Introduction: How to Create 3d Printable Articulated Sculptures
The availability of 3D printers and printing services is making it easier for aspiring hobbyists to get involved in creating sculptures, toys, and gadgets. With access to these tools, designers and inventors can rapidly prototype and evolve their ideas.
This tutorial is about creating articulated (movable) 3d printable figures, like my articulated crab, turtle, and crayfish. These models come right out of the 3D printer with moving parts - they don’t even need to be assembled!
Here's a quick video that shows how these figures are articulated.
For the articulation to be successful, the printer you choose should be able to create nested parts (example: a two-part hinge with enough spacing between parts so they don’t end up fused together). Currently, the best choices are laser-sintering printers that fuse layers of powder together, or SLA printers like the Formlabs Form 1+, that use lasers to selectively cure layers in a bath of resin. [I'm submitting this Instructable to the Instructables FormLabs contest, in hopes of winning their 3D printer so I can create more of my articulated figures. Being able to prototype all of my creations at home is something I've wanted for years!]
However, even if you don’t have a 3D printer, fear not! Shapeways is a great company that I use handle the 3D printing. After going through the steps of this tutorial, you’ll have a 3d model that can be sent to Shapeways for them to do the printing for you.
Step 1: Getting Started: Choosing a Subject
There’s really no limit to what you can model and print. To start off, I recommend designing something that is simple and small, just to get the hang of the process first. If you’re like me, you might want to create insects or crustaceans. For this Instructable, I'll use the shore crab as an example. I used to catch these little crabs in California whenever we visited the tide pools. A crab or spider might be a good starting point if you like small creatures: they have many pairs of similar legs, making it easier to model on the computer.
Step 2: Using References and Drawings
Like any sculptor, we want to become very familiar with our subject. If I’m making a model of a real-life creature, I go to Google images for reference pictures. Sometimes I find shells on the beach or natural history museums that help with the creation of a more accurate figure.
If you’re working on a fantasy or science fiction creation of your own design, it’s a good idea to draw a lot of sketches from various angles.
Having your reference pictures at hand, draw scale pictures of the figure you want to create. Graph paper is a very useful tool for understanding the scale of the model and keeping the right proportions when you redraw the model on computer.
Step 3: 3D Modeling: a Brief Introduction to Wings3D
Before we start 3D printing, we need to create the computer model. If you’re already familiar with a CAD (Computer-Aided Design) program, many of the following techniques will be applicable, and you can use the program of your choice. If not, I recommend using the free, open-source program Wings 3D. It’s a bare-bones, mesh modeling program that can do a lot. A computer mesh is a simple type of computer model, where connected vertices form shapes in 3D.
- Download and install Wings3D from wings3D.com.
A full Wings3D tutorial is outside of the scope of this Instructable, but in the next step, I will try to cover a few of the basic tools. If you'd like to learn more, Wings3d user puzzledpaul hosts the Wings3D User Manual, which I recommend having at hand, when you are modeling. His site also has a good number of tricks for more advanced usage of Wings3d.
Step 4: A Quick Computer Modeling Tutorial
When you open Wings3D, you will see an interface like the first image.
There is a grid in the main window; this can be treated like the “floor” of the virtual space. Each square of the grid is one “unit” long, which for the sake of this Instructable, we will consider to be equal to one millimeter.
When you right-click in the modeling area, you will see a pop-up menu like the fourth image.
Here you can see all the primitives, or shapes, that wings allows you to start with. Let’s start with a cube.
Now, orbit around the cube by clicking the middle mouse button (or alt+click on a Mac) in the empty space around the cube, and then dragging the mouse around. click again using the same button to exit the view/orbit mode. This function will be very useful as you model, since you’ll need to change your point of view frequently. A few other tricks to changing the view are to hit “o” which toggles the perpective or orthogonal mode, and the “x” “y” or “z” keys which align the view with these axes, respectively (so that you can view the side, top, or front views of your model.
You will notice at the top of the screen, there are four icons of a cube (third image). One cube has two vertices highlighted in red, the second cube has an edge highlighted, the third cube has a highlighted face, and the fourth cube is all red. These icons indicated which “selection mode” you are in. If the first three icons are boxed, that means you will be able to select vertices, edges, or faces. If only one of the boxes is highlighted, you can only select that type of geometry (for example, vertices). The fourth box, when selected, limits the selection to bodies, or entire parts.
Hover over the different parts of the cube you just created. You'll see different parts glow green as your cursor moves over them. If you click on a vertex, the selection mode goes to "vertex" and the vertex you selected glows red. Hit the spacebar to return the selection mode to "vertex + edge + face" and deselect anything you have selected. Try this with edges and faces too.
More things to try:
- select a vertex and right click, and select "move" from the popup window. Notice that You can see the different options for moving a vertex; you can move it in any of the axial directions, normal to the surface, or freehand. This functions similarly for vertex, edge, face, or body mode. While you are moving, try hitting "Tab", a window will pop up so you can specify exactly how much you want to move a feature. This "Tab" option works for most of the geometry tools.
-select a face and click "rotate". Do the same for the other selection modes. Just like with "move", you can rotate things about the x,y,z axes, or about the normal.
-select an edge, or face, and click "scale". This scales the size of the given feature.
-select a face and click "extrude". This is a useful tool for adding features to a 3D model.
-select a face and click "inset".
-select two vertices not connected by an edge, and click "connect" or type "c". Try the same with two edge.
-select a vertex or edge and hit the "Delete" key.
Trying all these functions and experimenting with the ones I have not mentioned will help you get familiar with the Wings3D software. Take your time and challenge yourself to create various models, like human faces, spaceships, etc. It doesn't necessarily have to be something you want to 3D print!
Step 5: Modeling Blocky, Then Smoothing the Model
Since Wings3D is a mesh modeler, by necessity all shapes are composed of vertices and hard edges. This may seem somewhat limiting, but it's actually very cool and useful for what we're doing. Wings has a built-in smoothing function, which allows us to model in a blocky mode and then smooth everything when we are about to export the model for 3D Printing.
For any given model, you can see how this works by hitting [Shift] + [Tab]. This activates the "Smooth Preview" mode so you can see what will happen when you smooth your model. Try this with a cube, you will see that it turns into a sphere.
There will sometimes be shapes that you want to make that retain hard edges; for this, you can specify the "hardness" of an edge. Select all the top and bottom edges of a cube and right click, select "hardness" , then "hard". Now try the quick smoothed preview. You’ll see the cube smooths into a cylinder.
As you model, get in the habit of toggling between the regular, blocky view and the quick smoothed preview.
It may take a little getting used to, but this will be handy later when we sculpt the organic form crab. You’ll be able to approximate the shape roughly with big polygons, but use smoothing to generate the form that’s more close to life, which you’ll use to 3D print.
Step 6: Modeling the Mechanical Components
Articulation is possible with certain 3D prints when separate parts of the same assembly (like the leg segments of a crab) are designed so that there is a little bit of space between each part. This distance, or clearance, between parts is determined by the capabilities of the 3D printer, and can be found in their specifications, or by experimentation.
- Create standalone hinges that conform to the tolerances allowed by the printer you plan to use. Whether you are using Shapeways or your own 3d printer, there should be a rated “minimum gap size” or “minimum clearance”, a “minimum wire diameter” and a “minimum wall thickness”. We’re going to design our hinges around these numbers. I use Shapeways to print in laser-sintered nylon for most of my figures, so I will use the numbers given on the shapeways website, on the materials section:
https://www.shapeways.com/materials/strong-and-fle...
According to the design guidelines,
- minimum clearance is 0.5mm
- minimum wall thickness is 0.7 mm
- minimum wire diameter is 1.0 mm
Create a cube. In “Face” mode use the “scale” commands on the top and bottom face so that the cube becomes a flattened box 4mm wide on a side but only 2 mm tall. View along the y-axis to make sure that the box has the proper dimensions. Now, with the top and bottom faces of the box selected, use the “inset” command create a frame around each face.
You’ll see that two faces remain selected. Right click and select “bridge”. The faces get connected across the middle of the cube, turning it into a rectangular tube. This will be outer part of our simple hinge. Create another cube that sits inside the tube, with a 0.5 mm separation between the cube and tube. Move the top and bottom faces of the cube normally so that the cube is longer than the tube, then extrude these faces upwards about 1mm. Then extrude the newly created faces of the extrusions, so that the model looks like a dumbell with a tube around the shaft. The wider parts of the dumbell will prevent the two pieces from coming apart.
You may also choose to use the extrude and bridge tools to form a loop connecting the ends of the dumbell.
Select both pieces in "Body" mode, right click and select "combine". This way, whenever you are in body mode, the two pieces will be selected and translated as one. At this point, our "hinge" is still very blocky, but that's ok: we will use the "smooth" function much later, after we've modeled our figure, to round all the corners and edges, and the hinge will be more rounded and functional then.
This is one of the most basic of joints you can create, a hinge that allows axial rotation between both pieces. You may want to create several different size variations of this joint, and other hinges and joints like it. Save each of these hinges/joints as its own .wings file. These will be the start of your components library, which we'll use to construct our articulated figure!
Step 7: Layout: Placing the Joints
Start a new wings3d file. This will be the master file for the figure. Go to file/merge, and select the hinge component you want to use. Use the copy tool to place the hinges to the right locations, according to the plan view drawing(s) you made earlier. Use the "rotate" tool in body mode to rotate the joints so that they all are oriented in the right direction. Note, you only need to do this for one side. Later, we'll use a mirror function to take care of the rest.
Step 8: Connecting All the Joints Into a Basic Form
Using the "bridge" tool, join faces of the joints, forming connected legs and claws. Use the "extrude" tool to make leg and claw tips. Create a cube in the center of the model, this will become the body of the crab. Swtich to "Body Mode" and "combine" all the objects. Use the "Virtual Mirror" on the midplane face of the body to mirror the entire left half of the crab. The way "Virtual Mirror" works is that any change you make to one side of the crab is perfectly mirrored on the other side. Divide the edges of the body into 5 segments and connect the vertices to split that face into 5 faces. Finally, connect the legs to the body using "bridge". This is now a basic crab shape with all the joints in the right places, all we have to do is sculpt it in wings to look more like a realistic crab!
Step 9: Sculpting
The rest of the modeling leaves a lot up to your own creativity! Now that the framework of the crab is completed, you can shape all the limbs to taste. You can use the right-click toolbar menus to modify vertices, edges, or faces. Feel free to delete vertices and edges where they are not needed, and to add detail where it belongs, using the divide, connect, and inset commands. Little features like eyes and spikes can be extruded and refined in the same way.
One useful tool for sculpting is the "tweak menu" under Tools/tweak/enable tweak. I like to turn it to "Move", which allows me to drag and drop vertices, faces, and edges using the cursor.
Depending on how realistic you want the model to be, you can add a lot of fine details, or you may go for more of minimalistic look with fewer vertices. Remember to toggle frequently between the normal view and the "Quick Smoothed Preview" using [Shift + Tab].
Finally, if you want your final model to have organic curves, select all items in "Body" mode and click "smooth" on the right-click menu. This tool, unlike the smoothed preview, actually smooths all of your geometry, so if you plan to keep editing your work, save a copy BEFORE smoothing. If you are ready to 3d print, export the file as a .stl, and fire up the 3D printer!
Step 10: 3D Printing
Depending on what you plan to use as a 3d printer, there is often a setup step before the printing actually happens. If you are using the Formlabs Form1+, you should open the crab .stl file that you just exported from Wings3D. The program performs several steps, including generation of support material (necessary for keeping the crab in place as it prints) and slicing (which turns the geometry into a set of motion instructions for the printer). Using the same software, you can send the instructions to the 3D printer, hit "go" and come back the next morning to the finished, articulated crab! It is that simple!
If you don’t have access to a 3d printer, or your home printer can’t print the detail required for articulation, you can use an online service like shapeways.com to do the 3d printing for you. You just have to set up an account (it's free) and upload the .stl file. Within a few minutes, it processes the file and displays the price to print in various materials. In fact, that’s how I got started, and I still use them a lot for complicated creations or prints in more exotic materials.
Even if you do have a printer, you might find that the Shapeways printers and materials are more varied and can handle finer detail. They can print in a variety of materials, even metals or ceramics (although for the latter, articulated joints are not possible. For articulated models, the available materials are the plastics and “sandstone”). If you like the automated quote by the shapeways site, you can pay with paypal and have the 3d printed model shipped to you in about two weeks.
(Pictures 1, 2, and 4 are from the formlabs website. Picture 5 is from the Shapeways website.)
Attachments
Step 11: Optional Step: Painting Your Models!
One of my childhood activities that got me into creating my own 3d printable figures was building Gundam model kits, which are often painted after assembly. Making these models to me is reminiscent of building those fun kits, with the added customizability.
The Formlabs resins and Shapeways nylon materials can be painted with acrylic paints and brushes or airbrushes. My favorite brand of acrylics is Tamiya, I tend to use a lot of thinner and clear washes to apply lots of translucent layers over the models; by layering the colors this way, I can more easily achieve a natural-looking effect. At this stage, it's very good to pull up the reference pictures as a painting guide.
To all my readers and aspiring hobbyists, I hope you found this tutorial useful! Please let me know if there's any part of the Instructable that you think needs clarification, and I'll edit the Instructable however I can to make it clearer. Making these figures can be challenging, but CAD and 3D printing tools makes the task a little more fun, and a little less crazy. Patience and practice really pay off - good luck with your creations!
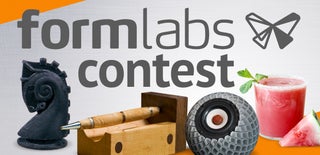
Participated in the
Formlabs Contest