Introduction: How to Make a Phone Wire Bracelet
These wires are from a 25 pair telephone cable that was discarded at the office. It just didn't seem right to toss them!
I after pouring 15 ounces of epoxy I drilled a hole (the epoxy harden in about 5 hours ) for the inside diameter a 2 5/8"
After a quick turning to a smooth cylinder, I started sanding it... and sanding it... I wet sanded up to 400grit then switched to my high grit polishing pads. 1200 grit to 12000 grit! It's a long process! I still had to sand the inside... but I did that by hand. It took an hour or so.
I love the look with the wires and exposed cooper! Thanks for looking!
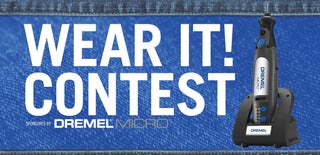
First Prize in the
Wear It! Contest
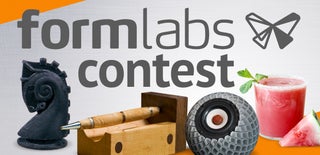
Participated in the
Formlabs Contest