to a 4x4 foot sheet of oak plywood from Home Depot. The sheet was stained and then the first (topmost) drawer front was cut to measure.
The first drawer front was attached to the topmost drawer by keeping a 1/8th inch strip below the top edge and the top of the drawer front for a gap. The drawer front was held temporarily with clamps and then screws from the inside were used to attach the drawer to the drawer front.
The second drawer front was then cut from the sheet to fit and attached as above with the 1/8th inch strip ensuring a gap between the first and second drawer.
The procedure was repeated till all the drawer fronts were attached.
Drawer handles that I had picked up from my parents house in India were attached to all the drawers.
Molding was applied to the side panels (top and bottom) and to the front of the cabinet. The pieces were stained and let dry.
The last picture shows that the bottom molding strip still has not been attached.
Step 6: In Use ...
Am amazed at how simpler my workshop experience has become with these drawers. They have an incredible capacity - most of my fasteners, fastening tools (screwdrivers, screw driver bits, nut drivers, etc.), cutting tools (chisels, scissors, drill bits), clamps, wood scraps, wall wart powersupplies and power cords, and hardware (wheels, knobs, ...) fit in these set of drawers.
Highly recommend building these type of shallow drawers instead of tool storage on walls, etc. The drawers keep the dust away. You find things at a glance. And did I mention the overall capacity!
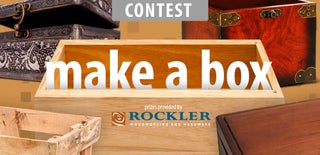
Participated in the
Make a Box Contest