Introduction: How to 3D Print on String (How to Make Floating Jewelry)
After experimenting with 3D printing on tulle, I wanted to keep going. While trying to figure out earring designs, I decided to use string instead of tulle to see what would happen and it worked well 3D printing on string is super easy to do and has really fun results.
I can't find an example, but I feel like I've seen an anime or cartoon character that had earrings that just seemed to float off the ear and this would be a good way to accomplish that effect for cosplay.
Instructable 279
You can find the Wind Spinner Earrings for sale in different colors in my Etsy store!
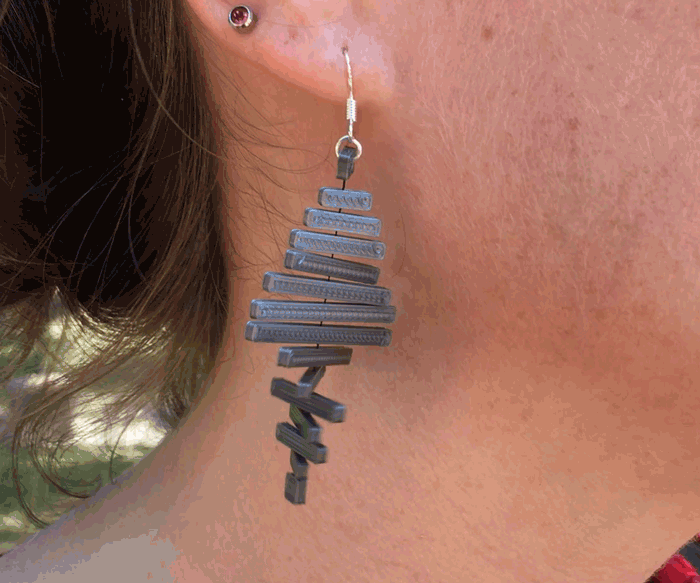
Step 1: Supplies
The supplies will vary depending on what specifically you are creating (I'm making earrings), your design, and the type of string you use.
Supplies:
- 3D Printer - I'm using a Prusa MK3 (it is super easy to change the filament, just saying)
- Slicer - I use Simplify3D but there are many out there, you just need to be able to pause the print and move the head out of the way so you can put down the string
- Thread - don't use something too thick or it could get caught during printing
- Clear/Invisible thread - I'm using Nylon
- Fibrous thread - like cotton or polyester - I'm using 100% polyester
- Painters Tape - binder clips might also work well for holding the string tight so it doesn't shift
- Scissors or Exacto - it can be hard to cut the excess string next to the print so be careful so you don't pull the piece off while trimming it
- Glue - (optional) E6000 should work, or I recently got Acrylic Cement and so far it seems to work well. I have tried using Loctite Super Glue Ultragel Control and while it seems to work, it discolored my black and made it white.
- Jewelry Findings
- Earrings
- Jump Rings
I'll be going over a lot during this Instructable, but I also wanted to try to gather together some tips in one place, so here they are:
- Skirt: a skirt to catch excess filament that oozes out after the pause/color change - it also holds thread tight and in place, I recommend a skirt that is 3 wide and goes to at least one layer higher than when you add the string
- Layers: need enough to cover the string, 4 on each side at least especially if the threads contrasts
- StringColor: the color of the thread should work with the filament - probably not use black with white filament
- ThreadSize: avoid thick thread (embroidery floss or yarn) so you don't catch on the head
- Tape: tape as close as you can to the print, make sure it won't try to print on top of the tape
- Glue: glue can help to hold the string onto the finished piece - glue on nylon is iffy, but glue on the fibrous thread seems to help
- KnottingString: you can try knotting at the very top and very bottom of your finished piece to try to keep things from moving
Step 2: Past Tests
I actually started testing this idea ages ago right after I finished the 3D printing on tulle instructable, but printer issues and then waiting for the new printer my hubby got me to come delayed me finishing it (and, let's be honest, laziness).
So here are some early pieces when I first figured out what I would need to do to get this to work. Along the left and top you can see the ones I did with tulle before moving onto string. Tulle works fine, but you can see it easier than string and it limits you on movement. No twisting of pieces with tulle.
The white one on the right is when I tried braiding 3 pieces of nylon together. This did not work but I'm not sure if a looser braid would work better or a tighter braid. I'd have to do more experimenting.
Since these were just tests, after I got them off the printer I actually yanked on them to see how easily they would move. With enough effort, you can get all of them to move, but using knots and fibrous string ended up working out the best.
Step 3: Designing Your Earrings
You need to start by designing your piece of jewelry (or whatever you want to print onto string, I will continue speaking about earrings, but these tips can be directed at anything you are making).
First, think about the size of the earring. You don't want it too wide that it is going to hit your face (unless you don't care) and you don't want to go too long because the longer the piece the more likely the string will be shifted out of place during printing. Lastly, regarding size, you need to think about how thick you want the piece. All of my designs so far have been 1.6mm thick which comes out to 8 layers when I slice it. This seems to work well as 4 layers seem to just cover the string. This is also a nice light thickness for the earrings.
When it comes to the design, think about how big each piece of the design is. This is important because the more there is to it, the more plastic there is to stick to the design (we will be printing at 100% infill, but if the part is still thin, there will be issues). For example, my "Wind Spinner" earrings (inspired by the Mesmerizing Wind Spinner by TheCarmichaelWorkshop) started out fairly thin going up and down, but they were sliding so much so I ended up thickening them after a few iterations.
Lastly, you should think about angles when you design your piece to avoid the need for support material. My Wind Spinner earrings were flat pieces so there were no issues, but the 8-sided diamond earrings angled on the top and bottom. Because I wanted this dimension to it, I made sure my angles were 45 degrees to avoid support. Though, if you can design a piece that requires support material that won't be in the way of the string, go for it.
If you are going to make jewelry, you will need a loop or a hole which you will use to attach your 3D printed piece to your piece of jewelry. I put 2mm holes where I needed them, but if a hole doesn't make sense, you can also design a loop sticking out the edge of the piece.
Step 4: Scripts and Earring Files
I will mention these where they are relevant later, but I wanted to slip these in so they are hopefully easy to find when you need them.
Pause: - below it will pause after layer 4, move the head to X0Y0, and continue at layer 5 when you restart the 3d printer, you can replace the layer with any layer, just remember it will pause BEFORE that layer.
{REPLACE "; layer 5," "G28 Y0 X0\nM0\n; layer 5,"}
Color Change: - below it will pause after layer 4, allow you to change the filament, and continue with layer 5
You might just be able to do this right on your 3D printer, but it is nice if you can put it into the script so you don't have to remember to pause your print, change the color, and start it up again manually. You can replace the layer with any layer, just remember it will pause BEFORE that layer.
{REPLACE "; layer 5" "M600\n; layer 5"}
Notes about Slicing:
- Slice the item right away and see how many layers thick it is, this will determine at what point you add the pause to add the string. If your design is an odd number of layers thick, I recommend making it slightly thicker or thinner so it is easier to add the string in equally.
- Add a skirt that goes up at least 1 layer higher than when you will add the string. When you add the string, there is a good chance filament will ooze out of the hotend, if you have a skirt it will help wipe off that excess filament before continuing on with your design. If you don't do this, there is a very good chance the excess filament will stick to your design and catch later.
- Place the design on the bed so it is towards the back, whether you use the pause or color change the head will head towards the front of the bed and you need to be able to get to your design to tape down your string. For the pause, I put my design in the back right, for the color change I put the design in the back left.
Step 5: Using Clear String (more Difficult But Looks Good)
Prep by Knotting your String
I have yet to find a clear string that isn't slick, that being the case, anything you print on a slick string will slide fairly easily off. I experimented with different ways to combat this and the best method seems to be to knot the string wherever the 3d print and string intersects.
For example, I decided to print my 8-sided diamond earrings on a clear string, so I measured from top to bottom of the design and found all the places the design will intersect with the string and measured it out on a piece of paper. Now, I needed to knot within all of those areas. If you can only do 1 knot in each section, so be it, but if you can go for 2 or more. I did 2 knots per section.
If you are going to use my diamond earring, you need to put knots between (measuring from the bottom to the top):
- 0-3.75mm
- 7.94-17.46mm
- 21.65 - 25.40
- 29.38 - 36.10mm
I found it was easier to do this if I taped the strings down, and then loosely put the knot on a pin or tack. Then, I slid the knot carefully until it was within the zone I wanted it and slipped it off the pin while pulling it tight.
Once you have all of your knots in place, get a piece of tape on each far enough away from the knots that they won't interfere with the print when placed. This is mostly so you won't lose the string before you need it and you remember which end is up or down.
Printing
Now it is time to slice then print. You will need to put a pause in the script before generating the gcode for the print so that the head will move away from your design and allow you to place the string. It is the same script I used for 3D Printing on Tulle Fabric. Below I altered it to put in the layer that works if your piece is 8 layers thick.
{REPLACE "; layer 5," "G28 Y0 X0\nM0\n; layer 5,"}
When it gets done with layer 4, the head should move out of the way and allow you to place your string. Tape it down as close to your print as you can without interfering with the print. In my earlier prints, as seen above, I taped over the skirt since it only went up 1 layer. For later prints, I decided the skirt could be helpful and brought it up through 5 layers and had to tape right outside the skirt.
Continue the print.
When it is all done, carefully take it off the bed. The hope is that the knots will hold the piece pretty firmly in place on the string, but it is still best to not be rough with it.
(If I were to print this design again, I would probably try to bring the design in tighter. I think there was too much of a gap between the top and bottom piece and too much space between the diamond in the middle and the outside diamond ring.)
Step 6: Using Fibrous String
I'm not sure the best way to describe it, but the other type of string you can use would be a fibrous one like polyester or cotton.
Using this is really simple compared to a slick string as all you have to do is line it up on your print and tape it down. Of course, you still need to add a pause or color change into the gcode so you can add the string.
The third image above just shows the evolution of the wind spinner design. As you can see it started longer and the pieces were smaller, but the string was shifting too much during the print and it wasn't gripping to the string well. So, I brought the pieces closer together and made them a bit bigger.
I ended up changing the design above slightly by making the top piece of the design longer so there would be more plastic to grip the string. The hole I needed to add took away from that and after wearing these ones, the top piece disconnected.
The file attached earlier is for the final updated design.
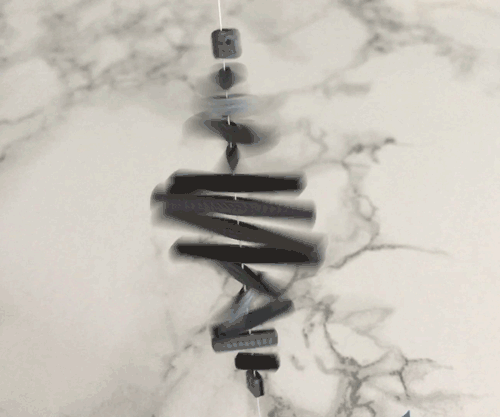
Step 7: Using 2 (or More) Strings
After doing all these prints, I decided to see what it would be like if I used 2 strings. I tested this method with the wind spinner design, but this can be particularly helpful if you have a wide design.
If you don't want your design to twist, make sure you lay the strings flat and don't twist them. If you do any twisting, the final print won't hang flat, it will try to twist.
Also, make sure the print will cover the design. As you can see in the second picture, the string at the top shifted for the earring on the right causing it to not connect the top part of the design to the rest of it :(
Step 8: Glue
To try to help everything stay together, you can smear some glue on the ends of the piece where the string sticks out. This didn't seem to help with the nylon string, but other strings it seems to help.
Step 9: Making Into Earrings
This is the easy part ;)
Now, just use a jump ring to attach your earring to your finished piece. Enjoy!
Above, I am also sharing the parallel diamond design I tried (4th image). It was more difficult because the string shifted and because of the design, it just didn't look as nice. The string needed to come right out the tips to hang right.
Step 10: Enjoy
Please share if you try any of these or your own designs. I'd love to see how things turn out :)