Introduction: HV9910 Universal LED Driver With 220v AC Input
HV9910 Universal LED driver with 220v AC input
Step 1: Introduction
Caution: Construction of this form of power supply is recommended only to those persons experienced or competent in handling AC mains. So do not try this circuit if you are not experienced in handling High voltages.
Great care must be taken while testing the power supply. Do not touch at any points in the PCB since some points are at mains potential. Even after switching off the circuit, avoid touching the points around the big capacitor to prevent electric shock. Extreme care should be taken to construct the circuit to avoid short circuits and fire.
HV9910 is universal LED driver used for driving string(s) of LEDs from wide range of input voltages (8v to 450v DC). Providing constant current on the output for driving different watts of LED string(s). I have taken help of data sheet of HV9910 , documentation of demo board 2 (file attached) of HV9910 and Application note AN-H48.
There are lot of information available in the above mentioned links and files about HV9910.
I have made this circuit by using different values of the components (See attached Excel file) to provide an out put of 35 to 40 volts DC and 1 Amp current.
One more different thing in this project is the use of two inductors in series for getting required output because I was not able to find one inductor of the required value from my local electronics markets. For this purpose I took help of a field engineer from Supertex and was successful in using two identical inductors of the same value in series to get required output.
In this project I have made a PCB for HV9910 from scratch to final.
Also I have attached Eagle PCB cad software schematic and board files used for components placements and making any modifications required by any user.
As HV9910 is a surface mounted IC so it is soldered on the bottom side of the PCB beside other components.
Step 2: Things Required
Following is the list of components that are required to make this project.
Copper sheet size 7.5cm x 7.5cm for making PCB
Ferric Chloride for PCB Etching (Please use rubber gloves to handle this chemical)
Fine Sand Paper
A small sharp Knife or blade
A small PCB drill machine for drilling holes in PCB
and drill bits of different sizes according to PCB holes sizes (.75 mm to 1.5 mm)
An Iron for toner transfer method for PCB
Electronic Parts list
C1 0.1uf 400v metal film capacitor
C2 22uf 400v electrolytic capacitor
C3 1.0uf 400v metal film capacitor
C4 2.2uf 16v electrolytic capacitor
C5 0.1uf 25v ceramic chip capacitor
C6 100pf ceramic chip capacitor
C7 0.47uf 400v metal film capacitor
CON1 AC AC Input (90v to 260v)
CON2 LED LED connector (Output 30v to 40v 1 Amp)
D1 STTH2R06U OR STTA506 Ultra fast diode
D2 FR307 3 Amp diode
D3 FR307 3 Amp diode
D4 FR307 3 Amp diode
D5 FR307 3 Amp diode
IC1 HV9910BNG Universal LED driver
L1 1.0mH 1.4 Amp
L2 1.0mH 1.4 Amp
NTC 50 ohm THERMISTOR
Q1 STD7NM50N OR FQP5N60C N-channel FET
R1 182K 1/4 watt Resister
R2 1K 1/4 watt Resister
R3 5K Variable R-TRIM
R4 1K 1/4 watt Resister
R5 470K 1/4 watt Resister
R6 1K 1/4 watt Resister
R7 0.22R 1 watt Resister
Step 3: Let's Make the PCB STEP 1
You need a print out of the board by using EAGLE software or you can use the attached PDF file for print out. Make sure that you get print out only on the laser printer photocopy and inkjet printer will not work. Because we will use the toner transfer method for making the PCB. In this method only laser printing works.
You also need the copper sheet for making PCB. Use very fine sand paper to fine grind and clean the copper sheet before toner transfer.
Place the print out of the board on the copper sheet upside down.
Put very hot iron (Iron must be on very hot position) on it becareful not to move the print out paper on the copper sheet. Iron should be on very hot position other wise the toner on the paper will not stick to the copper sheet.
Move the iron on the paper edge to edge for at lease 3 to 4 minutes. You will see that the paper will stick on the copper sheet. Make sure that all the paper stick on the copper sheet.
When you are sure that paper is completely sticks on the copper sheet remove the iron and let the copper sheet cool for few minutes.
Attachments
Step 4: PCB STEP 2
Now we have to remove the paper from the copper sheet.For this take a small container of warm water and put the PCB in it for at least 30 minutes. By doing this we will remove the paper and the toner will remain on the sheet. To remove paper rub the wet paper gently with your fingers. You can use a soft tooth brush for gently removing the paper. (It works well).
Before putting PCB in etching solution please check toner traces care fully all the lines and places are complete other wise use small permanent marker to fine edit your PCB trances.
Step 5: PCB STEP 3
Now take three table spoons of ferric chloride and add in a glass of water. You can make the solution as much you need. Use rubber gloves when handling this solution. Before putting PCB in etching solution please check toner traces care fully all the lines are complete other wise use small permanent marker to fine edit your PCB trances.
Put PCB in Ferric Chloride solution. If you use a little warm solution the etching process will work fast and it will take less time may be 5 to 7 minutes.. Keep moving the container (not splitting it) until PCB etches completely. Wash PCB with tap water thoroughly. See pictures.
Step 6: PCB STEP 4
Use small knife or sharp blade or any sand paper to remove only toner from the PCB. Then use very fine sand paper to clean the PCB.
If you want to keep safe the copper traces from corrosion then you can put any protective chemical layer on the PCB.
Step 7: Putting Components on the PCB (Assembling)
Use given picture of components placements in order to add the components on the PCB. Watch carefully when soldering the IC HV9910. there is a small circle engraved on it this is pin 1 of HV9910.
AC input 90 to 265 volts
Out put 30 to 40 volts DC 1 Amp.
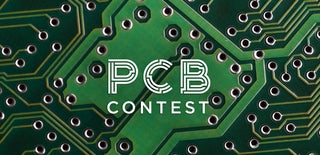
Participated in the
PCB Contest