Introduction: Edison Bulb Dome Lamp
A while back, I came across this style of lamp during my stumbles across the internet. I stored the idea in the back of my mind until I eventually found myself with access to a CNC router, at which point I pretty much had to figure out how to make one. Unfortunately, I finished the project before deciding to document it, so work-in-progress images are a bit sparse (oh noes!). I absolutely love this lamp though, and hopefully this instructable can you help you to enjoy your own project just as much! :D
Step 1: Materials (Components)
- A piece of 3/4" thick wood
- You'll need enough material for two 6" diameter circles (for the lamp shown). Also, I used pine, but you can use whatever wood you prefer
- Lightbulb
- This is the main element of the lamp, so spend some time making sure you pick out a bulb you really like. I ended up selecting an Edison style bulb with a Marconi filament.
- Light socket set
- A brass finish is easy to match with hardware later on, and looks great. Also, I didn't want it to look like you should remove the glass dome to turn the lamp on or off, so I chose a socket without a built in switch.
- Glass dome
- more on sizing this piece in the next step
- (Optional) rayon-covered wire and antique style plug
- Not necessary, but it certainly matches the bulb
- 2" long 1/8-IP size nipple
- Use 1 1/2" if you want the socket to be flush against the base
- 2 flat washers
- 1 lock washer
- 1 hex nut
- Ensure all hardware is for use with 1/8-IP nipple
- (Optional) 1/8-IP Coupling
- Used as a decorative spacer to cover the threaded exterior of the 1/8-IP nipple
- 1 DPDT slide switch
- 2 wood screws (sized to fit switch's mounting features)
- Extra 18 AWG wire (internal to the lamp, so doesn't have to be decorative)
(I personally got the glass dome from collectingwarehouse.com; the bulb, socket, wire, and plug from 1000bulbs.com, and the rest of the parts from my local hardware store)
Step 2: Materials (Tools/Equipment)
- CNC router
- It is important to note that access to this equipment can be replaced with a saw, manual router, and woodworking knowledge. I'm still new to this sort of project though, and trust my ability with CAD/CAM software and CNC equipment more than my ability with traditional tools
- Soldering-iron and solder
- Heat shrink tubing
- Wire strippers
- Needle-nose pliers
- Wood glue
- C-clamps
- Wood stain
- Clear protective wood finish
- Brush
- Medium grit sandpaper (~60 grit)
Step 3: Initial Design (Sizing Components)
Before we can start making anything, it's important to make sure it's all going to fit together.
The first step is choosing an appropriate size glass dome. The size of the dome depends on dimensions of the bulb and socket chosen and the desired space around it.
Edison bulb: 2.625" diameter x 5.3125" height
Light Socket: 1.5" diameter x 2.25" height
I decided that I wanted the distance between the bottom of the lightbulb and the lamp base to equal the distance between the top of the bulb and the top of the glass dome. Since I also wanted 1/2" clearance between the light socket itself and the base, this means the total height will be about 2.5"+5.3125"+2.5"=10.3125" (I rounded up to 11" to give the bulb more space). Next, I wanted the height-to-width ratio of the dome to equal that of the bulb, so the following equation gave me the proportional dome diameter:
Diameter / 11" = 2.625" / 5.3125" ----> Diameter = 11" x 2.625" / 5.3125" = 5.435"
From this, I knew to get a glass dome with a height of 11" and a diameter of 5.5" (which is, fortunately, a standard size).
Next, having the diameter of the dome allows us to determine final dimensions for the two base pieces. It's important to note that since the dimensions of the dome weren't posted on the website I purchased it from, I decided to wait until it shipped to measure its wall thickness and determine whether 5.5" was the inside or outside diameter. It turns out that the 5.5" diameter measures to the wall center, which has a thickness of about 1/32". Additionally, the following component dimensions were important to finish dimensioning the base pieces as shown in the images.
Switch: 1.375" x 1/2" face plate, 7/8" x 1/2" body
Wire: 1/8" x 1/4"
I/8-IP Nipple: 3/8" OD
Once all the dimensions are taken into account, you can use Coreldraw (or whatever software you prefer) to create the vector drawing needed for the CNC machine from the dimensions attached (with any alterations for different components you use). That is, of course, unless you plan on doing it manually, in which case you do your thing! :P
Step 4: Cut and Prep the Base Pieces
If you plan on using a CNC router, as I did, I assume you have some familiarity with the equipment, so this will be more of a reminder. First, you take the two vector file images created at the end of the previous step (one for the base and one for the top) and use CAD/CAM software to turn it into the appropriate file format for the machine you will be using. From personal experience, make sure you extend the cutouts in the base beyond the edges of the circle so that the edges are cut completely. Next, set up the material on the machine bed and secure it either using wood screws (placed in the corners so they're out of the way) or a vacuum table (if the machine is equipped with one). Finally, put a 1/4" bit on the machine, perform a trial run above the material (to make sure the tool path looks correct), and then cut the pieces out!
At this point, the edges may look a bit rough, like in the attached image. Use sandpaper to smooth the pieces a little bit, but keep the outer edges a bit rougher (it'll give the base more character later). Now, use a brush to apply wood stain following the instructions provided. Do this on all sides of the pieces except the upper face of the bottom piece and the lower face of the top piece (this will need to be glues together later). Finally, after allowing the stain to dry, apply the clear protective finish to the same faces.
Before adding the wiring, it's time to assemble the mounting hardware around the hole in the top piece. Put the 1/8-IP nipple through the hole in hole in the center, and assemble the following parts in order:
hex nut - lock washer - flat washer - wooden top piece - flat washer - 1/8-IP coupling - socket base
Step 5: Assemble the Electronics
Before we continue, I'd like to apologize for my terrible drawing, but I hope it gets the idea across.
Now, there are a few important things to know for wiring up the circuit. First, on most electrical wires the neutral path will be marked in some way, usually with ribs along the length of it (the hot path, on the other hand, will be smooth). Use that to keep your wiring straight. The image at this link (http://hostedmedia.reimanpub.com/TFH/Step-By-Step/FH05NOV_WIRSOC_01.JPG) shows how to wire up the socket and how to tell which end is which on the plug. Also, the inside of the plug also has screw terminals, much like the socket. Lastly, if you are using a different switch, make sure you understand how its terminals connect internally; you may have to wire it slightly differently.
You should have two wires, one longer wire to connect the switch to the plug, one shorter wire to internally connect the socket to the switch. Use the wire strippers to remove the sheathing from the ends of the wires. For the long wire, open the plug and screw one end to the appropriate terminals, then solder the other end to the switch as drawn in the diagram (put heat shrink tubing on this end before soldering it to the switch, so you can then use a blowdryer to shrink the tubing over the solder joints). Next, feed the shorter wire through the socket base and hardware assembly you attached to the top piece, solder one end to the switch as drawn (with heat shrink tubing again), and screw the other ends into the socket (remembering to first add the underwriter's knot).
At this point, you can screw the lamp into the socket and plug in the circuit to make sure it works! If something is wrong, make sure you followed the ("expertly drawn") diagram attached, check that your switch works the same as the one I've shown, and if all else, let me know and I'll do my best to help.
Step 6: Assemble the Base and Finishing Up
We're getting close now!
Take the long wire, place it in the shallow 1/4" thick trench in the bottom piece, and either glue or staple it in place (being careful, if you choose to staple it, not to puncture the sheathing with the staples). Make sure there is enough room for the switch to mount where it is intended to go (with a little additional service length).
Now, glue the top to the bottom! Put glue on each face and clamp the two together. Once the glue is dried, use sandpaper to remove any dried glue that was pushed out the sides. Using two wood screws, screw the switch into place, then add one last coat of the protective finish (this will make any gaps between the two pieces less apparent).
All you have to do now is screw the bulb in and place the glass dome over the top of the assembly!!! (Just as a note, you may want to use some windex to clean the dome if, like me, you managed to get fingerprints all over it)
Step 7: You're Done!
YAY!
Now put your new lamp somewhere nice and enjoy it! :D
This is my first instructable ever, so if there's anything I can clarify or improve on, please let me know.
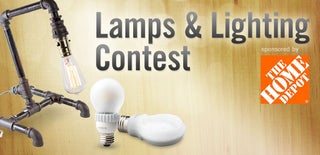
Participated in the
Lamps and Lighting