Introduction: Complete Overhaul of Vintage Signal Generator
I acquired an Eico 320 RF signal generator at a ham radio swap meet for a couple of dollars a few years ago but never got around to doing anything with it until now. This signal generator has five switchable ranges from 150 kHz to 36 MHz and with harmonics, is usable up to 100 MHz. The unit has a 400 Hz test tone which can be switched in and out. There are two old-fashioned "microphone" connectors on the front. One is for the 400 Hz test tone which has a potentiometer that allows the output adjustment of the 400 Hz tone from 0 to 20 volts RMS for testing audio circuits. The modulation level isn't adjustable but the RF output is, with the potentiometer being right beside the RF output connector.
The Eico model 320 (Electronic Instrument Company) came out in 1956 and was manufactured into the 1960s. My unit was probably made in 1962 as the tubes are original Eico tubes and have a date of manufacture as late 1961. The chassis was in good condition inside but had bad solder joints everywhere. The only work that had been done since it was assembled was the replacement of the filter capacitor. Also a very crude soldering job.
I figured that the unit was a good candidate for an overhaul and modernization as the tubes were strong and the chassis clean.
Step 1: Take Unit Apart for Inspection
The signal generator comes apart very easily with only slot type screws in the front. Once the screws are removed the chassis and the box come apart. This unit has had the handle removed. Probably done because the original owner wanted to mount something on top of it. The surface of the chassis and the inside were extremely clean with the cadmium coating still intact. The tubes were clean and there was no dust to speak of anywhere. Considering the signal generator's age, it was in amazingly good condition.
I checked the plug, cord and input transformer for shorts using an ohmmeter. I did a quick check of the filter capacitor with an LCR meter and the capacitor value was close to the rating on the can. After I was satisfied that the unit would be safe to plug in. I turned it on and checked for any output, by trying all bands with a scope attached. There was none. I checked the voltage on the filter capacitor and it was around 215 VDC. Even though it was OK, I decided to replace it.
All the capacitors would need to be replaced, the front microphone connectors would need to be replaced with modern BNC connectors and all the switch terminals cleaned with a pencil eraser and/or liquid contact cleaner.
Step 2: Study Schematic Diagram and Explain Circuit
The schematic is fairly straightforward with an AC power supply connected to an isolation transformer. There are two .1 uF capacitors that connect each side of the line to the chassis. This provides a path for noise from the hot side of the line to neutral preventing it from getting into the generator. (Out of curiosity, I took the .1 uF capacitors off and checked the AC voltages between the hot and neutral to the chassis. One voltage was 215 VAC and the other was 115 VAC. With the capacitors connected the voltages were equalized at approximately 14 VAC. The capacitors also provided an additional safety feature to any person working on the generator. Best to never get too confident when working on tube equipment as there are lethal voltages everywhere).
The transformer feeds the 6X5 full wave rectifier tube which delivers approximately 330 volts to the first resistor that forms an RC filter with the filter capacitor and second resistor which feeds the 6SN7 tube with approximately 100 volts on the plate. The voltage on the filter capacitor is approximately 217 VDC. The anode of that part of the tube is at RF ground through capacitor C2. One half of the 6SN7 twin triode is configured as a type of Armstrong or Tickler coil oscillator. Each switchable coil has one end tied to ground while the top is coupled via capacitor C11 to the control grid. The DC voltage of the control grid is set by 100K resistor R1 which ties it to the cathode. The taps on the coils are tied directly to the tube cathode. Below this, the cathode has a 10K resistor in series with a 10K potentiometer where the signal is taken out of the wiper through capacitor C7 to the RF out terminal while the bottom end of the potentiometer is connected to ground.
The 400 Hz oscillator utilizes half of the 6SN7 twin triode where it is configured as a Hartley oscillator. The coil has two capacitors in series across it and the point where they meet is tied to ground. R4 is the 20 ohm cathode resistor and R3 is the grid resistor. C3 acts as the grid capacitor. SW3 connects the plate of the tube to L6 and B+. This switch also connects the output of the Hartley to the plate of the other oscillator, allowing it's output to be modulated by the 400 Hz signal. At this point, the audio is also taken off and applied to the audio output potentiometer and output BNC terminal.
Step 3: Replace Line Cord
I replaced the line cord with a more modern one. Since there is an isolation transformer, it doesn't matter which way the line cord is connected. It is important to tie a knot in the cord so that it will not put any strain on the soldered terminals when pulled.
Step 4: Replace the Microphone Connectors With Chassis Mount BNC Terminals
Since the output connectors were of the old-fashioned microphone type, I thought it would be practical to change them to the near universal 50 ohm BNC type. This was an easy job as the holes were of a standard size that the BNC connectors would fit in with no modifications.
Step 5: Take Out Coil and Capacitor Section by Removing Two Screws
The coil and capacitor section comes out when you remove two screws on the top of the chassis. The two wires that connect to pins 4 and 6 on the tube socket need to be unsoldered. The band and frequency selector dials must be removed, plus the dial marker. All these come out with set screws in the dials themselves. Once the section is removed all the solder terminals on the coils and variable capacitors should be redone and the selector switch should have the connections cleaned with contact spray cleaner and/or a pencil eraser. Once these things have been done, put the section back in and resolder the terminals.
Step 6: Replace All Capacitors
Replace all capacitors with the same values but with the same or higher voltage rating. The power supply electrolytic should be replaced with the same voltage rating but with same or higher capacitance. I didn't have an axial electrolytic capacitor so I mounted it in place with a bit of hot melt glue and I put a piece of electrical tape over the terminals for safety.
Step 7: Resolder All the Terminals
Once the capacitors have been replaced, check to see if there are any connections that haven't been resoldered. Once this has been done, it's time to fire the unit up and see how it works.
Step 8: Checking Output Waveforms and Calibration
I have taken three examples of the waveforms out of the signal generator. One at 200 kHz, the second at 2 MHz and the last at the highest frequency of 33 MHz. In each image is a text box showing the first six harmonics and their levels in dB. The green waveform is the actual oscilloscope waveform and the blue one is the spectrum analyzer display showing the fundamental frequency on the left and the relative levels of harmonics going to the right. The waveforms are relatively clean with all the harmonics at least 20 dB down from the fundamental. The highest band relies on the harmonics of the fundamental to give useful signals up to around 100 MHz. I verified this by putting an FM radio nearby and could hear the presence of the carrier by the "quieting" of the receiver or the reduction in the sound of the background noise at a clear frequency around 100 MHz. At this time the generator can be calibrated by loosening the set screw in the pointer and moving it to the same frequency as is shown on an accurate radio (preferably with a digital display). The set screw can then be tightened down. I found this method to be more useful than that provided by the trimmer capacitor. If the trimmer capacitor is adjusted, the frequency drifts when the metallic case is put back on due to the capacitance of the case. A more accurate way is to have the metallic case almost completely on and adjusting the set screw with a long screwdriver when moving the pointer to the right frequency.
This generator has now been brought back to life and is now a useful piece of test gear which otherwise would've been stripped for parts or sent for recycling.
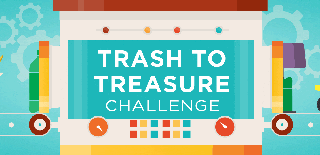
Participated in the
Trash to Treasure