Introduction: How to Build a 12x20 Cabin on a Budget
Building a cabin yourself is much more economical than buying a prefab storage shed. The cost of materials for this build, including doors and windows, was around $2,200, which was about the same price as the install would have been on one of this large size if I’d purchased it from a hardware store. I know this for a fact because six years ago I bought a 12x16 shed from a well-known company close to where I live and it cost $2,000 for them to build it and drop it off. Today that same building would cost $4,200. With such a big price increase I decided that if I wanted to add a cabin to my property I had to build it myself.
If you decide to do the same, remember to check with your local authorities to make sure you don’t need a permit. It’s not likely that it’s required for a building of this size, but you never know.
If you would like to see the finished inside of the cabin please click here: https://www.instructables.com/id/How-to-finish-the-inside-of-a-12-x-20-cabin-on-a-b/.
If you would like to see the matching modern outhouse please check this out: https://www.instructables.com/id/modern-outhouse/.
Step 1: Floor Illustration
Here is the 12x20 floor plan showing where the 4x4s and the floor joists would be located.
Step 2: Drilling and Planting the Posts
1st picture: shows my ford tractor and my neighbors post hole digger he let me borrow.
2nd picture: shows the posts planted and the bottom 2x10 stringers.
3rd & 4th pictures: show the upper 2x10x12 and the 2x10x16 upper stringers being nailed in at 7 feet 8 inches.
Step 3: Setting the Center Rafter Board
This picture shows the center rafter board. I measured over 6 feet to the center. The roof is going to be a 5/12 pitch roof so the rafter board had to be 30 inches to the top of the board.
Step 4: Making the Angles for the Top and Bottom of the Rafters
1st picture: shows using a quick square. Put the pivot point at the top of the board and turn the square until the 5 on the * COMMON TOP CUT* line graph lines up with the outside of the board. Then draw the line to make the angle.
2nd picture: Once you cut your first angle then you have to measure from the tip of your cut down the length of the rafter to get your measurement for the seat cut. Once you have that measurement then you put the pivot point on that mark and turn the square until you get your 5/12 angle again. Then measure up that angle 2 1/2 inches and draw that line.
3rd picture: shows taking the edge of the square and lining it up with the 2 1/2 in line and turn the square until the tip is lined up with the edge of the board. Then draw that line.
4th picture: shows the angle seat that I just drew cut out.
Step 5: Setting the Rafters
1st picture: shows the rafters being set next.
2nd picture: shows the rafters on and the starting of the purlins being put on the top of the rafters for roof support. This is what the metal roofing is screwed to.
3rd picture: shows the tails all cut to 9 inches long and shows the steel roofing over hanging the roof by 2 inches to support the facia boards.
4th and 5th pictures: show the roofing installed.
Step 6: Adding on a 4 Foot Porch
Here is where it started to get complicated for me. I was looking for a 12x16 cabin, but once i looked at it I decided I wanted the whole 12x16 for floor space so i added a 4 foot porch to the 12x16 to make it a 12x20 total building instead of a 12x12 inside living space.
Step 7: Side Wall and Purlin Illustration
Step 8: Lag Bolting the Outer Joist to the 4x4 Poles
I had to screw (36) 3x3/8 inch lag bolts to all the outer joists into the 4x4s for stability.
Step 9: Hurricane Studs
1st picture: shows the (20) 13 inch hurricane studs with the 5/12 pitch angle cuts.
2nd picture: shows them installed.
Step 10: Floor Joists and Insulation and Floor
1st & 2nd pictures: show the (14) 2x10x12 floor joist installed
3rd & 4th pictures: show the 1x2 furring strips nailed to the inside of the floor joist 1 inch below the top of all the joists.
5th picture: shows the 1 inch insulation board between each joist before gluing and nailing the floor to the joist.
6th picture: shows my Dad lending a hand nailing down the floor.
Step 11: Rough Sawn Lumber for 8 Inch Board and Batten Siding
1st - 3rd pictures: show my dad cutting the siding boards to 8 foot long.
4th - 6th pictures: show the boards up on the wall and the soffit and the facia boards being put on.
Step 12: Studding in the Porch Ceiling
This picture shows the studding in for the porch ceiling, 16 inch centers and 4 foot long studs.
Step 13: Studding in the Front Wall and Door Frame
Studding in the front wall and front door frame, it was a hot day!! Here's my dooraggin' Dad! Just had to take a picture of this! He-he-he...
2nd picture: my friend Josh came over for a day to lend a hand on the mitre saw.
Step 14: Gable Ends
Here are the gable ends finished with the batten strips attached. All that's left for them are the two vents.
Step 15: Finished Cabin Structure
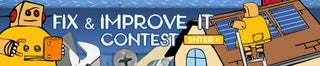
Finalist in the
Fix & Improve It Contest