Introduction: Fascinating Wooden Bowl Using Steam Bending in a Microwave
I am very interested in creating designs on my desktop cnc that make perfect usage of a given material when going into the third dimension. A full 3d relief cut seams a unbelievable waste of material and time. So most of my designs rely completely on 2d operations giving the opportunity to use a laser cutter or – in some cases – even a water jet.
After releasing the first version of my "Bend Spiral Bowl" on Thingiverse I got some pretty harsh comments on how difficult the built was for some readers. So I took some time to improve my design concept and after several prototypes I came up with the idea of bending the wood like the German cabinet maker Thonet invented in the middle of the 19th century – using steam.
This wooden bowl can be done in different sizes but I show the process for a rather small version. You'll need a sheet of 6 mm beech plywood approx. 22 cm x 22 cm. As tools I used my desktop cnc, a microwave oven and a suitable bowl. To finish the bowl I used some sandpaper and hard wax oil.
Step 1: Create the Drawing
The basic shape of this bowl relies on an Archimedean spiral. Many graphic tools can create a (logarithmic) spiral like you see on a snake house but not this kind. I found a script for Illustrator written by Sato Hiroyuki to create an approach of the Archimedean Spiral.
When rotating a single arm I added a circle to the outside. This guarantees that the pivot point is exactly in the center. I used a 30 degree angle of rotation resulting in 12 'arms'. It took a little time to optimize the shape so I got single lines. This was best because I planned to use separation cuts, thus the design is not set to a certain tool diameter.
Step 2: Getting Your G-Code Ready
I use Estlcam to create my machine paths. This software opens the dxf saved from Illustrator and when utilizing the automatic mode it can create G-Code in a blink of an eye. My arms are neither parts nor pockets so I told Estlcam to create 'engravings'. In this case setting the tool diameter is unnecessary, but might be necessary to flip the drawing to get the correct cutting direction. I wanted the machine to cut from the outside to the inside. As there is no possibility in the dxf to determine a 'path direction' as it's possible in Illustrator flipping is the fastest solution.
As the whole operation is strictly two dimensional you can always flip the work piece afterwards to define the direction of the final result.
Step 3: Cutting the Shape
It might be possible to cut the 12 arms on classic tools like a scroll saw or a band saw, but it's quick and precise if you have access to a cnc-machine. When cutting flat stock it's perfect to use a vacuum machine bed. In this case you can do without tabs.
I used a cutter with a very small diameter (1.2 mm) to achieve the narrow separation cuts.If you create a larger version with thicker material you might need a little larger bit.
The round forms of the design let the machine work with full feed rate as there aren't any harsh changes in direction where the inertia of the machine would leads to a need of deceleration.
Step 4: Sanding and Bending
After getting the part from the machine I sanded the upper and lower surface with some fine grit sandpaper and then soaked the whole thing in water. The water can penetrate the material fast due to the cuts and the process is a matter of a few minutes at most. Then I put the wet wood into a microwave oven and heated it up (600 W / 60 s). Be careful not to burn yourself when take it out.
You'll see the material gets very soft by now and you can easily insert the part into a suitable bowl.Press it in and let the bowl cool and dry out.
Step 5: Glue Up
After some time (I let the bowl sit in the form over night) you can take it out and be amazed by the result. The arms do not take the original from, but stay bent. To stabilize the bowl for when to put stuff in I decided to glue the arms in place. Simple clamps and some classic wood glue do the trick. As I had only four small claps I did this three times to get all arms glued up.
Step 6: Finishing
To protect the bowl against moisture and emphasize the wood structure I applied a layer of hard wax oil with a brush. It takes a surprising amount of oil because the bowl has so many parts of open end grain.
Step 7: Create Your Own!
So, how cool is that? You can download the files (free for non commercial usage) and start bending you own wooden bowl. Visit my website ZenziWerken for downloads and more interesting ideas to be used with a cnc or laser cutter. You can even use the supplied pdf to create paper templates and go for traditional tools.
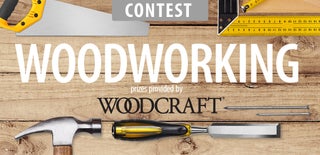
Participated in the
Woodworking Contest 2017