Introduction: Desktop Racers - 3D Printed Pull-back Racers
In this Instructable, we'll be looking at how to create a custom, 3D printed, pull-back car. With it's fairly small size, it makes a great desktop toy and can be fully customized for racing with others. They only require a 3D printer, some support removal tools (eg pliers) and a rubber band to work properly.Firstly, we'll take a look at the mechanics behind the cars and then on to how to build your own, either with 3D modelling software or with the provided .stl files.
Required for this project are:
1) A 3D printer
2) Support removal and finishing tools
3) 1 Rubber Band
For further customization the following may be required:
1) Paint
2) Silicone or large diameter rubber tubing
3) Extra Rubber Bands
Step 1: How It Works
The motion of the car depends on the contraction of a rubber band. The band is anchored to the chassis of the car at one end, and the other is wound around the axle by the "gear".
When charging the car, by pulling it backwards, the rubber band winds around the front axle.
When released, the rubber band contracts, unwinding itself from the axle and forcing it to rotate, making the car drive forward.
How I came up with the design
I came up with this idea after designing a wind-up rubber band motor. It made use of winding a rubber band around itself to rotate one end of a cylinder. The problem with the motor was that it would take a long while to wind up and that it would spin forward and backwards when released, making any car I made go backwards a little. After a bit of thinking, I came up with using a "gear" that would unwind with the elastic band. This gave the car a decent bit of momentum and it would keep going in one direction. The only problem was that by having the rubber band wind around the back wheel meant it had to be reset across the top... right where the shell would be. So I flipped the chassis around and make the band go underneath the car, making it easier to reset once made.
Step 2: Designing Your Racer
When designing your own car in 3D modelling software, you'll need to consider:
Wheel size
Rubber Band size
Frame shape
Why?
The size of wheel must be bigger than the "gear" that holds the rubber band to stop the teeth hitting the ground. The size of rubber band that you choose to use may mean the distance between the anchor and the front axle may be bigger or smaller. The shape of the Frame will also determine how any car "Shell" fits on to the chassis to give it better aerodynamics or just to make it look like a proper car. Also bear in mind how the axles will fit onto the chassis. In my design I created a "press-fit" socket that would allow the axles to be pushed in, but stop them from falling out. A cut was made, just smaller than the diameter of the axle, into the top of the socket so that with a little force, it could go in, but the dimensions would prevent it falling out
Creating a Shell
Once you've modelled you chassis, you should incorporate "pins" that will hold on to an outer shell for a better appearance. A few raised cylinders along each side is enough to give a decent hold, and they can be glued together once printed.
The Shell itself can be anything you want it to be. Go wild. You can model it to look like a supercar, a truck, even just a platform for carrying light objects across the table. Whatever you can design, as long as it fits onto the chassis and leaves enough room for the wheels and gear.
If you're printing my version, the orthographic image shows the dimensions I used (in mm) if you want to build a custom shell around that.
Once the modelling stage is complete, it's on to the printer.
Step 3: Print the Parts
Normally, I'd print these parts with a layer height of around 0.250mm with a raft using PLA, but the model should come out decently on normal settings of 3D printers. When printing the shell, the layer height can be reduced to give it a smoother look, but can be sanded smooth either way.
Once printed, as much support should be removed as possible as some parts fit quite tightly.
Unfortunately my usual printer has run out of filament and won't be getting some for a while so I can't get decent photos of the finished print.
Step 4: Assemble and Fit the Rubber Band
Once the parts are printed and the support removed, it's ready for assembly. Firstly, the axles should be able to press-fit into the sockets. If not, sand very lightly and carefully to avoid them becoming too loose and try again.
Bear in mind, the gear should be on the front axle of the frame, the part with the flat edge on my model.
The Elastic band is then looped around the central stud and passed under the chassis by pulling it through the slit before being latched to the gear.
The axle should then be able to wind backwards, and then be propelled forwards by the rubber band. Once unwound, the rubber band should still be on the underside of the chassis, making it easy to reset the rubber band over the gear
The shell will then be able to fit on top of the studs and glue on or clasp depending on how you model it.
Step 5: Completed, What Now?
With any luck, you'll have you own car similar to the picture above, that you can wind up again and again. But that's far from the end of the story. You can go on to upgrade your car with some simple ideas:
Give the car some racing colours with paint
Try creating rubber wheels to give the wheels extra traction (large rubber tubing? Silicone rubbers?)
You could add more rubber bands to the car to give it more power
Try 3D printing custom wheels to see if it improves performance
Not driving straight? Will angled wheels help? What does adding weight do? What difference does winding the band around the back axle instead make?
Get creative
And most of all:
Have fun
If you liked this project, be sure to vote for it in the contests, and feel free to ask any questions.
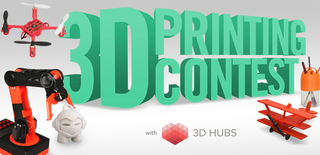
Participated in the
3D Printing Contest
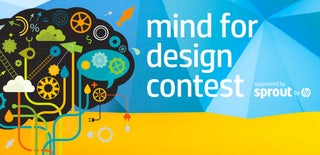
Participated in the
Mind for Design

Participated in the
Move It