Introduction: How to Build a DIY Light Box Sign With LASERS!
Welcome to my DIY Light Box Sign build! This was a fun one, with tons of options for customization. If you don't need a sign, you could use a plain piece of glass instead and have an awesome light box. There are tons of cool ways to customize this build to suit your needs. Let's get started!
Don't miss the video above for lots more details!
Step 1: Gather Your Materials & Tools
This build can be made with a miter saw, table saw, and drill. You could even cut the grooves with a router if you don't have access to a table saw! The easiest way to get the glass is probably from an old picture frame. Check your local Goodwill!
DIY Light Box Sign Materials List
The links below are affiliate links, from which I get a cut of the sales. They don't cost you anything extra and help to support me!
- 1x2x6 (I used Walnut, but Oak, Select Pine, or any other wood would work!)
- ¼" plywood
- Pane of glass (size is up to you!) : http://amzn.to/2jt4RZf
- Spray Paint (for painting the back of the glass) : http://amzn.to/2jabUoH
- Decor for the sign (vinyl lettering, more paint, use your imagination!) : http://amzn.to/2knPxB5
- Battery Powered LED Light Strip : http://amzn.to/2jNtiRO
- Finish of your choice (I used Waterlox)
DIY Light Box Sign Tools List
- Dewalt 20V Max Impact Driver : http://amzn.to/1QxJD7w
- Bosch ROS65VC-6 Random Orbit Sander : http://amzn.to/2aWHSDR
- SawStop PCS 1.75-HP Professional Cabinet Saw : http://amzn.to/2aqqRyn
- DEWALT FLEXVOLT 120v MAX* 12" Double Bevel Compound Sliding Miter Saw : http://amzn.to/2ah20gS
- (Optional) Full Spectrum Laser Cutter : http://bit.ly/fullspectrumlaser
Step 2: Decide on Frame Size & Contents of Your Light Box!
My buddy Brad laser etched this piece of glass with my logo on it, and that's what I used inside my light box. Check out his version of this build, which I'm remixing, here.
There are TONS of other options though. Maybe a cool sign for your kid's room featuring their favorite superhero? Or maybe a light up sign for your game room with your favorite team's logo! The sky is the limit! You do NOT need a laser cutter for this build.
Step 3: Cut Frame Pieces to Rough Size
My piece of glass was 16" wide by 12" tall, so I made my frame accordingly. To pick your final dimensions, consider how much of your piece will be inside the grooves on the inside of your frame. For example, I wanted my piece of glass to be ¼" into each side of the frame, to make sure it was well supported. Because of this, I subtracted ½" from the width and the length to get my inner dimensions. Since my wood was ¾" thick, the formula was as follows:
For the height, I took 12" (from the glass height), subtracted ½" to account for the grooves, and added 1 ½" (¾" x 2) to account for the thickness of the wood. This left me with 13" long sides.
For the width, I took 16" (from the glass width), subtracted ½" to account for the grooves, and added 1 ½" to account for the thickness of the wood. This left me with 17" long sides.
You don't want to cut the pieces to their final length at this point, just get them close. We'll cut them to final length in the next step.
Step 4: Cut 45 Degree Bevels on Ends of Frame Pieces
With my final dimensions decided and my pieces cut to size, I set up a stop block on my miter saw for the first length, 13" in my case. I set the bevel angle on my miter saw to 45 degrees and made my first cut. I flipped the piece around, pushed it up against the stop block, and made the cut on the other end of the piece.
I repeated this for the other matching piece from the frame, without moving the stop block! As long as the lengths of your sides are identical and your angles are correct, you will end up with a gap free frame.
After cutting the bevels on all of the test pieces, I did a quick test fit and they were looking good!
Step 5: Cut Grooves Into the Inside of the Frame Pieces
Each piece of the frame needs two grooves on the inside: one groove for the piece of glass and one groove for the plywood back. I set my table saw's blade height to ¼" (remember how I decided on a depth of ¼" in the previous step?), set my fence to ⅜", and made my first pass.
One pass was all that was needed for the piece of glass, since the kerf (or thickness) of my saw blade is ⅛".
With the first groove done, I flipped my piece around 180 degrees and made another pass. Since the plywood backing I'm using is ¼" thick (technically, just under ¼" but that doesn't really matter here), I made one pass, moved the fence over ⅛", then made another pass. This left me with a ¼" wide groove.
Step 6: Cut Plywood Back to Final Size
With the grooves on the frame cut, I cut my piece of plywood to final size using the table saw and miter saw. With all of the pieces finalized, I put everything together to make sure everything fit, and it did!
Step 7: Paint the Back of the Glass to Diffuse Light
Next, you will need to paint the back of the glass panel to diffuse the light. I used a basic spray paint, nothing special here. Don't put on too many coats, just enough to get even coverage. Otherwise, you'll block too much of the light.
Step 8: Sand the Frame Pieces
With the paint drying, go ahead and sand the pieces of your frame. I used 80, 120, then 180 grit sandpaper on my random orbit sander.
Step 9: Assemble the Frame & Sand Corners Flush
I used 1 ¼" screws to assemble the frame. This was in case I needed to disassemble the frame at some point in the future. Since I bring this with me to craft fairs, etc., there is a definite chance that the glass could be broken at some point.
With the frame assembled, I sanded the corners flush.
Step 10: Apply Finish (Waterlox, in My Case)
For the finish, I used Waterlox. It's a blend of tung oil and resins, so it brings out the grain of the Walnut but also has a protective film once it dries. It's one of my new favorite finishes for Walnut, I love it so far. I just wiped on a few coats, sanded with 320 grit sandpaper, then wiped on one final coat.
Step 11: Install LED Lights & Assemble
I used a battery powered LED light strip for this project since, as I said, I will have this with me at craft fairs and other places where power isn't always easy to come by. The one downfall of these battery powered units is that they are significantly less bright than their plug-in counterparts.
Installation was a breeze. I drilled a hole in the plywood back, ran the lights through, and stuck the lights to the inside of the back using the built-in adhesive on the lights plus a few dabs of CA glue. On the other side of the back, I glued down the in-line remote that controls the color modes, brightness, etc., then just duct taped the battery pack on, since it will need to be removed when the batteries run out.
All that, all that was left was to assemble the light box! One tip: make sure to avoid putting your screws into the groove where the glass is supposed to run. Don't ask me how I know... :)
Step 12: Enjoy Your New Fancy Light Box!
I'm really happy with the way this turned out. It will be perfect for my booth as craft fairs, but will also look great on the wall of my shop in the meantime.
If you liked this build, maybe think about subscribing to my YouTube channel! I put out new project videos like this one every week. Also, check out the build article on my website for some more details on this build.
Thanks, and I'll see you all next week with another project!
Johnny Brooke
@craftedworkshop
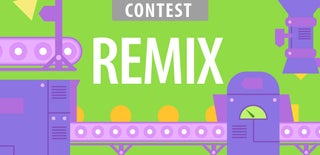
Participated in the
Remix Contest 2016
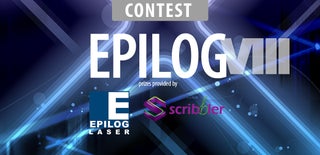
Participated in the
Epilog Contest 8
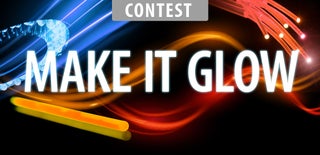
Participated in the
Make it Glow Contest 2016