Introduction: How to Make a Vacuum Chamber
I had a need for a particular project (mold for a 3d printed logo ) and several projects in the future where I needed to degass silicone as well as remove air from investment for casting in metal.
I currently have very little real estate in my garage so I needed a custom solution, also it didn't hurt that this project saved me a couple bucks along the way from purchasing a commercial unit.
Let's build a Vacuum Chamber!!
Step 1: Supplies for the Chamber of Secrets
To get started with this build you will need the following items
Cooking Pot:
I purchased the cooking pot from Bed Bath and Beyond. I was looking for a tall pot with a diameter that wasn't larger than 8" inches. The pot was made for steaming asparagus so it was tall and had the diameter I needed.
Asparagus pot
Polycarbonate Or Acrylic Sheet:
I stopped by my local plastic supplier and picked up a piece of 9" x 9" x 1/2" polycarbonate sheet. I decided to spend the extra dinero on polycarbonate as it's less prone to cracking and is much stronger than acrylic.
Silicone RTV Gasket Maker:
To create a seal for the lid I picked up some silicone gasket maker from the automotive store. The silicone RTV comes in different colors and I decided to go with the blue for personal preference.
Permatex Multipurpose RTV Silicone Gasket Maker
Fittings:
All the fittings such as the vacuum gauge and bulk head were purchased online. You can find equivalent parts at your local hardware store but I took the easy route after driving all day finding the above ;-)
1X 2-1/2" Oil Filled Vacuum Gauge -OEM - 1/4" NPT - Lower Mount - -30 Hg to 0
2X Female To Male Ball Valve 1/4" NPT
1/4" NPT Female To Male Ball Valve
2X Bulkhead 1/4" NPT
1/4" NPT Bulkhead
1X Branch Tee 1/4"NPT Female
Tee Fitting
Step 2: Layout for Your Day Out
Layout:
I traced the outside of the pot as a reference as the pot was not completely cylindrical.
I then use a center finder and mark a line on two opposite sides of each other to find the center of my material. In my case this was extremely easy to achieve as my polycarbonate was completely square.
I then locate my compass at the point in which the two lines intersect and draw a circle for the inter diameter to give me an accurate circle to locate my borders for my endmill. I mark a line for the outer diameter as well and try to space the circle about a 1/4" from my reference outline of the pot (You may need to increase this number if your pot is really oval), This ends up giving me a border of about 1/2" around the reference outline of the pot.
Step 3: Subtractive Manufacturing of Goodness
I head to my mill to start the drilling and cutting operations.
I use a scrap piece of wood and set my piece of polycarbonate on top
I drill a hole in the center with a drill bit about .30 thousandth of an inch smaller than the wood screw I intend to use.
I then screw the wood screw in and tighten everything in place
I drill a pilot hole in the center of my outline I drew earlier and follow with the same diameter as my endmill which is 5/8".
Please note that most end mills do not have the capability to center cut and do not like to be plunged straight down. This is why we drill the relief hole.
I insert the end mill into my mill and take a depth of cut of about 30 to 50 thousandth of an inch per pass. This is about the thickness of about 3 to 4 business cards.
Once the slot is complete I move the end mill half an inch from the slot to round the sides of the top (I used an endmill with center cutting which allowed me to plunge if you watch the video.
This part is strictly for esthetics and not necessary if you prefer a square top.
I then drill a pilot hole with an 1/8" drill bit for all my fittings,these can be located anywhere you prefer.
I switch the drill bit to a .266 (H) drill bit and drill the remaining holes to the clearance diameter of my fittings.
And were done with the milling and drilling.
Step 4: Seal the Deal With Some Silicone
I laser cut a squeegee out of acrylic to apply the silicone to the proper height to prevent the pot from being pushed down to far (you could easily make a squeegee without a laser)
I apply the silicon RTV and make sure that I apply a liberal amount. Once applied I then use the laser cut piece to set the height of the 1st layer of silicone.
I apply my second layer once the silicone has completely cured and smooth the top with a razor blade.
I apply some vaseline as a release agent as this is adhesive based silicone and put the top of the pot on the silicone we just applied.
Once cured I then pull the top off and remove the protective masking on the front and the back of the polycarbonate.
And were ready for the next step!
Step 5: A Fitting Day to Make Everything Stay
Since our top is complete it's now time to add the all the fittings to complete the chamber.
I added two ¼” npt bulk heads with neoprene washers to extend the fittings further down as my lid was a 1/2" of an inch thick.
Please note I add teflon tape to any connection with a thread and tighten firmly.
I grab the vacuum gauge and attach it to the furthest bulk head from the center.
I then use a tee fitting to attach two ¼” npt ball valves
I attach both ¼” npt ball valves to the tee fitting and tighten till I firmly align them with the knob facing the top.
I then use a quick connect fitting to easily attach and detach my vacuum pump
And were done with the Vacuum Chamber!
Side note: I decided to add a custom vinyl cut sticker as I felt the pot needed a little more style.
Step 6: Mold My Heart and Cast Me Away
Now it’s time to test the Vacuum Chamber!
Pouring the silicone mold:
I grab my part A and part B platinum silicone and mix vigorously. Once completely mixed I put the container in the chamber and pull my vacuum.
I’m using a 7 CFM vacuum pump for my chamber but you can go with a much lower cfm unit.
Once the vacuum pump is on I sit back and watch the silicone grow. :)
Please note silicone expands two to three times it’s volume so it’s ok to release some vacuum to prevent the silicone from spilling over the cup and into the container.
Once the vacuum has completely degassed the silicone I pour the silicone into a mold box with a 3D printed logo I made for my friend Nick Ferry who has a youtube channel here.
Once the silicone is completely cured I use 91% isopropyl alcohol to release the hot glue surrounding my mold box.I then pull the 3d print out of the mold and the mold is complete
Casting the resin piece:
I grab some talcum powder and apply it to my mold. This causes the resin to absorb finer details and reduces bubbles in the resin especially on corners.
I pour some urethane resin into the mold and move the resin around.
Once cured I pull the resin part out slowly from the mold, the remaining flashing can be removed with a finger nail or exacto knife,
That’s it finished bubble free resin copy!
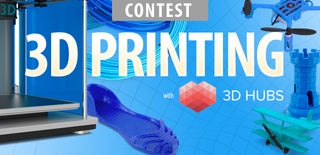
Participated in the
3D Printing Contest 2016