Introduction: Hand Forged Skinning Knife
The delicate craft of forging has been around since before our Lord Jesus Christ was born. Evidence of forging dates back to 4,000 BC and most likely was practiced before this time. Forging has been essential to the development of the human species. Tools and weapons of war were first forged by early man out of bronze, iron, and copper. Only later was steel made to be used in the forging process for wars such as World War II. Even today the forging process is still used, although it is not traditionally done, but rather automated by machines. Some examples of forging today are gun barrels, some knives, even transmissions are made by forging! Without any further delay Lets begin this project!
IMPORTANT: make sure to view all of the photos as they help illustrate the steps clearly
WARNING: forging is a very dangerous practice and you should take very careful precautions before you begin. Remember to take your time and always wear the proper safety gear. Failure to do so may result in very severe injuries.
Step 1: Starting Off
First You will want to gather all of your tools and materials together that you will need.
The tools I used for this build include:
- anvil
- forge (can be propane, coal, or wood)
- bench grinder
- drill press
- belt grinder
- band saw
- assortment of wood and metal files
- bucket of water
- bucket of oil (can use motor oil, vegetable oil, or commercial grade oil)
- safety glasses
- gloves (optional but recommended)
- leather apron (optional but recommended)
- tongs
- assortment of hammers
- wire brush
- something to light the forge
The materials that I used in this build are listed below:
- bocote wooden knife scales
- an old medium carbon piece of scrap steel that I was able to salvage
- brass pins (1/8th inch thick)
- leather strips
Now this may seem like a lot of things to gather and to purchase. However it is possible to use alternatives such as an angle grinder and files to complete this project (this method will take longer to do). Now that we have gotten all the necessities out of the way lets get to the fun part of this build!
Step 2: Lighting the Forge
This step is pretty simple and straight forward. You will need a lighter, matches, flint and steel, heck even rubbing two sticks together! Depending on the forge you use will depend on how long it will take to light. For propane it is instantaneous, on the other hand charcoal, coal, and wood forges take longer to light and a large amount of fuel to keep them going at the temperature them need to be at for the metal to get to forging temperature.
I happen to have a propane forge which is pictured above and this is what I will use to make this project. Be careful with the propane forges as if you do not light them fast enough the flame produced will shoot out and ignite all the propane that leaks out of the forge.
Step 3: Flattening Out the Steel
Now that we have started the forge it is time to start moving the metal into a workable billet. To do this I will flatten the corners of this piece into a nice rectangle to work with. This particular piece of steel was a handle off of an old safe from a shutdown mine. I have made sure this piece has a good carbon content by spark testing it on my bench grinder. I have used it in knives that I have made and sold before and it is a good trustworthy steel.
Step 4: The Beginning of the Blade
Now that we have a workable billet its time to start to shape the knife into what we want it to look like. I always begin with a taper to start to form the tip of the blade. To preform this taper I hit the steel at the end of the billet at a slight angle to start to taper the metal to a point. It is important to keep the steel you are working with at a high temperature (about 1200 to 2000 degrees Fahrenheit) to be able to move the metal the way you want it to move. The amount of heat you use will ultimately determine how much the metal moves when you strike it. The hotter the metal the more it will move.
Step 5: Don't Mess Up
This craft is all about patience and learning from trial and error. I made a critical error to the tip of the blade by folding over the metal instead of flattening it. If I were to continue my customer could have sent shrapnel flying when using the knife. So I decided to cut my losses and save what was left. I took an angle grinder and cut about an inch and a half off of the tip of the blade. Even after doing this I still have enough material to complete the knife.
The pictures above show me realizing my mistake and thinking on how to correct it and then actually correcting it. Always remember to have patience and think about your next move to fix your mistakes and never give up.
Step 6: Reforming the Tip
Now that we have cut off the bad steel we can start to reform the tip of the blade. Just like the previous attempt at forming the tip I angle my hammer strikes to begin to form another tip. This time I use lighter hammers to form the tip to prevent folding the metal over itself again. While you form the tip the blade will start to twist and turn and it is important that you lay the metal flat on the anvil and re-straighten the blade. Try to keep it as straight as possible the entire time you are forging.
Step 7: Beginning to Form the Handle
Now that the outline of the tip has been shaped we will move on to the handle of the blade. I am using the horn of the anvil (the rounded part of the anvil that goes to a point) to start the finger stop and to mark the separation of the knife blade and the handle. I try to forge as much of the blade as possible to save me from having to grind a whole lot. I like the old way it was done and try to stick to the old methods as much as I can but I still use modern power tools when making a knife.
Step 8: Fully Shaping the Handle
This step takes the last step and simply extends the handle by using the same technique just making the handle bigger by using a larger part of the horn. Be sure to keep the blade as flat as possible and remember to re-straighten after putting the curve in the handle as this will warp the blade.
Step 9: Brushing Off the Slag
This is a completely optional step but is a very helpful one. This step you take a wire brush and scrap the extra slag off of the work piece. This ensures that slag does not splash back on you when you strike the metal with the hammer. This is more of a safety step more than anything. I've been splashed by slag before and let me tell you it hurts a lot!
Step 10: More Drawing Out!
Now that we have the basic shape of the handle its time to stretch it a little bit further and to thin it out a bit. Maintain the shape and curve of the handle while you draw this part out. The curve in the handle is a crucial part of how this skinning knife feels and works in the hand.
Step 11: Fitting to the Hand
Now that we have drawn out the handle it is time to fine tune the length of the handle so that it will fit perfectly in the hand. My customer's hand is roughly the same size as mine so I am fitting it to my hand which will in turn fit theirs.
Step 12: Now to Fine Tune the Shape of the Blade!
I am now using very small nail and ball peen hammers to achieve small detailed strikes. These detailed strikes save a lot of time at the grinder and allow me to see the details in the blade.
Step 13: Now to Press the Blade Flat for the Grinder
To ensure that the grind lines on the knife are symmetrical I am pressing the steel flat with a flat 4 pound hammer. Doing this allows me to put a nice even bevel on the blade.
Step 14: Chopping Time!
Time to cut the excess material off of the handle with a angle grinder. The simplest steps make all the difference in appearance!
Step 15: Grinding Time!
Time to grind down imperfections of the handle and the blade to prepare the it for a handle. I am using a hand file to profile the inner curve of the hand stop. The belt grinder and bench grinder I am using to knock off all of the nicks and dings all along the blade edges and handle edges as well as thinning the blade and preparing a spot to stamp My initials and the year it was made. The water bucket is to cool off the blade as it gets hot when using the belt grinder for extended periods of time.
Step 16: Drilling Time!
Now we are pretty much done with the forge other than quenching and texturing, but we will get to that later. My customer wanted two brass pins along with a third hole to run a leather strip through to tie a dangler loop. To space the two brass pins I spread my fingers and use that as a guide to judge where to place my pins. Before you harden a blade it is always a good idea to drill and grind the blade. When the blade is hardened It makes it difficult for the drill to go through the metal and wears away the belts faster. This is because when the metal is softer the belts and drill eat away at the soft metal better than if the metal was hard.
Step 17: More Grinding!
Now to grind in the bevels on either side of the knife. Being a skinning knife the angle needs to be very small from which the bevel is set. Take this time also to address any other flaws that can be taken out with the grinder.
Step 18: Hand Shaping the Handle
This is where the craftsmanship comes into play. Using your hands rather than everything being automated. The grinder was not able to reach the little part of the hand stop so I hand filed it smooth and finished it with sandpaper.
Step 19: Texturing the Blade
What I mean by texturing is purposely putting dents in the spine of the blade to give it some character. This is not necessary to make a complete functioning knife but it gives the blade something that stands out among the rest. When I am done with it, it will have a rough bumpy feel to the spine. To do this I am taking a very light ball peen hammer and using the edge, the ball, and the flat part to put nicks and dings into the spine.
Step 20: Stamping the Spine
This is a unnecessary step but I take this step to mark my work to show it is hand made and to show the smith who made it and the year it was made. I am still working on making a trademark stamp to mark my work with but until then I just use my initials and the year. In the picture the 9 is backwards on the stamp but when it transfers to the work it is correct.
Step 21: Now to Heat Treat the Blade
In order to correctly heat treat a blade you must use some type of oil and have the blade at an extremely high temperature. I use vegetable oil for quenching but other oils work just as well. Heat the blade evenly by moving it in and out of the forge to ensure an even heat throughout. They once the blade is a very bright yellow/orange it is time to dip it in the oil. It is important to ensure that there are not any warps in the blade as they will worsen when hardened. Whenever you quench the blade try to keep it straight in the oil until it fully cools. Now be careful because when using extremely hot metal and combining it with oil it will flame up very high. Once the blade is fully cooled in the oil I like to dip it in water to ensure that the whole blade is cooled, this is because the quenching bucket I have is not big enough to fully submerge the blade entirely so I finish it in the water bucket. This does not affect the hardness of the knife because the blade part that holds an edge is hardened.
Step 22: Redo Your Bevel
This step is probably the easiest one to do. All you have to do is go back over the bevel you have already made to make it shine again. Go back over the edges of the knife as well just to add some detail to it and this will be important for when the handle is added to the blade.
Step 23: Fitting the Handle and Beginning to Shape
To fit the handle to the knife you take two knife scales that you have made or have bought and fit them one at a time by drilling through the wood and lining up the holes. To do this and ensure it stays in place I take the scale and tape it to the blade and then drill through both. Then I line up the second scale and drill through it as well. Once you have done this its time to fit everything together. Once you have done this take the scales back off and start to round them off at the side that points to the blade. Do this for both scales to make the knife flow rather than have a block handle.
Step 24: Cutting the Pins to Size
Now that we have the handle fitted to the blade it is time to make it more workable. By this I mean cutting the pins to a smaller size to work with but still long enough to use. I cut both of the pins down to about and inch and a half or less. Once I have cut them both I round the tips of both sides of the cut piece so they will fit into the drilled holes better and not get caught on anything.
Step 25: Cutting Away Extra Wood
We are going to cut away extra wood that is not needed in this step. We will cut away as much as possible to save the grinding belt I am using so it will not wear away if it doesn't have to be worn away. The end result of your cutting should result in a rough outline of the end result. Be very cautious to try and not hit the metal when cutting with the band saw as this will dull the blade and make more grinding for you later.
Step 26: Shaping the Handle
Now that you have your rough shape of your handle it is time to fine tune the wood with the grinder and grind it down even with the metal and take any nicks that you have made with the saw blade out. Be sure to leave the handle pinned together and make sure to grind the material down evenly for both sides of the blade. By this step you should be able to see how the knife will truly look once completed. The handle will be kind of like a block by now and will not be comfortable in the hand at this point. We will round the handle off once we have epoxied the handle together and start to complete the handle.
Step 27: Piecing the Handle Together
I highly recommend using a two step epoxy when securing knife handles in place. I use gorilla glue two step epoxy, This can be found at your local hardware store. The epoxy I am using starts to set in 5 minutes after mixing it together. Once you mix the epoxy you must hurry and apply it to the handle on the knife. Then push your pins and handle scales onto the blade and squish it all together. Clamp the handle together with at least two different clamps and wipe away excess epoxy. Let the knife sit for at least 12 hours before continuing to work on your project.
Step 28: Grinding the Pins Off
Remember to keep the blade cool so that the epoxy does not melt off of the handle. You want to grind most of the pin off of the handle to prepare it to go to the belt grinder. If you do not grind most of the pin off it will catch the belt and tear it when you go to grind the handle to round it.
Step 29: Finishing the Handle
To finish the handle we will transition from the belt grinder to hand files to sandpaper to finish it off. All of this is to fine tune and make the handle as comfortable as possible. We use the belt grinder to get the extra epoxy off of the knife and to start the rounding process. Then we finish the knife with hand files and a sandpaper finish. I was not able to get a picture of the sandpaper finishing but all I did was go over the edges with a file then hit the same spots with sandpaper.
Step 30: Tying a Dangler Loop
This "dangler loop" is nothing more than a piece of leather cut into a thin strip and tied onto the knife. To attach the knife run the piece of leather through the open hole at the end of the handle. Stick your hand through and tie it off with enough room to get your hand in and out with ease but able to hold the knife in place if you drop it.
Step 31: Sharpening
This should always be your final step when making a knife. If you sharpen before you are done working on the project you run the risk of cutting yourself or deflecting the edge and messing up the whole project. To sharpen the knife take a wet rock and lay down a towel on a table. Then wet the rock so that you can sharpen the blade. Then at a 20 degree angle start to slide the knife down the wet rock using the whole rock to sharpen the blade. Sharpen until you have reached the point where it will shave your arm hair off.
Step 32: Your Done!
Congratulations! You have successfully made a hand forged skinning knife! Now the best part is actually using the knife and just admiring that you have made such a amazing piece!
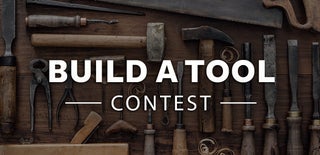
Participated in the
Build a Tool Contest