Introduction: Walnut Wood (triathlon) Bicycle Frame
As an income-less college student, it can be difficult to get into the sport of triathlon. Swimming and running are fairly cheap sports, but outfitting a bicycle that is competitive can be daunting. I bought a road bike from a bike swap for $600 a couple years ago, but it wasn't great for triathlons and I recently got a dent in the top tube that worried me. Luckily, as a part of my engineering curriculum I learned what I needed to build my own frame out of locally sourced black walnut wood.
While this was a fairly intensive 5-month project (I only had time to work on it occasionally because of school), I'll do my best to give a good outline of the steps involved. Prerequisites are a good understanding of bicycle design (which I attained mostly by reading on the internet) and access to some wood working tools and a vacuum bag.
Step 1: Materials and Tools
This list is not exhaustive but it provides an overview of the most important tools and materials needed.
Materials
7-10 board feet of black walnut (other hardwoods may be suitable)
Titebond III wood glue
Locktite Epoxy (see image)
appropriate bicycle tubing for the head tube and seat tube
Bottom bracket insert
flexible metal tubing for cable routing
3/4" plywood
and all associated bike parts except for the frame. Like I said, I used all the parts from my previously owned road bike.
Tools
Planer
Vacuum bag and pump
band saw/ miter saw/ table saw
Assorted drill bit sizes
Router and necessary bits
hand drill
drill press
Step 2: Bicycle Design Stage
Before any building can occur, you must have a well developed design. The great part about a wood bicycle is that you can cater the bike frame exactly to your fit and your needs. I used solidworks as a design platform to draw and model my frame. I essentially started with the geometry of my road bike, because I knew that it fit me, and then adjusted it to have the triathlon qualities I was looking for. Notable adjustments I made were increasing the seat tube angle, adding an airfoil shape to the down-tube and seat-post, lowering my seat-stay attachment, and adding a profile for the back wheel.
It is important during this step to keep in mind the components that you will be using for the build. The wheels, seat post, steerer, and bottom bracket insert are all sizes that are especially important to get right.
The computer model should have the ares of the tubes that will be hollowed out to save weight. I left about 6mm walls in all of the tubes.
Finally, you should get the outline for the main triangle printed on a 1:1 scale. I was able to get an engineering-printing company to print me two copies for about $5.
The bike will be made by laminating thin plies of the wood together. By doing this, you can take advantage of grain direction in key parts of the bike to improve strength in multiple directions. My bike is made up of 8 layers of plies. Because it is symmetrical, I made 4 plans of ply orientations that would be mirrored across the center of the bike. Above is a picture of how I planned these layers on solidworks for another bike I made. For the head tube (which encounters a lot of stress) I made sure to include + and - 45 degree angles from the steerer axis for 4 of the layers and longitudinal with respect to the top tube and down tube for the other 4 layers. For the joints of the down-tube/seat-tube and top-tube/seat-tube, I made sure that the plies coming in overlapped every other ply so that the joints would be well integrated.
Step 3: Laminating Layers
This step takes a lot of time and care. It can be difficult because the end product seems far off, but doing this correctly is important to the integrity of the bike.
The first step is to create the plies. I used plies that were everywhere from 2x10" to 5x40". My ply-orientation layout from the last step told me how many plies I needed of what sizes. Essentially I picked parts from my walnut boards that didn't have a lot of knots and assigned them, piece by piece, areas on the bicycle frame. Then I used the table saw to cut them roughly to size at about a 10mm thickness (pictured above), planed them down to 6mm thickness, and used a miter-saw to cut the angles I needed for them to fit into my layout.
I used the paper copies of my design and the 3/4" plywood to make templates for my bike frame. One of the printouts became the outside profile and one of them became the inside profile (for routing out the hollow portions). I used the outside profile template to begin laminating the layers of plies together. At my school's woodshop we built a vacuum table for this specific purpose, but you could use a vacuum bag and two boards to do it on too. Essentially just laminate the two halves of the bike together one layer at a time so that you end up with 2 four-layered blocks of wood with all of the grain going in the directions that you designed.
After this process if over, the bike begins to take shape and it is a lot of fun! Unfortunately I didn't get pictures of the lamination process, but you can see an idea of what it turned out like on the next step.
Step 4: Routing and Shaping
After the lamination, you essentially have two big bulky blocks of laminated wood, and your bike frame is hidden inside. This step brings it out.
Routing
I actually used a hand router and a template to do most of the hollow spaces you can see in the first picture. For my down tube, since I had the airfoil shape, I used the milling machine pictures to get the tapering effect.
Profiling
I also used my other template to table route (with a straight bit) the profile on both of the halves. At this point, you have a squarish looking bike frame, but it is starting to take shape.
Shaping
I used a table router to curve the edges of the tube-like portions of the bike and an orbital sander to make my airfoil shapes on the down tube and seat tube
Note: There is a chance, depending on the laminating and on warping, that the two halves wont fit together flush. In that case you need a router and a sled or a milling machine of some kind to flatten both surfaces.
Step 5: Metal Inserts
The two metal inserts need to be prepared.
The bottom bracket is brazed or welded to a seat tube to allow for the bottom bracket and seat post to fit into the frame. It takes some work to get the piece to fit perfectly between the two halves of the frame.
The head tube just needs to be cut to the correct length.
Then both of the metal inserts are "swiss-cheesed" to save a little weight (because they aren't strength members) and sandblasted so that the epoxy will adhere better.
Step 6: Combining the Main Triangle Halves
This piece, if all the previous steps are done well, is not too difficult.
The metal inserts are included (along with the spaces for the internal cable routing tubes) and the halves are made to fit together with the inserts included.
Not pictured is a space for a pin to go through perpendicular to the frame for the back brake to mount in. The space can be dremmeled out before the halves are put together.
When everything is correct, then wood glue is placed on the surfaces between the two halves and epoxy is spread out around where the metal inserts are. The two halves are put together and pressed together in the vacuum bag or table. The above picture of the vacuum set up is the same I used for the initial laminations.
Step 7: Stays (chain Stays and Seat Stays)
For the stays, I made 1/8" plies and laminated 5 together using a plywood mold with 6 bolts. It was a separate mold for the chain stays and the seat stays, allowing the expansion from the width of the front triangle to the width of the rear hub.
Using a normal bike making fixture, I held the frame and stays in place to get a close shape for all of the stays. Then it was a matter of drilling holes that would screw the stays into the steel drops and making sure the half inch pin that the back brake bolts onto fit together.
Using the epoxy between the stays and the frame as well as all around the bolts that attach to the drops, I clamped it all together with the back wheel in. By having the actual back wheel in I could be sure that the wheel lined up straight with the frame.
Step 8: Finishing Up
Next I used a gunstock finish on the whole frame (with a whole lot of sanding) to get a protective and good looking finish. After that, I started working on getting the components to work. I had to paint my front fork black so that it wouldn't clash with the frame as much.
I had to mount a bracket for the front derailleur. I dremmelled out a place on the seat tube and epoxied in a braze-on bracket to do the trick.
Besides that, most of the components fit because I designed them to the correct sizes. With that it was just finishing touches and then I was ready to ride!
Step 9: Riding!
Above is a picture from my first ride. I was so excited to finally get it on the road after 150+ hours of working in the shop on it. I was a little worried because there are a lot of unknowns involved in the process. Luckily everything turned out great and the handling and tracking of the bike was nearly perfect for me. The fit is even better than my road bike was, and the wood removes a lot of the road vibrations so my butt-soreness has also gone down.
I got a friend to take some professional pictures of the bike, check them out!
Update: I just started a blog to write about my bike from time to time. I will likely add more information there in the future about builds and maybe discuss interesting rides or triathlons. The link is http://triwood.wordpress.com/
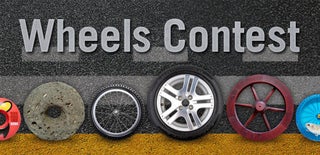
Second Prize in the
Wheels Contest
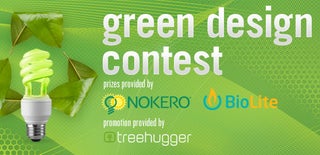
Third Prize in the
Green Design Contest